手仕上げ作業、手による加工の実際
2004年07月04日公開、最新の更新:2008年11月19日、FC2のアクセスカウンターを付けました。
最近は精密な機械部品や制御機器もカタログから拾い出して注文すれば2〜3日で入手できます。相当複雑な機械部品もミスミ等のフレキシブルな発注スタイルによって可能となりましたので、設計さえきちんとできれば、実験装置として十分な機能を有するものを完成させることができます。
しかし、実際に装置を組んでみると、設計ではこうしたかったが合わせてみたら別の方法が・・・などということは良くあることです。こうしたことに対応するためには、必要最小限の工作設備が必要となります。ここで解説するのは、こうした工作設備のうち、手仕上げ作業あるいは手による加工に関することがらです。
別稿で解説した旋盤やフライス盤などの本格的な工作機械がなくても、日曜大工的な卓上旋盤・ボール盤とハンドガスバーナーだけでNMRやダイリューションクライオスタットなどの低温実験装置を製作することは可能です。
この解説は、大学の実験装置を作る際に必要な基礎技術・技能としてまとめたもので、一般の工場や大量生産の現場とは異なることもたくさんあると思います。大学の研究室の大半は工作設備がほとんどない、あるいは極めて不十分な状況です。このような状況下においても、最小の設備で最大の効果を上げるためには、手仕上げ作業を如何に上手に活用するかが重要です。
これまでに経験した様々な状況を想定し、私たちの創意工夫も若干紹介しながら、手仕上げ作業、手による加工の実際を説明したいと思います。
やすりがけ
「やすり」は、鋼の表面に刻みを付けて、ものを削る道具です。
刻みの形によって、単目、複目、波目、鬼目(わさび目)などの種類があります。
さらに、複目には、目の粗さに応じて、荒目、中目、細目、さらに細かい油目の4種類があります。
そして、ヤスリの長さと形状による区別がありますので、全てを見ると非常に多くの種類があることが分かります。
金属工作で主に用いるのは「鉄鋼用やすり」で複目が一般的です。
波目ヤスリはプラスチックやアルミ材などの柔らかい材料を効率よく削ることができます。
やすりは非常に便利な工具です。ブラシ掛けなどによるメンテナンスを行い、綺麗な仕上げ面を得られるようにしておきましょう。
組みやすりは色々な形状のヤスリのセットです。5本組、7本組と種類が多くなるほど形状も小さくなります。写真は5本組やすりです。断面が、平、甲丸、四角、三角、丸の5種類です。
ヤスリの刃の部分がダイヤモンド砥粒でできているヤスリは焼きの入った鋼やセラミックス、アルマイト処理を施したアルミニウムの部品など、鉄鋼やすりでは加工できない硬い物も削ることができます。銅やアルミニウムなどの柔らかい金属を加工するときも目詰まりしないのでたいへん便利ですが、高価なことが難点です。
この写真はヤスリの刃の形状を示した物です。左の鉄鋼ヤスリは目の刻みがクロスになっています。アルミニウムなどの柔らかい材料を削ると目詰まりするので、下のようなワイヤブラシでやすり目に添って擦って目詰まりを除去します。これでも除去できない場合はケガキ棒などの先の尖ったもので丁寧に溝をさらいます。
波目やすりはアルミニウムやプラスチックなどの柔らかい素材を加工するのに向いています。特にアルミニウムの加工では削りとる量も多く目詰まりしないので作業がはかどります。
鬼目やすりは木工で良く使います。
ワイヤブラシ |
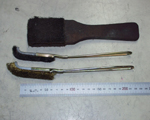 |
ワイヤブラシと総称していますが、上がやすりの目詰まり除去用です。
- やすりによる平面加工
金のこなどで切断した棒や板などの工作物の切断面を綺麗に仕上げたり、寸法を調整するためには、やすりがけ作業が適しています。
最初に「荒目」のやすりで大まかな形状や寸法を出しておき、「中目」や「細目」のやすりで仕上げます。
やすりの基本的な姿勢は、下の写真のように、足を前後に開いて脇をしめ、利き手で柄を、反対の手でやすりの先端を持ち、腰を前後に動かす要領でやすり面を押し出します。押すときに削れます。このとき、手や腕だけ動かすとやすり面が曲がってしまいます。
やすりの使い方 |
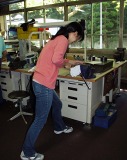 |
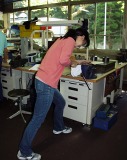 |
- やすりによるバリ取り加工(面取り加工)
「バリ」とは、加工途上で生じるエッジの「かえり」のことで、旋盤作業では加工手順の中に「バリ取り工程」を入れて綺麗に仕上げることができますが、切断加工やフライス加工では「バリ」が出ます。
この「バリ」は加工精度を損ねたり仕上げ面に傷を付けるので、必ず除去しなければなりません。
この様な「バリ取り作業」には「油目」のやすりが最適です。
単に加工手順上必要な「バリ取り」は「バリ」を完全に除去し、「糸面」(極小面取り)仕上げとしておき、全ての機械加工を終えた後で指定された面取りを施します。
写真のように、ヤスリを45°の角度を保ちながらエッジ部分を滑られます。全てのエッジが同じ幅で仕上がると角の部分は参画の頂点がそろって大変綺麗です。
やすりによる面取り作業 |
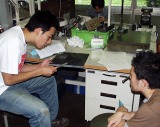 |
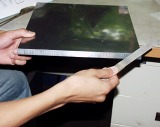 |
- やすりによる角穴、長穴加工
角穴や長穴の加工では、穴の大きさによって角やすり、丸らすり、半丸やすりなどを用い、小さい穴では組やすりを用います。
大学の実験室では電子回路の筐体やパネルの加工において、こうした加工が最も頻繁に登場します。
パネル加工では、電線が通る穴の面取りができていなかったり、バリがぶら下がっているような形でふらついていることを度々目にしますが、こうしたことは装置の信頼性を著しく損ないます。エッジで電線の絶縁物が切れてショートしたり、バリが電子回路上に落ちてショートするなど、思わぬ事故を引き起こしますので、しっかり「バリ取り」を行ない、バリを完全に除去しなければなりません。
- ダイヤモンドやすり
焼きの入った鋼などは「鉄鋼やすり」で削ることができません。こうした場合にはダイヤモンドやすりを用います。
ダイヤモンドやすりとは、金属基盤上にダイヤモンド砥粒を特殊金属メッキによって緻密に結合させたもので、「組やすり」の形態で市販されています。
実際に使用する場合は、「湿式研削」のほうが乾式より切れ味を長く保つことができます。
ダイヤモンドやすり |
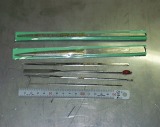 |
- やすりの柄
鉄鋼やすりは柄を自分で付けて使います。
付け方はやすりのくさび部分を柄の穴に入れて軽く叩きます。
力のいる粗加工ではやすりの柄を付けないと力が入りにくいので、必ず付けますが、面取り加工などの細目〜油目では力を入れるようなことはないので柄を付けずに使うことの方が多いでしょう。
やすりの柄 |
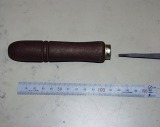 |
ヤスリのメンテナンス
ヤスリでアルミニウムを加工すると必ず目詰まりします。目詰まりしたヤスリをそのまま放置していたのでは次に使うとき困りますね。
ヤスリは、使った後、必ずワイヤブラシを使って切り屑を除去し、目詰まりを取り除きます。
ヤスリの目詰まりを取り除く方法を順に写真と共に示しますので、参考にしてください。
- ワイヤブラシで擦る
まず最初に、ワイヤブラシで擦ります。荒い目のヤスリには粗いワイヤブラシで、細かい目のヤスリには真鍮製のブラシを使います。写真のように、ヤスリの目に沿って(矢印の向きで)擦ります。
各種のワイヤブラシ | 目詰まり(赤丸の部分)したヤスリ | 矢印の方向にワイヤブラシで擦る |
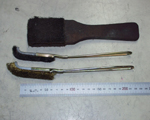 |
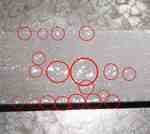 |
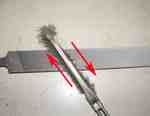 |
- 残った目詰まりは尖った針先で取り除く
ワイヤブラシでも取れない頑固な目詰まりは、先の尖った「罫書き針」などを使って、目詰まり部分をヤスリの目に沿って「こそげ落とす」ようにします。針先が尖っていないとうまく除去できません。根気の要る作業ですが、これを取り除かないと、綺麗なヤスリがけは出来ません。
ブラシ掛けで残った目詰まり | 罫書き針で目詰まりをこそげ落とす | 綺麗になったヤスリ |
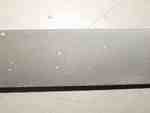 |
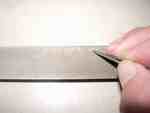 |
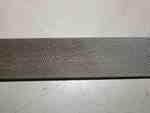 |
金のこ、糸のこの使い方
金のこ | 糸のこ |
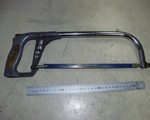 |
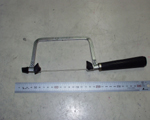 |
金のこは棒や板の切断に、糸のこはパネルやケースの穴加工などに必要な工具です。ここでは、金のこと、糸のこの使い方について説明します。
- 金のこの使い方
金のこの刃は押す方向で切れるように取り付けます。
手元の柄と弓の先の部分は四角になっていて、のこ刃を上下左右の向きに取り付けることも可能です。
加工物はバイスにしっかり固定します。固定が弱いと思いがけないときに加工物が外れ、作業者が怪我をすることがあります。
金のこによる切断作業では、切断の時に急に負荷が軽くなるので勢い余って怪我をすることがあります。僅かに残してのこ引き作業を終了し、手で折り切るぐらいがちょうど良いでしょう。
万力 |
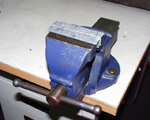 |
- 糸のこの使い方
金のこは押す方向に取り付けますが、糸のこの刃は引く方向で切れるように取り付けます。
糸のこも金のこの刃と同じように、上下左右どちらの向きにも刃を取り付けられます。
糸のこで薄肉パイプを切断する場合、刃が肉厚分を過ぎると強く引っかかり、無理に引くとのこ刃が切れてしまいますので、刃が引っ かかるようになったら切る場所を移動していきます。
糸のこによる切断作業では、刃が何回も切れることがあります。適度に油を刷毛塗りして潤滑すると刃のもちが良くなりますが、刃の 消耗はある程度仕方ないことなので、切れたら付け替えて作業を続行します。
糸のこによる溝加工 |
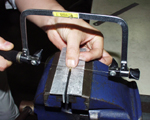 |
ケガキ作業
ケガキ作業は、穴位置を決めるなど、装置の完成度に直接影響を与える場合が多いので、正確にできるようにします。
ここでは、穴加工の中心位置を決める作業を想定して、定盤を用いたケガキ作業で位置を求め、それに続くポンチ作業で確定するまでを説明します。
けがき針 | けがき作業 |
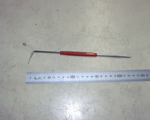 |
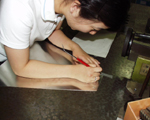 |
- 定盤を用いたケガキ作業
一般的には、定盤(基準平面)の上で、Vブロックやイケールなどの直角基準に工作物を押しつけ、トースカンやハイトゲージなどの高さ標準によって、要求される位置に必要な平行線を「ひっかき傷」として工作物上に刻みます。
工作物の基準面に直交する平面を底面として(90度回転させて)同様に線を刻めば、交点が目的の位置となります。
- ハイトゲージの使い方
ハイトゲージ | スクライバーを定盤面に合わせる | 目盛ゼロにする |
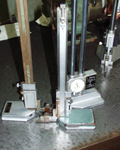 |
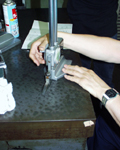 |
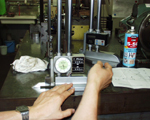 |
ハイトゲージはノギスと同じように主尺(メインスケール)と副尺(バーニアスケール)によって0.05mm程度の分解能をもつ、高さを測ったり決めたりする道具です。
定盤の面にスクライバー(刃先)の底面を合わせ、ゼロが合っていることを確認してから、目的の高さに刃先を合わせて、工作物にケガキ線を刻みます。スクライバーの刃先が欠けていたり、減っていると正しい高さにケガキ線を刻むことができないので、作業を始める前によく確認しておきます。
ハイトゲージの高さを見るときは、視差に十分注意します。目の高さをバーニアスケールの位置に合わせないと、メインスケールとバーニアスケールが同一平面ではないので視差が生じます。
定盤の上で操作している時に不用意に他の物に刃先をぶつけると刃先が欠けてしまい、正しいケガキ作業ができなくなるので注意します。
- スケール(直金尺)とケガキ針、コンパスを用いたケガキ作業
フライス加工をする前の材料の切り出しや、ボール盤による穴あけの位置を決める場合、けがき作業が必要です。
金工室には150mm、300mm、600mm、1000mm、1500mmの5種類のスケールを用意しています。
けがき針は鋼の細い棒の先端を鋭く尖らせた物で、金属の表面に傷を付けて目印にします。
金工室のスケール置き場 | 150mmのスケール | スケール裏面のインチとの変換表 |
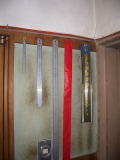 |
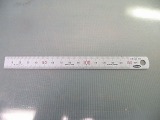 |
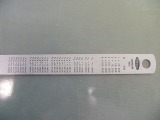 |
コンパスは中心の針とケガキ側の刃の間隔を任意に変えられるもので、微調整用ネジの付いた物が使いやすいです。写真の右側は普通のコンパス、左側は微調整付です。
このスケールとケガキ針で工作物に傷を付けて、目印とします。
コンパスはフランジのボルトサークルや円周や弧を描く他、二等分線を求めたり、基準線に直交する線を求めたりするのに便利です。
各種コンパス | コンパスとスケールで寸法を拾う |
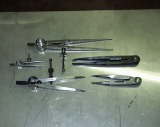 |
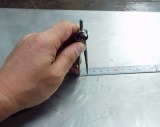 |
- センターポンチ作業
センターポンチ作業は、ケガキ作業で得られた交点に、センターポンチの先端を合わせ、ハンマーで打つ作業です。センターポンチを打たないと、ドリルによる穴加工ではケガキの中心にドリルを合わせることができません。
センターポンチには色々な種類があります。
左はハンマーで打つタイプ、右はオートポンチといって押し付けるだけでポンチを打つことが出来ます。
センターポンチ | オートポンチ |
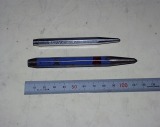 |
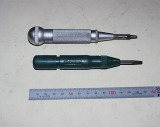 |
センターポンチは穴加工の大きさに合わせ、大きい穴の場合は大きく、小さい穴の場合は小さく打ちます。
センターポンチにの位置がずれてしまったときは、ずれた方向の反対側にすこしずれして軽くポンチを打ち、中心にポンチ痕を移動してから、最後にしっかりポンチを打ちます。
ポンチの位置を拡大鏡等でよく確認し、確実にケガキ線の真ん中(交点)にポンチ穴の中心が来るように心がけて下さい。
けがき線の交点にセンタポンチの先端をあわせる | センタポンチを打つ |
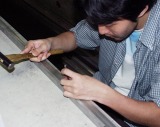 |
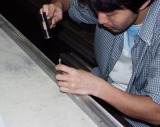 |
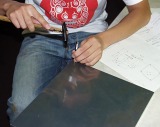 |
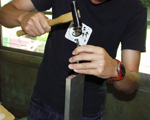 |
インデックス(割り出し機)の使い方
インデックスの爪交換 | フランジのボルト穴位置を割り出す |
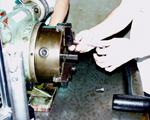 |
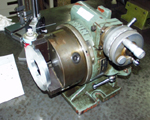 |
インデックスはフランジのボルト穴などの位置を割り出すのに便利です。
昔は何当分〜というような割り出し板にピンを入れて回すようなスタイルでしたが、今は角度目盛で割り出すものが多いようです。
この写真のインデックスは回転軸が水平と垂直の両方にできるので、そのままフライス盤のテーブルに置いてインデックス加工もできる便利な道具です。
このインデックスは最小角度分解能10秒と非常に高精度です。水平に置いたとき、定盤の基準面から150.0mmの高さに回転軸中心があります。
簡単な研磨作業
物理の実験室では度々研磨作業によって装置の部品を作らなくてはならないことがあります。
例えば、PM管のライトガイドや、光ファイバーの端末処理、光〜サブミリ波領域の反射鏡など、多種多様の素材・形状・精度・面荒さが要求されます。こうした部品をいちいち特別注文していたのでは時間やお金がかかるので、開発段階で大まかにあたりを付ける場合など、自分で研磨できればとても便利です。
ここではこうした要求に対して、設備的にも新たな投資を発生させないで研磨する方法とそれで実現できるスペックを実例と共に示します。
- 耐水ペーパー(研磨布)による研磨
耐水ペーパーを精密定盤に固定し、僅かに水を付けながら研磨したい表面を擦ります。このとき、あまり力を入れないのがこつです。
耐水ペーパーは研磨砥粒によって#400〜#2000程度まであり、荒い方から細かい方に順に変えていきます。
切削痕を取り去るような場合は荒いものを使い、適当に途中を省いてもかまいません。#2000まで行く前に、後で紹介するピカール(金属研磨ペースト)やダイヤモンドペーストに移行しても良いでしょう。
精密定盤 | 耐水ペーパーを使った研磨作業 |
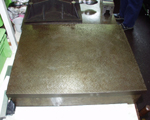 |
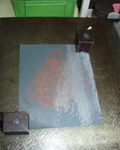 |
- 金属研磨ペーストによる研磨
金属磨きペースト=「ピカール」なる商品名のものがあって、真鍮、銅、アクリル樹脂の研磨に最適です。
前段階で耐水ペーパー等で刃物痕を取り除きます。これを怠ると、研磨痕の残ったまま表面荒さのみが細かくなり、返って見苦しい物になってしまいます。
柔らかい布に研磨ペーストを付けて軽く擦ります。円筒面は旋盤等で回転を与えながら研磨すると良いでしょう。
最後に新しい布で研磨ペーストを取り除くと、光沢のある研磨面を得ることができます。
- ダイヤモンドコンパウンド(フィルム)による研磨
金属磨きでは十分な面荒さを得られない場合、ダイヤモンドコンパウンドやフィルムを用いると、さらなる面荒さの向上が期待できます。
耐水ペーパーは#2000まで、金属研磨ペーストは#3000に相当しますので、それ以上の面荒さを実現しようとすれば、さらに細かい砥粒を用いる必要があります。
ダイヤモンドコンパウンドやフィルムは#7000(〜2μm)〜#15000(〜1μm)の砥粒に相当し、鏡面研磨を実現します。
- 研磨布による研磨(主に旋盤作業で)
旋盤作業で、円筒面を研磨仕上げするのに研磨布を用います。
ステンレス鋼や炭素鋼の場合は#150〜#240、真鍮の場合は#320〜#400程度がよいでしょう。
アクリル樹脂の場合は次に述べる耐水ペーパーの方が良いようです。
旋盤作業で注意したいのは、ネジ山を滑らかにするときに研磨布を用いるのですが、ネジの山が立っているところを直接指で押さえる様なことは非常に危険です。ネジにバリが出ていると研磨布ごと指も切ってしまいます。
内径ネジの場合は指を噛み込んで大怪我をする場合もあるので、木の棒のようなものに研磨布を巻き付けて使いようにします。
- 研磨パッド(ナイロンたわし)による研磨
研磨パッドはナイロンたわしのようなもので、ナイロンのスポンジに研磨砥粒を混入して成型したものです。
研磨砥粒の範囲が広いので、錆び落としのような荒い作業から、表面のつや出しのような仕上げ作業まで幅広く使えます。
研磨布 | ケンマパッド |
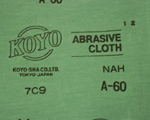 |
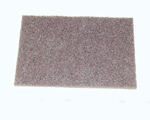 |
- ハンドグラインダーを用いた研磨
ハンドグラインダーは小型の軸付き砥石やバフ等で細部の研磨を行うのに適しています。
軸付き砥石には、ビドリファイド砥石、ゴム砥石、ダイヤモンド電着砥石で研磨砥粒#100〜#400程度まで、各種形状があります。
また、バフやブラシなども多くの形状であるので、様々な用途に使えます。
ハンドグラインダーは小型の高周波モータ駆動式とエアモータ式があります。どこでも使えるということでは高周波モータ式が便利ですが、長時間使うのには適していません。長時間作業する場合はエアモータ式が良いのですが、コンプレッサーによる高圧空気が必要です。
- バフ研磨
両頭グラインダーのようにモーターの両軸は左右に突き出ていて、そこにバフを取り付けて高速回転させるもので、バフに研磨砥粒をこすりつけた後、研磨する品物を回転しているバフに当てて磨きます。
研磨砥粒の種類と被研磨材との関係は以下の通りです。
名称 | 砥粒の種類 | 用途 |
青棒 | 酸化クロム | 真鍮、鋳物の仕上げ研磨 |
白棒 | アルミナ | ステンレス鋼、銅の中仕上げ研磨 |
トリポリ | 珪石(酸化珪素) | 鉄、真鍮、アルミニウム、プラスチックの中仕上げ研磨 |
曲げ加工(板金)
金属板に穴をあけたり折り曲げたりすることを一般に板金加工といいます。
ここでは、板金加工の中の「曲げ加工」について説明します。
穴加工はパンチ、リーマの項を参照してください。
曲げ加工には、板を曲げる「折り曲げ」とパイプやアングルを曲げる「ベンダー」があります。
- 板の折り曲げ
折り曲げはなかなか奥の深い加工です。曲げる板が厚くなるほど難しさが大きくなることや、板の熱処理や圧延方向などといったことでも状況が変化してしまいます。薄板(0.5mm程度)なら思ったように曲げられますが、板厚が2mm以上になると一回で完成品を得ることは不可能な場合が多いことも十分承知しておいて下さい。
しかし、設計上、ネジやスポット溶接などの接合部分を折り曲げ加工で可能にすると部品数も減り、組立も楽になるので、折り曲げ加工を利用できると非常に便利です。
折り曲げ加工では手順が大切です。形状によっては手順を誤ると加工不能となってしまうので、加工手順を十分に検討する必要があります。できれば実物大を薄板でシミュレーションすると良いでしょう。
以下に、折り曲げ器の使い方について説明します。
- 板厚に合わせて刃の隙間を合わせる
板厚より刃の隙間が狭いと、折り曲げ器の刃が傷みます。
板厚に等しい隙間となるよう念入りに調整します。
- 折り曲げ角度の調整
曲げ加工ではスプリングバックがあるので、直角に曲げたい場合は、直角よりも大きめに折り曲げます。
スプリングバック量は実際に折り曲げる板と同じものを試験的に折り曲げて確認し、あて板を戻したときにちょうど良い角度になるよう、折り曲げ量を調整します。
折り曲げ器での作業 |
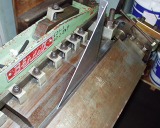 |
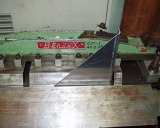 |
- 折り曲げによる寸法変化
エッジから10mmの位置にケガキ線を入れ、この線に押さえ板の刃先を合わせて折り曲げても、後で実測するとそのような寸法にはなっていません。実際にどれだけずれてしまうかを確認し、その分を織り込んでケガキを行う必要があります。
- 穴加工との関係
折り曲げ加工後に穴加工をしたいのは山々ですが、折り曲げ後では穴加工が困難になる場合があります。そうしたことも良く考え、折り曲げ加工と他の加工の順番を決める必要があります。
- 簡易折り曲げ器
ホーザンのカタログを見ると折り曲げ器が掲載されています。この装置は安価で、極めて実用的なので、ここで紹介します。
この折り曲げ器は作業台などにしっかり固定しないと本来の性能を発揮しません。
板の厚さに合わせる機構は偏芯キーによって行うことができますが、作りが華奢なので、銅やアルミニウムの2mm厚までしか折り曲げることができません。
押さえ板の切れ込みは、シャーシを作る最に必要ですが、位置が固定なので、このサイズのものしかできません。
以上のような制約はあるものの、1mm程度の銅やアルミニウム板ならば、簡単に綺麗に直角曲げを実現できます。
- 自作の折り曲げ器
折り曲げ器の原理は簡単なので、0.5mm厚程度のアルミニウム板を自由に折り曲げるために、折り曲げ器を紹介します。
基本的な構造
鉄の押さえ板は平角棒などから切り出します。
本体は力のかかり具合を考え、写真のように適当な構造となるようにします。
曲げ側の板は両側に軸を付けますが、銀ろう付けかネジ止めでいいでしょう。左右どちらかに、回転するためのレバー(棒)を入れ る穴をあけておきます。
押さえ板は本体上部かたネジでしっかり固定できるようにします。
使い方は以下の通りです。
- 板を挟む
押さえ板を外し、曲げたい板を本体に載せて曲げる位置のケガキ線と本体のエッジを合わせ、押さえ板が板厚の分オフセットした位置に来るように合わせて、ネジで固定します。
- 曲げ板をレバーで回転させる
曲げ板の穴に棒を突っ込み、必要な角度だけ回転させる。この時、スプリングバックがあるので注意します。
折り曲げ器での作業 |
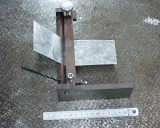 |
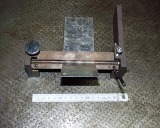 |
- 板を外す
曲げ加工が一回だけなら押さえ板のネジをゆるめるだけで加工物を取り出すことができます。何回も曲げるような複雑な物は、押さえ板を完全に取り外します。
- パイプを曲げる・・・パイプベンダー
銅やステンレスパイプ使って真空や高圧ガスの配管を行うことがあります。このとき、パイプを適度なRで曲げる加工が必要になります。このときに使う道具がパイプベンダーです。
配管用のパイプは外径が規格化されており、実験室でよく使う直径1/4インチ(6.35mm)や3/8インチ(9.53mm)は専用のパイプベンダーがあります。
使い方は簡単です。パイプベンダーにパイプを挟んでハンドルを回転させるだけです。角度の目盛りも付いているので、90°以外の角度にも対応できます。
配管作業では、パイプを任意の場所で切断するパイプカッターも併用すると便利です。
- ロール加工
ロール加工とは、板を丸めてパイプ状にすることです。そしてこの装置を3本ロールと呼びます。
手前の2本のシャフトはギアによって連結されています。この2本のシャフトの間に板を入れて後ろのシャフトで少し上にめげるようになっています。後ろのシャフトは上下できるように軸受けの下に調整ねじがあリます。最初は軽く曲げるように設定し、徐々に後ろのシャフトを上げて曲げのRを小さくしていきます。任意のRになればロール加工は終了です。
3本ロール |
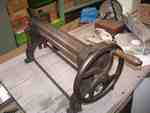 |
はんだ付けと銀ろう付け
はんだ付けやろう付けは装置を組み立てていく場合には、非常に重要な手法です。
はんだは100℃〜300℃で融ける鉛と錫を主成分とした合金、銀ろうは600℃〜800℃の融点をもつ銅と銀の合金で、他にもリン銅そう、ニッケルろう、金ろうなどもあります。
特に銀ろうは古くからの技術ですが、機械的強度も十分で真空漏れをおこしにくく、極低温でも超伝導にならないなどの優れた特徴から、低温装置を製作する場合にはなくてはならない基本的な技術となっています。
両者とも、金属の熱拡散作用を用いて金属どうしを接合する基本的な技術で、電気的にも機械的にもすぐれた性能を得られます。
ろう材と母材の金属熱拡散を安定して得るには、母材(被接合部品)表面の酸化物やその他の余分な物を取り去り、温度を上げても表面が酸化させないことが重要です。そのために、還元作用の強い物質を表面に塗布します。これをフラックスといい、はんだ付けの場合は塩化亜鉛や松ヤニ、ろう付けの場合は500℃以上で還元作用の顕著なフッ化物を主成分とした塩類(有毒であるがメーカーは成分を明らかにしていない!)が使われています。
両者とも接合作業のあとはフラックスを完全に除去する必要があります。残留フラックスは金属を腐食するので後に装置の致命傷にいたります。
棒状ハンダ | 糸状ハンダ | 銀ろう(φ1.6mm) | 銀ろう(φ0.8mm) |
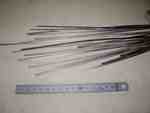 |
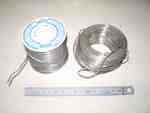 |
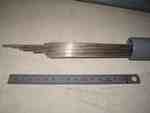 |
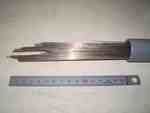 |
以下に、はんだ付け及びろう付け作業について解説します。
1ー1、はんだの種類
はんだは100℃〜300℃で融ける鉛と錫を主成分とした合金です。
- 高温はんだ
240℃〜300℃は高温はんだといって、はんだの中では強度も高く、銀などの貴金属を多く含有していているものは接合面の光沢もあり耐食性にすぐれています。
- やに入り糸はんだ
電気回路には糸状で中央にフラックスが封じ込められている「やに入り糸はんだ」を用います。以前は鉛65%錫35%融点240℃のものが使われていましたが、最近では有害な鉛を排除する方向で技術開発が進み、家電業界では鉛フリーはんだが主流となっています。用途に応じて2.0、1.6、1.4、1.0などの太さがあります。
- 共晶はんだ
特に錫と鉛の共晶はんだは融点183℃で、はんだの中では流れ性が最も良いものです。
- 低温はんだ
135℃以下のはんだを低温はんだと呼び、特に100℃以下で融けるものをウッドメタルと言って、温度を上げられない場合の接合に用います。低温はんだにはインジウムやビスマスなどの低融点金属を多く含有しています。
- アルミはんだ
アルミニウム用に開発されたはんだで、「やに入り糸はんだ」と同様に中央に特殊なフラックスが入っています。比較的融点が高いので熱容量の大きなハンダゴテを用います。
1−2、ろう材
ろう材は多くの種類がありなすが、金工室で用いているのは、銀ろう(BAg−1)です。代表的なろう材(AWS記号)の成分と性質をしめします。
- 銀ろう(BAg−1)
Ag=44-46%,Cu=14-15%,Zn=14-18%,Cd=23-24%
固相点=607℃、液相点=618℃
- リン銅ろう(BCuP−3)
P=5.8-6.2%,Ag=4.8-5.2%,Cu=残り
固相点=643℃、液相点=813℃
- ニッケルろう(BNiー1)
Cr=13-15%,B=2.75-3.5%,Si=4-5%,Fe=4-5%,C=0.6-0.9%,P=0.02%,S=0.02%,Al=0.05%,Ti=0.05%,Zr=0.05%,Ni=残り
固相点=977℃、液相点=1038℃
- 真鍮ろう(RBCうZn−A)
Cu=56-61%,Sn=0.25-1.2%,Pb=0.05%以下,Al=0.01%以下,Zn=残り
固相点=888℃、液相点=899℃
- 金ろう(BAu−1)
Au=37-38%,Cu=残り
固相点=991℃、液相点=1016℃
2、はんだ付け、ろう付けの熱源
はんだ付けは、はんだが融ける温度まで母材を暖めなくてはなりません。そのための熱源は、はんだ付けの規模や用途に応じて様々な方法があります。
- はんだごて
電気回路など、微細な箇所のはんだ付けには「はんだごて」を用います。
18W〜25W程度の小型のものは半導体回路のプリント基板など繊細な回路パターンのはんだ付けに向いています。デジタル回路でははんだこての漏電によってICが破壊されることがあるので、電気絶縁性の高いはんだごてを用いなければなりません。
制御回路など比較的熱容量の大きな端子にはんだ付けする場合は30W〜100Wの容量の大きなはんだごてを使います。
電子回路用はんだごて(23W) | 自作の温度調節器付きはんだごて台 | 市販の温度調整型はんだごて | 大形電気はんだごて(200W) |
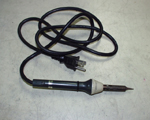 |
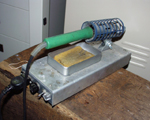 |
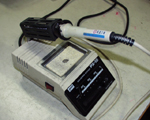 |
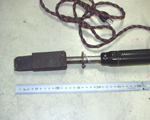 |
- ハンドガスバーナー
機械部品など熱容量の大きなもののはんだ付けやろう付けにはハンドガスバーナーを用います。ここで紹介するハンドガスバーナーは都市ガスと酸素を用いた物です。実際の作業や母材の熱容量などを考慮し、火口(3〜4種類あります)を交換できるので、小さい物から大きな物まで幅広く対応できます。
ハンドガスバーナーは火力の範囲が広く操作性も良いので後で述べる銀ろう付けの熱源として最適です。
ハンドガスバーナー | 酸素ガスを調整 | 火口を交換すれば調整範囲大 |
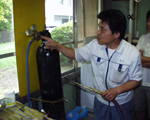 |
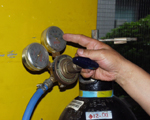 |
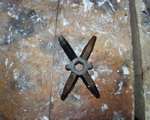 |
ブタンガス充填式やカセットコンロ用ガスボンベを使ったガスバーナーは、屋外作業や、緊急に実験現場で作業をしなければならないときに使いますが、熱容量の大きな物には不向きです。
- 卓上ガスコンロ
大きな物を暖めるには卓上ガスコンロを補助熱源として用いるのが便利です。加熱できる面積が大きいので部品全体を暖めるのに効果があります。火力が強いので暖めすぎないように注意する必要があります。
- 電気炉
全体を一様な温度に暖めて一気にはんだ付けする場合には電気炉が便利です。接合箇所にやに入り糸はんだを置き、電気炉ではんだが融ける温度まで加熱します。
銀ろう付けでは温度を800℃まで上げる必要があるので、そのような仕様の電気炉が必要です。
- 電気コンロ
電気コンロはお比較的大きな部品を接合するのに補助的な熱源として用いると便利です。
- カセットコンロは危険!
カセットコンロは母材の輻射熱によってカセットボンベが加熱され、爆発する可能性があるので使ってはいけません。
3ー1、はんだ付け用フラックス
- やに入り糸はんだの場合
微細なプリント基板等のはんだ付けにはやに入り糸はんだを使います。やに入り糸はんだは中央にフラックスとして作用する「やに」が入っているので、改め別のフラックスを使う必要はありません。
制御機器などの端子のはんだ付けは太めの「やに入り糸はんだ」を用います。はんだ付け後にフラックスを除去するのも同様です。
- プリント基板のフラックス
大量生産では、プリント基板のはんだ付け面にはんだの乗りを良くするため、「やに入り糸はんだ」に入っている「やに」と同様のものをアルコール等で希釈し、基盤全面に塗布しています。これらのフラックスは、はんだ付け終了後、完全に除去されています。
- 液状フラックス
機械部品などのはんだ付けでは、塩化亜鉛を主成分とする液状のフラックスを使います。刷毛やヨウジで接合部に塗布します。
腐食性が強いので、作業終了後は念入りに洗浄し、フラックスを完全に除去します。大学の実験装置では、このフラックス除去が不完全なために、端子等が腐蝕して接触不良を起こしたり、真空容器に孔が空いて漏れが発生するなど、やっかいなトラブルを起こすことが多いようです。
- ステンレス用フラックス
ステンレス鋼は表面に不動態形成があるので一般にははんだ付け不能とされていますが、特殊なフラックスを使うことによって可能となります。このフラックスはステンレス鋼の不動態(薄い酸化皮膜)を強い還元作用で除去するもので、先に述べた液状フラックスよりも腐蝕力が強いので、はんだ付け後の洗浄には十分な注意が必要です。ステンレスの真空容器では特に残留フラックスが濃縮されるので穿孔腐蝕や応力腐食割れの原因ともなります。
3−2、銀ろう付け用フラックス
銀ろう付け用フラックスの主成分はフッ化物ですが、各社のデータシートには成分表示がありません。但し、有毒である旨の表示があるので、取扱には注意が必要です。
大量に使う場合は、フッ素ガスによる健康被害の可能性があるので、換気に注意し、できることなら専用のフードを取り付けて積極的に換気して下さい。
以下に、代表的な銀ろう用フラックスの成分を表示します。
- 硼酸塩
ナトリウム、カリウム、リシウム塩などからなり、酸化物の溶解力・熱安定性よも良好、760℃で溶解し効力を発揮する。
- 硼フッ化物
カリウム、ナトリウム塩のフッ化物からなり、多くの点で硼酸塩とにている。
- フッ化物
ナトリウム、カリウム塩などのフッ化物からなり、ほとんどの金属酸化物と反応して強い還元作用を発揮するのでフラックスの主成分として最も重要な働きをする。活性化するとフッ素ガスが発生し、作業者の喉や目に刺激を伴う炎症を引き起こす恐れがある。
- 塩化物
ナトリウム、カリウム、リシウム塩などからなり、低温で溶解し、フッ化物基準フラックスの融点を下げる働きがある。
4ー1、やに入り糸はんだを用いた端子と電線のはんだ付け
はんだごてを使ったはんだ付けで一番重要なことは「こて先」の温度管理です。いつも一番使いやすい温度に保つことが、はんだ付けを上手におこなうこつです。
- はんだこての通電と、こて先の温度管理
はんだこて台にはんだごてを載せ、電気を入れます。こて先が暖まってきたらやに入り糸はんだを当て、溶け始めるのを確認します。
はんだが溶けたらこて先に十分はんだを載せ、一度スポンジで溶けたはんだを除去し、こて先にはんだが綺麗な銀色で薄く乗った状態にします。
この時の温度が一番良いので、以後この温度を保つように、適度に電気をON−OFFします。
はんだの乗ったこて先が紫色に変色(酸化)するのは温度が高すぎる証拠です。水を含んだスポンジにこて先を擦って温度を下げると共に、表面の酸化物を除去します。
- 電線をはんだ揚げする
電線の被覆を剥き、素線がバラバラにならないように少しよじってから、やに入り糸はんだと電線を左右の手で持って、はんだの小手先に当て、はんだが融けて電線の素線に十分はんだがしみこむことを確認します。これをはんだ揚げともいいます。
- 端子のはんだメッキ
はんだ付けしようとする端子にはんだごてのこて先とやに入り糸はんだを押し当て、はんだが融けて端子に乗るようにします。この時、はんだが多く乗りすぎた場合は、はんだ吸い取り器や吸い取り線で余分なはんだを取り除きます。この作業をはんだメッキと言います。
- いよいよ端子と電線の接合
はんだメッキされた端子にはんだ揚げされた線をからげ、そこをこて先とやに入り糸はんだを押し当てて、はんだを融かします。適度にはんだが乗ったらこて先を放します。
はんだメッキやはんだ揚げが十分できていれば、この段階で十分はんだ付けができているはずです。
- フラックスの除去
フラックスが端子の内部に進入して、電気接点を腐蝕するなどの問題を起こすことがあるので、フラックスの除去を行います。
綿棒にアルコールなどをしませ、はんだ付けした端子や電線とその周辺を擦ります。綿棒にフラックスが付いて来なくなるまで念入りに行います。
最近の電子部品の端子は内部へフラックスが浸透することのない密閉式のものも多いので、この工程を行わなくても良い場合があります。
- 熱縮チューブ等による絶縁処理
端子をはんだ付けした所は電気的にむき出しの状態です。ここに熱縮チューブをかぶせてヒートガンで暖めると、チューブが縮み、電気絶縁ができます。チューブを長めにとると、電線の補強ともなります。
熱縮チューブ | ヒートガン |
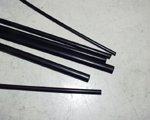 |
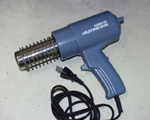 |
4−2、ハンドガスバーナーを用いたはんだ付け
ハンドガスバーナーを用いたはんだ付けで一番重要なことは、母材を暖めすぎないことです。
ハンドガスバーナーの炎の性質を良く知ることが大切です。
炎の芯の青白い部分は酸化炎といい、温度も低く酸化作用が非常にの強い部分です。外側の炎は還元炎といって、温度も高く炎自体に還元作用があります。従って、ハンドバーナーの炎ではもっぱら還元炎のみを使います。バーナーを近づけると温度が上がるように思われるかもしれませんが、火口に近い酸化炎が母材にあたると強固な酸化皮膜を形成し、はんだが乗らなくなります。
バーナー点火 | 炎を調整 |
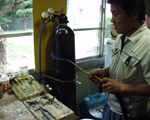 |
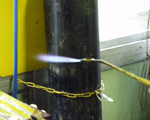 |
- フラックスの塗布
刷毛やようじでフラックスを接合したい場所に塗布します。
- ハンドガスバーナーによる加熱
ハンドガスバーナーの還元炎を母材にまんべんなくあてて、全体を暖めます。このとき、母材の表面に水滴が現れ、やがて蒸発します。この時の温度が丁度100℃です。
さらに暖めていきますが、もし可能なら感熱チョークなどで200℃程度の温度が確認できると良いでしょう。
- 棒はんだを盛る
母材が200℃になっていれば共晶はんだ(融点183℃)は十分融けるので、棒はんだを押しつけます。この時、棒はんだを押しつけたところが十分暖まっており、フラックスが活性ならば、はんだは融けて毛細現象で隙間に流れ込んでいきます。
もし押しつけたところのフラックスが蒸発してなくなっているならば、ようじなどでフラックスを追加塗布します。
はんだづけしたい箇所全体にはんだをながすのですが、まだながれていていない所にフラックスを塗るとはんだが後を追うようについて来ます。
- フラックスを除去する
徐熱したあと、フラックスを水で洗い流します。このとき、お湯を使ったり、クレンザーを使うと効果があります。
水洗いの後ティッシュペーパー等でよくふき取ります。
4−3、ハンドガスバーナーによる銀ろう付け
ハンドガスバーナーによる銀ろう付け作業を紹介します。
前にも述べましたが、ハンドガスバーナーによる便ろう付けは低温実験装置を作る上で欠かせない技術です。物性物理に進んだ皆さんは是非とも習得されると良いでしょう。
基本的なことは、はんだ付けの場合と同じです。
ハンドガスバーナーを用いたはんだ付けで一番重要なことは、母材を暖めすぎないことです。
銀ろう付けでは母材を800℃程度まで加熱させるのですが、加熱時間が多くかかりますので、勢い、ハンドガスバーナーの炎を近づけすぎて、酸化炎を母材に当ててしまい、強固な酸化皮膜を形成して、銀ろう付けを失敗するといったことが起こります。
加熱の熱源が不足する場合は、ガスバーナーや電気コンロを補助的に使い、効率よく母材を暖めるようにして下さい。
- フラックスの塗布
銀ろう付け用のフラックスはペースト状になっているので、銀ろう付けしたい部分にあらかじめ付けておきます。そして、手元に追加用のフラックスを少し出しておくのもお忘れなく!
銀ろう用フラックス | フラックスを塗布 | フラックスを塗布 |
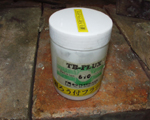 |
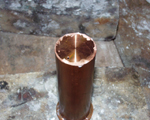 |
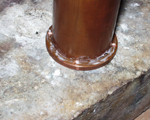 |
- ハンドガスバーナーによる加熱
ハンドガスバーナーの還元炎を母材にまんべんなくあてて、全体を暖めます。このとき、フラックスが融けて透明になると還元作用が発揮されて、フラックスで覆われている部分の酸化膜が取れ、綺麗な母材の色になります。この時、母材の温度は500℃を超えています。
この状態から、さらに加熱していきますが、母材が真鍮の場合は800℃を超えると母材自身が融けてきますので、暖めすぎに十分注意します。
フラックスが足らないと感じたら、手元に出しておいたフラックスを銀ろう棒の先に付けて、ろう付け箇所に押し当てます。
- 銀ろうの棒を押しつける
フラックスが活性化して還元作用による表面が現れたら、その部分を集中的に加熱し、銀ろう棒の先端をそこに押し当てます。このとき、銀ろうが融ける温度まで母材が加熱されていれば、フラックスが活性になった部分に銀ろうが融けて、毛細現象によって隙間に流れ込んでいきます。
もし押しつけたところのフラックスが不足して、酸化物が取れないようであればフラックスを追加します。
一旦融け始めると、フラックスが回るとそれを追いかけて銀ろうが回ってきます。
こうして、目的の箇所全体に銀ろうが流れればできあがりです。
- フラックスを除去する
十分に徐熱したあと、希硫酸液に10〜15分程度浸し、フラックスを除去します。
次に、母材に付いた酸を中和するために、苛性ソーダ溶液に浸してから、十分水洗します。この時、まだフラックスが残っているような場合は、お湯で洗うと綺麗に取り除くことができます。
希硫酸と苛性ソーダ |
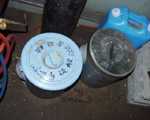 |
水洗いの後ティッシュペーパー等でよくふき取ります。
アーク溶接
ここでは比較的簡単な設備で実現できるアーク溶接について説明します。
鉄のアングルやチャネルを適当に組み合わせて大きな構造物を作る場合、アーク溶接ができると非常に便利です。
私たちの工作室には、アーク溶接の練習用として作った様々な架台があり、いまも重宝しています。部屋の僅かな隙間にフィットする棚や架台はスペースの有効利用にも貢献しますし、チャネルやアングルも切断すれば再利用も可能であることから、限られた予算や資財から新たな実験を立ち上げる際には大きなちからとなります。
溶接によって作った断材整理台 | 溶接によって作った旋盤アタッチメント収納架台 |
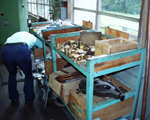 |
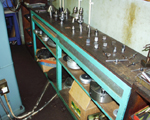 |
- アーク溶接特別教育
アーク溶接は労働安全衛生規則に則った特別教育を受ける必要がありますので、アーク溶接を行う前に、必ず受講して下さい。
- アーク溶接機
アーク溶接機は屋内に設置された物と、屋外でエンジンなどの発動機と連結した物とがありますが、どちらも基本は同じです。
- 溶接棒
アーク溶接では溶接棒の管理が大切です。私たちは大量に使うことが少ないので、少量を買い求めるほうが合理的です。溶接棒の保管は湿気を配するために、シリカゲルなどの吸湿材を入れた保管筒を作っておくと良いでしょう。
- 溶接設計
溶接で大きな構造物を作るときに注意しなければならないことは、部屋からの出し入れです。笑い話のようですが、これが以外と盲点となります。エレベータに入らなかったり、廊下の角を曲がれなかったりなど、あとで慌てないで済むように、運搬用の台車はどれを使うか、どこから何処まで運搬するか、その経路にどのような障害物があるか、エレベータなどの間口や奥行きは大丈夫か、スロープはあるか、重量制限はどうか、さらに遠くへ運ぶのならその方法は・・・などを加味して、製作しても良い最大の大きさ(モジュール)を決めてから、設計に移ります。
目的のものが大きすぎる場合は、途中で継ぎ足す構造を入れるなど、一工夫必要です。
- 溶接安全グッズ
アーク溶接は高温の火花の他にも、強烈な紫外線やヒュームといわれる煙が大量に発生します。
火花は直接身体にかかると火傷をおこします。紫外線は目や皮膚に炎症を、溶接ヒュームは塵肺をひきおこす危険性があります。従って、これらの被害を最小限に留めるため、防護に努めなければなりません。
溶接用手袋、腕カバー、溶接面、エプロン、脚カバー、安全靴は必需です。溶接の火花を周囲の人が直接見ることのないように、衝立なども必要でしょう。溶接ヒュームは専用の集塵機を用意します。
パンチ、リーマなどの板金工具
電子回路を収納するケースのパネルやシャーシの加工では、パンチやリーマなどの板金工具がたいへん役にたちます。
シャーシパンチは厚さ2mm(アルミニウム)までの板に、φ30、φ25、φ21、φ19、φ17の直径の穴をあけることができます。
リーマは小さい穴を序々に大きくする道具で、アルミニウムや鉄の薄板加工に重宝します。
ハンドニブラは角穴をあけるときに使います。一度に切れる面積は少ないのですが、角穴作業には欠かせない工具です。
文字盤の文字はテーキンを使って刻印します。
刻印の並びが曲がっていると見苦しいので、写真のように一度にたくさんのキャラクターを並べて一気に打つものもあります。
ハンドタップによるめねじ加工
ハンドタップによるめねじ加工のことを、「タップを切る」とか「タップを通す」といいます。
ハンドタップは普通3本セットです。ハンドタップの先端をよく見ると、先が細くなっているもの、少し細くなっているもの、そのまま先端までねじになっているものになっています。これを先タップ、中タップ、上げタップと呼んでいます。
ハンドタップ/上から上げタップ、中タップ、先タップ |
|
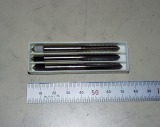 |
貫通穴の通しねじなら先タップを通すだけでめねじ加工は終了です。止まり穴にタップを切る場合は先タップを通してから上げタップを
通します。こうしてみると中タップはほとんど使いませんね。
ハンドタップには用途や被削材別に様々な種類があります。
ステンレス鋼などの難削材にはポイントタップ、止まりねじのタップ加工で穴の中に切りくずが残らないようにするにはスパイラルタップ、普通のタップでは届かない段下のねじ加工にはロングタップを使います。旋盤などでナットを作るときはナットタップ、というように使い分けます。
標準ねじ以外にも、細目ねじ、インチ規格(ウィットワース、UNC、UNFなど)、管用ねじなどの規格に対応したタップがあります。
ポイントタップ | スパイラルタップ | ナットタップ 標準タップ ロングタップ | スM26P1.0の細目ねじタップ |
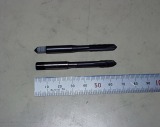 |
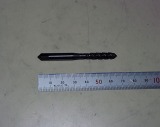 |
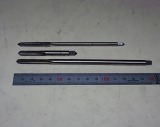 |
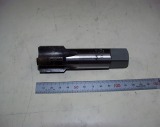 |
タップを切るとにはタップハンドルを使います。M3以下の作業では市販のタップハンドルは大きすぎるので、自分でハンドルを作ります。
T型タップハンドルはハンドル
タップ作業では、下穴にタップの先端を入れていくとき、正面と側面から交互に見てタップが垂直になっていることをよく確認することが大切です。少し回しては垂直を確認し、数回タップが回ったらそのまま回しでタップを入れていきます。
正面から見る | 側面から見る | 交互に見ながらタップを切っていく | 小径タップは慎重に |
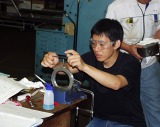 |
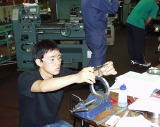 |
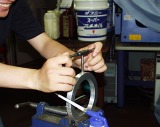 |
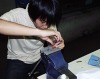 |
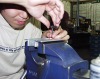 |
小ねじをハンドタップで加工する場合、タップを折ってしまうことが多いので気をつけましょう。特にM3以下は要注意、ステンレス鋼にM2のタップを立てようとすると、下穴加工の時に加工硬化をおこしていると大変難しい加工になります。途中まで入ったタップが進むことも戻ることもできず、結局タップを折ってしまう・・・という失敗をしたとき、下穴加工での加工硬化を疑ってください。
下の写真は先が折れたタップです。工作物には折れたタップの先端部分が残ってしまい、これを除去するのは簡単ではありません。
折れてしまったハンドタップ |
|
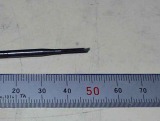 |
タップ作業は少量なら手で行ったほうが早く済ませることが出来ます。しかし、数が多いと忍耐を強いられる厳しい作業となります。このような場合は専用のタッピングマシンを使います。
こうした場合はロールタップを使い、塑性変形によってめねじを形成する方法もあります。
タップと同じような使い方でおねじを切る工具がダイスです。ダイスは写真のように丸いのですが、以前はさいころのように角だったようで、そこからダイスと呼ばれているようです。
ダイスもタップの刃先と同じようにテーパ部分があり、そちらから入れていきます。ダイスの表面にねじの規格が表記されている側が入り口です。
ダイスにもタップと同じようにダイスハンドルがあります。
インサートによるめねじの補強
アルミニウムや銅の部品にタップ加工したところを何回もねじを締めたり外したりしていると、ねじ部が除所にルーズとなり、最後にはねじが抜けてくるなどの不良を起こします。こうした場合、タップ部分を補強するのがここで紹介するインサートです。
インサートはメーカーによって色々名前が付いています(ヘリサート、スプリューなど)が、基本的な規格は同じなので、オーバータップや挿入工具などは共通で使えます。
例えば、M10の標準ねじならば、内径10mmでピッチ1.5mmの螺旋状になっており、先端に挿入工具を引っ掛ける爪が出ています。この爪は挿入後ポンチで取り除けるように工夫してあります。
インダートは呼び径とともに、有効長さを指定します。入手可能な長さは、呼び径をDとして、0.5D。1D、2D・・・となっています。
インサート | 挿入工具とインサートタップ |
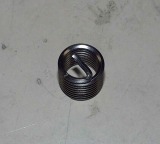 |
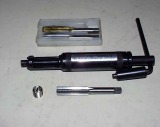 |
インサートの挿入作業を行なう前に、インサート挿入予定の穴にはインサートタップによってねじを切っておきます。
インサートタップを通した加工物 | 挿入工具とインサート |
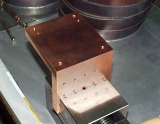 |
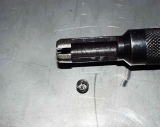 |
インサート挿入工具の先端をよく見ると、一番下側がねじになっていて、その上がポケットのようになっています。上から、中央の穴に沿ってハンドルにつながった軸から先割れの軸が出てきます。
インサートの爪の部分が下になるように、挿入工具のポケットにインサートを入れ、先割れの部分が爪を挟むように軸を降ろして少し右に回すと、インサートが挿入工具先端のねじに入っていきます。
挿入工具の下面にインサートの爪の部分が出るところまでハンドルを回します。挿入の準備はこれでOKです。
インサートを挿入工具のポケットに入れる | ハンドルを回してインサートを工具先端まで導く |
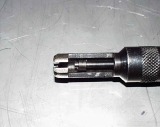 |
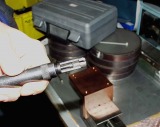 |
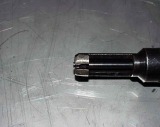 |
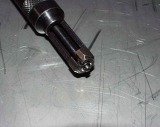 |
次に、挿入する穴に工具を垂直に立て、挿入工具を加工物に押し付けながら、ハンドルをゆっくり回していきます。
このとき、挿入工具のポケットが自分の正面に見えるような位置になっていると、インサートがどこまで入ったかを直接見ることが出来ます。
インサートの終端がねじ穴に半ピッチほど入ったところでハンドルを止め、挿入工具を抜きます。
最後に爪を折るために専用のポンチを入れて軽くハンマーで叩くと、爪が綺麗に折れてくれます。
挿入工具を加工物に垂直に立ててハンドルを回す | 挿入できたら専用ポンチでインサートの爪を切除 |
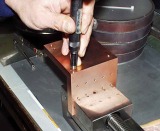 |
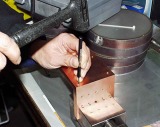 |
もし挿入しそこなったら、インサートを取り除くか、正規のタップを通します。