フライス加工の実例集
更新記録、2008年11月26日、タイトルを変更しました。
★ このページでは、機械工作実習ではなかなか経験できないような、汎用フライス盤による様々な工作方法、実例をたくさん紹介します。実習などの短い期間では経験できないことも多いので、実習修了者はこれを参考にして下さい。
金工室で普段あまり経験することのない、面白い加工なども紹介していきますのでお楽しみに!
ここで紹介するのは、加工専門業者のみなさんや町工場等で行なわれている方法とは異なり、大学の教育・研究において失敗の許されない加工や、学生さんが自分の実験装置を作ったり改造したりするための、安全第一に作業を行なうことを目的としたものです。
そのために、効率的ではありませんが、汎用工作機械の基本的な技術や工作精度を出すためのノウハウを多く含んでいると思います。
最近では汎用フライス盤を自在に操って高精度の加工を実現できる職人さんもめっきり減少したと聞いていますので、私たちのつたない経験が、プロのみなさんの参考になることもあるかもしれません。このHPをご覧になったみなさんからのご意見をお待ちしています。
まず最初に、一番良く使う汎用の縦フライスの加工例を紹介します。何れも基本的な加工ばかりです。
ここでは、工作物の様々な工程方法、フライス盤特有の刃物の紹介、そして、加工する場合の座標の取り方などを紹介します。これらの項目は横フライス盤やNCフライス盤でも同じですので、参考にして下さい。
このPAGEについてのご意見は kawai*tech7.sci.nagoya-u.ac.jpまでお願いします。(スパム防止のために@を*で表現しいますので、この部分を書き換えてください)
精密バイス(ミーリングバイス)を用いた加工
精密バイス(ミーリングバイス)とは、フライス盤用のバイス(万力)のことで、口がねやあごの部分が精度よく作られており、材料をバイスに加えた状態でフライス盤のテーブル移動軸と平行にセットできるものです。
小型精密バイスは固定するときに平行をださないとおけませんが、小物を精度欲固定するのに便利です。
マキノフライス専用バイス | 日立フライス専用(ツインバイス) | 小型精密バイス(横面で固定) |
 |
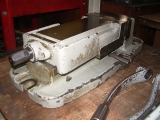 |
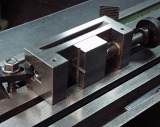 |
小物はバイスで固定する | バイスの横も利用した固定 | 同じ幅のものは2個同時に固定 |
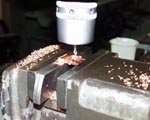 |
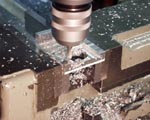 |
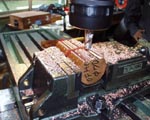 |
精密バイスの生命は口金部分です。誤操作によって口金部分を傷つけたり削ってしまうと、以後の加工精度に影響が出ます。口金は焼き入れされた硬い鋼になっているので、当然のことながら刃物も破損します。
従って、バイスの口金に刃物が当たらないように細心の注意を払って作業を進めることは当然のことです。
しかしながら、以下に示すように、金工室の精密バイスはかなり痛めつけられています。皆さん、是非ともこの様にならないようご注意下さい!!
この写真では、傷ついたバイス口金によってパラレルブロックまでも傷つけてしまった例です。
口金が破損している | 破損した口金でさらにパラレルにも傷が・・・ |
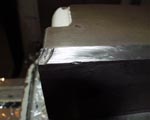 |
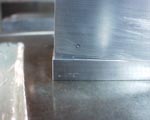 |
return to top !
ステップクランプを用いた加工
ステップクランプを用いて工作物を直接フライス盤のテーブルに固定します。ステップクランプを用いるときは必ず2カ所以上を固定します。この最、必ず下(テーブルと工作物の間)にダミーの板やブロックを挟みます。
大きな加工物の場合、加工物の穴などの形状を利用したり、ボルト締め用の穴をあけるなどして取り付けやすくします。
クランプの爪が当たる部分に薄いアルミ板などを挟んでおくと加工物に傷が付きません。
ダミーの板と一緒に固定 | 貫通加工でなければダミー板は不要です |
ブロックを下に入れて固定 | すて穴を利用して大きな板を固定 |
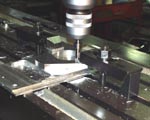 |
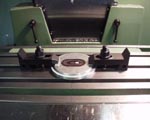 |
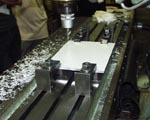 |
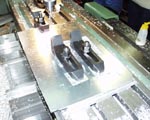 |
スクロールチャックを用いた加工
外径の丸い円盤のような形状のものを加工する場合は、スクロールチャックをステップクランプによってテーブルに固定すると良いでしょう。
スクロールチャックの生爪を用いたり、ジグを用いることによって、旋盤と連携した複雑な加工が可能となります。
スクロールチャックを用いた固定 | スクロールチャックの生爪を用いた固定 | スクロールチャックにジグを介して固定 |
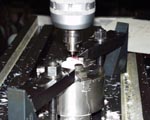 |
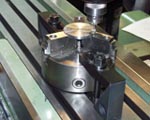 |
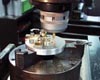 |
ツインバイスを用いた長物加工
長い工作物を固定するときはツインバイスを用います。ツインバイスは固定側の口金のYとZの座標が一致するようにメーカーの工場で調整されたもので、フライス盤のテーブルに並べて設置するだけで長い工作物を精度よく固定することが出来ます。
ツインバイスを用いた固定 |
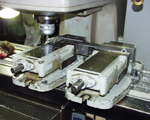 |
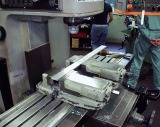 |
傾斜テーブルを用いた45°傾斜面の加工
傾斜テーブルを用いた傾斜角加工を紹介します。
写真の例はいずれも45°の角度です。この固定方法はセッティングに時間のかかることが難点ですが、強力に工作物を固定できるため作業効率をあげることができます。
エンドミルの底刃を使った加工なので、ダウンカット・アップカットを気にせず安全に加工できるメリットもあります。
傾斜テーブルに直接固定 | 傾斜テーブルにスクロールチャックを固定 |
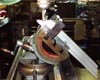 |
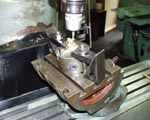 |
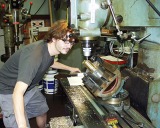 |
その他の方法による傾斜面の加工
板の一辺を45°にしたいとき、精度を要求されない場合は、Vブロックを用いてミーリングバイスに固定できれば簡単に加工できます。
同様に、ステップクランプによって45°に固定すれば、大きな面取り加工も楽にできます。
Vブロックを使った加工 | ステップクランプによって45°に固定 |
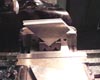 |
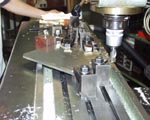 |
この他にも、ミリングバイスのスイベルを45°回転させたり、インデックスを用いて回転角を決める方法もあります。
インデックスを用いた加工
インデックスを用いることによって、多角形棒や円柱の側面に正確な角度で複雑な加工が可能となります。
インデックスを用いた固定(横軸) | インデックスを上に向けた固定(縦軸) |
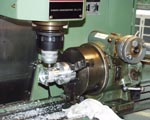 |
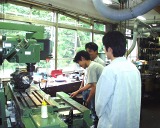 |
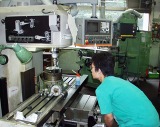 |
イケールを用いた加工
イケールは工作物を基準面から直角に保持する工具です。定盤の上では板にけがくときの背板となりますが、フライス盤のテーブルに載せれば大きな円筒状の工作物も保持することができます。
イケールを用いた固定 |
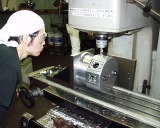 |
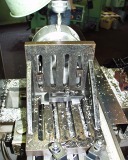 |
return to top !
ダイヤルゲージによる平行面(垂直面)の出し方
フライス盤のテーブルに工作物を取り付けるとき、平行の基準がない場合はダイヤルゲージを使ってテーブルの横や縦の動きに対する平行・直角を見ます。
ミーリングバイスなども、裏にキーのない場合は取り付け時に平行をかくにんする必要があります。
しっかりしたマグネットスタンドにダイヤルゲージを取り付け、変位を見て、平行や直角になるよう取り付けるものを微調整し、そろったならばしっかり固定します。ねじを締めると動く場合があるので、ねじを締めた後も蚊ならず確認しておきましょう。
ダイヤルゲージでバイスの平行を確かめる |
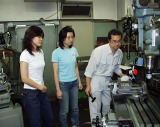 |
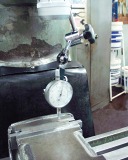 |
Tスロット溝とブロックによるX軸平行基準の出し方
大きい加工物を固定するときはテーブルのX軸(横送り)と平行に工作物を取り付けなければならないことがよくあります。こうしたときに、Tスロット溝にぴったり入るブロックやテーブル背面にマグネットベースを取り付け、その面に工作物を沿わせることでX軸との平行をとります。
この方法は切りくずなどを挟まないように注意するだけで比較的簡単に平行をだすことができます。
精度を要求する場合はブロックに沿わせた後、ステップクランプを仮締めして、ダイヤルゲージで平行を確認すればよいでしょう。
Tスロットにブロックを入れたところ |
ブロックを基準にして平行面を出す | マグネットベースで平行を出す |
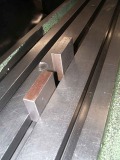 |
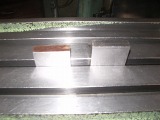 |
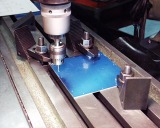 |
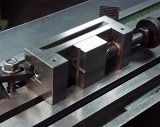 |
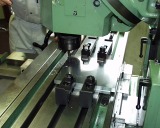 |
return to top !
団子針による加工原点の求め方
団子針とは、文字通り粘土と「針」を使った簡易な方法です。
針と粘土をエンドミルの先端に押しつけ、一度主軸を回転させて「針の先」を板などで軽く針先に触れてやると、エンドミルの回転中心に「針先」が倣う現象を用います。セットしてから僅か10秒足らずでおおよその加工原点を求められるので非常に便利です。
団子針を用いた加工原点設定 |
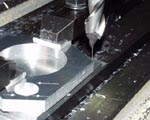 |
ポインターによる加工原点の求め方
ポインター、あるいはアキューセンターと呼ばれるフライス盤主軸の座標設計ジグを紹介します。
このジグは上下の円筒をバネによって引き合うような構造になっていて、600rpm程度の回転を与え、先端の部分を工作物やバイスの口金に近づけていくと、まだ当たらないときは振れているように見え、ピッタリ止まって見えるところからさらに大きく段が付くところまで変化します。この時に、段が付く瞬間テーブルの動きを止めると、その座標値が2〜3μmの精度で繰り返し再現性のあることが分かります。
この性質を利用して、主軸の中心を工作物の加工原点に設定するのですが、誰でも数ミクロンの精度で加工原点を決められることから、最近では多くの工場で使われているようです。
アキューセンターの外観 | エッジを求める | 円周加工の中心を求める |
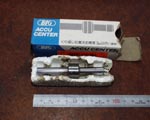 |
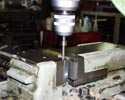 |
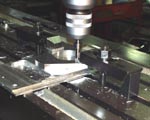 |
フライス盤で使う刃物
まず最初に、刃物を固定するためのツーリングシステムを紹介します。ここで紹介するのは縦型フライスのもので、コレットチャックのスリーブとドリルチャックやメタルソーなどを使えるようにショートアーバーが用意されています。
フライス盤も、旋盤と同様、多種多様な刃物があります。ここでは、フライス盤で使う「刃物」について、まとめて紹介しましょう。
エンドミルによる加工
今一番良く使われているのは「エンドミル」です。
エンドミルは、材質によって、ハイス(高速度鋼)と超硬合金とがあり、さらに形態によって、ソリッドタイプとスローアウェイタイプに分かれます。
さらに、刃数(1〜4)、材質別(レギュラー、アルミ、銅etc)、コーティングの有無や種類、長さ(レギュラー、ロング、エキストラロング)など、様々な違いがあります。
まず最初に紹介するのは、同じ2枚刃のエンドミルです。右から、レギュラー、アルミ用、TiNコーティング、TiCコーティングです。
右の写真は同じ2枚刃(φ16)の長さの違うエンドミルです。上から、レギュラー、ロング、エキストラロングとなります。
2枚刃エンドミル | ロングエンドミル |
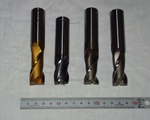 |
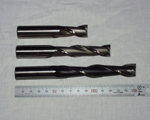 |
2枚刃エンドミルによる加工 | ロングエンドミルによる加工 |
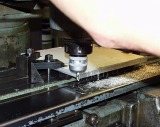 |
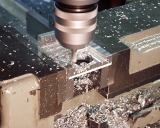 |
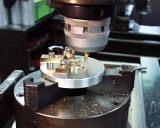 |
 |
次は変り種のエンドミルです。
ボールエンドミルは三次元曲面の加工に用います。特にR形状の精度を高くしたボールエンドミルは高価ですが、三次元加工の精度を決定付けるので、非常に重要です。
コーナーRカッターはエッジのR付け、Wアングルカッターは面取りに使います。
ボールエンドミル | コーナーRカッター | Wアングルカッター |
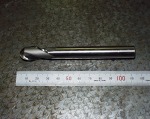 |
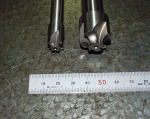 |
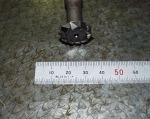 |
機械にとって重要な機構の一つであるあり溝の加工は、あり溝カッターを用います。旋盤刃物台の送り機構のように、機械の摺動による直線案内機構を作る場合に、あり溝カッターを用います。
あり溝カッター | 旋盤刃物台送り機構のあり溝 | 望遠鏡ガイドスコープ基部のあり溝 |
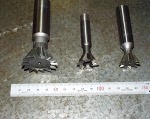 |
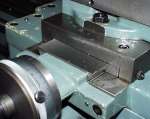 |
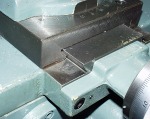 |
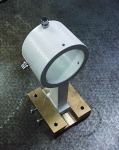 |
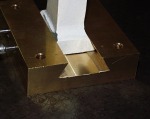 |
フライス盤のテーブルにはT溝が付いています。このT溝のおかげで、テーブルの自由な位置に工作物やミーリングバイスなどを固定ですので、工作機械には必要不可欠の構造です。このT溝を加工するための刃物がT溝カッターです。
次に紹介するのは、今は使われていない、古いタイプのエンドミルです。シャンク部分がブラウン&シャープ・テーパになっている所にご注目下さい。
旧2枚刃エンドミル | 鋳物用エンドミル |
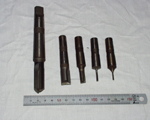 |
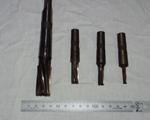 |
ブラウン&シャープテーパのエンドミルは使用中に時々抜け落ちる事故をおこしたそうです。
鋳物用のエンドミルは捩れ角が今のエンドミルと反対になっているのも面白いですね。
メタルソーによるすり割加工と横フライス
メタルソーは本来横フライスで使う刃物ですが、縦フライスでも使えます。狭い溝加工やすり割り加工では重宝します。
メタルソーは横フライスと同じように、アップカットで用いなければなりません。ダウンカットで用いると、刃物が工作物に食い込んでは存したり、場合によっては破損した刃物が作業している人に当たって思わぬ怪我をします。アップカットかダウンカットかをよく考えて、加工手順を決めてください。
ショルダーミルによる加工
ショルダーミルは刃先交換式の刃物で、様々なものがあります。
金工室ではアルミニウム合金を加工することが多いので、すくい角の大きいタイプばかりです。
旋盤の刃物と同じで、切れ味という意味ではこれらの刃物はハイスのエンドミルにかないませんが、効率よく大きな面積を加工する場合は重宝です。
さらに広い面積を一度に加工したい場合は、フルバックカッターを使います。刃物の直径が大きくなり、刃の数も多くなります。
マキノフライス用フルバック | NT50のフルバックカッター |
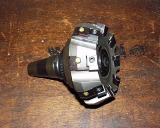 |
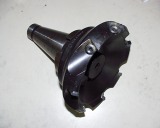 |
ショルダーミルやフルバックカッターを使うときは切りくずが勢いよく飛んできますので、必ず保護めがねを着用してください。
ヨルダーミルによる加工 | フルバックカッターによる加工 |
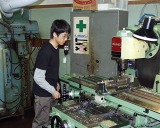 |
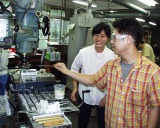 |
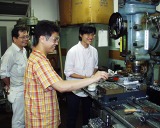 |
オートタッパーを用いたタップ穴加工
オートタッパーはタップ穴(雌ねじ)加工になくてはならないジグです。オートタッパーはタップを折損することなくタップのリードをうまく利用して雌ねじ加工を行うジグで、シャンクをモールステーパにしておけば旋盤の芯押台(テールストック)に取り付けて端面の雌ねじ加工にも使える便利なものです。
オートタッパーにはタップの呼び寸に応じた専用のホルダー(金工室にはM3〜M12まで完備)があり、タップが折れないようにメカニカルクラッチが仕込まれています。タッパー本体は主軸の前後に10mm程度スライドする機構が組み込まれており、タップのリードとの同期が不十分であってもそれを吸収できるようになっています。
従って、正転〜逆転が切り替えられる工作機械とオートタッパーを使うと、安全且つスピーディーなタップ穴加工が実現できます。
オートタッパー | フランジの角度割り出しとタッパーを組み合わせて |
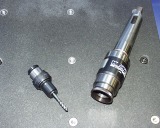 |
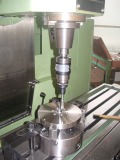 |
ここではフライス盤によるオートタッパーを用いたタップ穴加工について簡単に解説します。
- フライス盤の正転〜逆転機能を確認したら、オートタッパーを主軸に取り付け、穴位置にあわせます。
- 回転数をタップ加工できる回転(一般的に遅い回転)にします。
- 正転時タップのリードにあわせてテーブルを上げ(主軸を下げ)ていきます。このとき、タップのリードとテーブルの同期が不十分でも取り付け位置から上下10mm程度は吸収しますが、手動の目測でよいのでできる限り同期をとるようにします。
- 止まり穴の場合、タップが穴の先端に到達するとタップを掴んでいるホルダーのクラッチが効きカチカチと音を立てます。このとき、あわてずに主軸を一端停止し、テーブル(主軸)の送りも止めます。
貫通穴の場合はタップの切刃が十分貫通したことを確認したところで主軸とテーブル(主軸)の送りを止めます。
- 次に、主軸を逆転できるように、且つテーブルを下に(主軸を上に)送れるよう準備をします。
- 主軸を逆転と同時にテーブルを下に(主軸を上に)タップのリードに合わせて送ります。
- そのままタップが加工物から抜ければ一工程終了です。貫通穴タップの場合はこれで完成です。
- 止まり穴タップの場合は3番タップに交換して、同じ手順で作業を進めます。
慣れるまでドキドキしますが、タップホルダーのメカニカルクラッチの精度がよく、タッパーの不良による折損はありません。
この方法は縦型ボール盤にも応用できるものです。
横フライスによる加工
世界ではじめて発明されたフライス盤は横型でした。丁度旋盤の主軸チャックに刃物をとりつけ、刃物台に工作物を固定するような形でした。
横フライスで最も重要なことは、ダウンカット禁止ということです。使用する刃物は、何れも径の多きなものばかりなので、ダウンカットは極めて危険です。自分の加工がアップカットかダウンカットなのかをよく考えて作業を進めることが大切です。
本文はまだ準備中です!!
- アップカットとダウンカット
- アーバーと取付方法
- フライスカッターによる加工
- メタルソーによるすり割加工
横フライス用の刃物も紹介しておきます。
フライス盤は1820年頃アメリカのエリー・ホイットニーによって発明された機械です。最初は旋盤の主軸に刃物とを付け、刃物第二工作物を固定するような形でした。その後、主軸は1インチと決まり、アタッチメントやギヤの掛けかえで次々にギア加工やスパイラル溝加工など特殊な加工が出来るようになり、横型フライスは大きく発展しました。しかし、今では3〜6軸同時NC加工でこれらの加工を高精度に実現できることから、すっかり影を潜めてしまいました。
ここでは、少々時代がかっていますが、そうした刃物を紹介します。
金工室でも、メタルソー以外はほとんど使ったことがありませんが、Wアングルカッターなどは導波管のエルボを作った名残です。
正面フライス | 側フライス | 千鳥刃側フライス | 片角フライス |
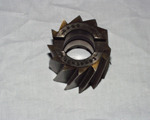 |
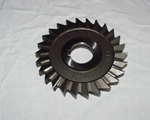 |
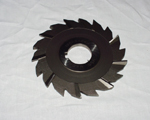 |
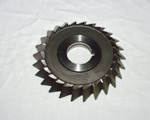 |
等角フライス | 内丸フライス | メタルソー | 大きなメタルソー |
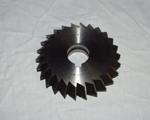 |
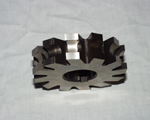 |
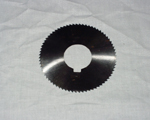 |
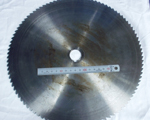 |
まだまだ多くの種類があって掲載しきれないほどですが、フライスへの取付は、アーバーと呼ばれる軸径1インチのアタッチメントを用います。
ショートアーバー |
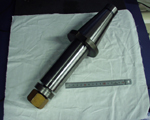 |
最後に、フライカッターを紹介します。これは簡単に自作することができるし、刃物を自分で調整できるので非常に便利な工具となります。
フライカッター | ブレード |
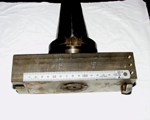 |
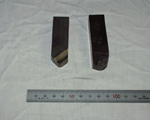 |
NC加工の例
NCとは数値制御のことです。簡単なプログラミングによってテーブルを自在に動かし、直線と円弧を組み合わせた複雑な形状の加工を行うことができます。
これまでに金工室で経験したNC加工の代表的な例を紹介しますので、参考にして下さい。
尚、金工室にある2台のNCフライス盤(日立と新潟)は基本的な操作方法が異なっていますので注意してください。
本文はまだ準備中です!!