汎用旋盤を用いた工作のいろいろ
★ このページでは、機械工作実習ではなかなか経験できないような、汎用旋盤による様々な工作方法を順次紹介します。実習などの短い期間では経験できないことも多いので、実習修了者はこれを参考にして下さい。
金工室で普段あまり経験することのない、面白い加工なども紹介していきますのでお楽しみに!
当ホームページについてのご質問、問い合わせはkawai@tech7.sci.nagiya-u.ac.jpまでお願いします。
最新の更新:2008年11月19日、FC2のアクセスカウンターを設置しました。
このPAGEについてのご意見は kawai*tech7.sci.nagoya-u.ac.jpまでお願いします。(スパム防止のために@を*で表現しいますので、この部分を書き換えてください)
旋盤作業の流れ
最初に、旋盤作業のおおまかな流れを紹介しましょう。
私たちは、おおよそ、以下のような順序にて、作業を行っています。これは私たちの工作室独自の考えに基づくものですが、多くの方々が気持ちよく使うためのルールとして決めている部分も含まれています。
- 機械使用の申し出と作業内容の説明
使用希望者は作業の概要を金工室スタッフに説明し、使用機械、工具等の指示を受けます。
この時、私たち技術スタッフは申請者の技量に応じて、作業方法に無理がないか等を確認した後、作業工程について必要なアドバイスを行います。
- 始業点検
使う機械がきまったら、その機械のハンドル類を回し、横送りやたて送りのハンドルを回して、機械が思うように動くかどうかを確認します。
普通の加工では旋回刃物台の送りハンドルが往復台(縦送り)と平行になっているかどうかをダイヤルゲージにて確認します。
次に電源を投入し、チャックにダミーをつかんで、主軸を回転させ、異常音などのないことを確認します。
- 使用刃物工具(バイト)を選択
使用する機械が決まったら、専用の工具台から作業に必要なバイト等の工具を選び出します。専用工具台に必要なものが見つからないときは、他の機械のバイトを借りることになります。
目的の加工が特殊な場合、適合するバイトが見つからないこともあります。こうした場合は、技術スタッフが新たにバイトを製作します。
また、適合するバイトが見つかっても、刃先が消耗していることも多いので、私たち技術スタッフが研ぎ直すなどの処置をします。
- 材料を固定する
旋盤作業では断面の丸い棒状の材料をスクロールチャックを用いて固定します。スクロールチャックは3本の爪が同時に動く仕組みになっているので、そのままチャックハンドルを回していくと自動的に材料の中心が出るように固定することが出来ます。
形状によっては材料を固定する方法に一工夫必要な場合があります。例えば薄肉パイプなどはそのまま掴みますと、三角のおにぎり型にパイプが潰れてしまいますが、この部分に芯を入れると潰す恐れもなく強固に材料を固定することができます。
- バイトを固定する
バイトの刃先高さを旋盤の主軸中心に合わせ、刃物台に取り付けます。このとき、センターやトースカンを有効に使います。
ヘールバイトや中ぐりバイトは僅かに刃先を高く取り付けておくのがこつです。
直径の大きなものの外周加工では刃先高さの精度はあまり重要ではありませんが、端面加工で材料の中心まで削る場合には厳密な高さあわせが必要です。
- 粗削り
端面加工や外周の粗削りを行います。このとき、ハンドル(横送り台、手送り台など)のカラーを回して目標の寸法との関係を付けていきます。
仕上げしろ0.1mm程度をのこして加工を進めていきます。
- 仕上げ削り
必要な寸法を出すために、最終の加工を行います。
寸法測定は必ず主軸を止めて安全を確認したのちに行います。必要な精度が出ない原因の多くは、仕上げ加工の前の測定の時に何らかのミスがあって、実際の寸法とは異なる値が出てもそれに気づかない場合や、バイトの切れ味が悪く目標の切り込みができなかった場合などです。
面取りの工程も忘れないようにします。
この工程は、あと回しにしてり落としてからでは同心加工にならず、見苦しくなることもあります。
エッジが鋭くないからと言って油断は禁物です。面取りしていないところで指を切ることはよくあります。
- 切り落とし
必要な部分を切り落とします。このとき、突っ切りバイトを使います。
突っ切り作業は材料の直径が大きいと難しい作業となります。
- 反対面の加工(粗加工〜仕上げ加工)
反対面を加工する場合、仕上げ面を直接チャックの爪で噛むと傷がついてしまいます。こうしたことを避けるには、薄い銅板を材料に巻いて、チャックの噛みあとがつかいないようにします。
このとき、切り落とした工作物が薄い構造の場合は、薄肉パイプの時と同じようにつかむためのジグを作るなどの状況に応じた工夫が必要です。
- 清掃と切り屑処理
全ての作業が終了したならば、機械の清掃を行います。清掃は次に使う人が不快感を覚えないよう、丁寧におこないます。
切り屑は、極力多の金属材料と混ざらないようにし、分別して専用のバケツへ入れます。
- 機械の整備
清掃と切り屑の処理が終わったら機械の整備を行います。
油の補給や不良箇所(もしあったら)の修理を行います。
- 作業報告(フライス盤を使った時も同じ)
機械使用簿に記帳します。
旋盤加工の準備その1−刃物台の調整
旋盤加工に入る前に、必ず確認しなければならないことがあります。それは「刃物送り台と主軸の平行」です。私はこの平行を確認せずに何回も失敗をしてきたので、今では旋盤作業の最初に必ず実施することにしています。
ダイヤルゲージを使って簡単にできますので是非実行してみて下さい。
最初に、ダイヤルゲージのマグネットスタンドを旋盤のベッドに装着し、ゲージの頭が刃物送り台の固定側に面に当たるようにセットします。このとき、往復台を左右に動かせば、刃物送り台の傾きを調べることができます。
傾いていればゲージの指示が変化するので、旋回台の固定ネジを緩め、ゲージの指示変化が最小のところで旋回台を固定すればできあがりです。
ダイヤルゲージをセットし、往復台を左右に動かす | ゲージの指示が変化しない所が刃物送り台の傾きもゼロ(主軸と平行) |
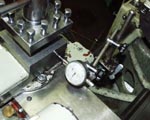 |
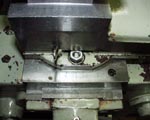 |
迅速に合わせるこつは、最初に旋回台固定ネジ付近のゲージの指示を覚えておき、往復台を右に送って刃物送り台基準面の端に来たときにゲージの指示が先ほど覚えたところに来るよう、旋回台を調整し、そこで固定ネジを締め直します。これなら一分程度の時間でこの作業を完了することができます。
旋盤加工の準備その2−バイト刃先高さの合わせ方
次に、目的の作業に最適なバイトを選び、刃物台に固定します。この時、バイトの刃先の高さを合わせる必要があります。
もし、高さが合わないと、バイトの逃げ角・すくい角が変わってしまい、正常な加工ができなくなります。但し、外径の大きなものを加工する場合は、神経質に高さを合わせなくても良いでしょう。
バイトの高さを調整するには「敷き金」を用います。「敷き金」とは厚さの異なる金属のスペーサーのことです。以下にバイト高さ合わせの手順を説明します。
- 旋盤の主軸の高さは「芯押し台」に「センター」を装着して、「トースカン」の先端とセンターの先端を正確に合わせます。このように、トースカンで高さを求める作業を「拾う」と表現することもあります。
- トースカンで拾った高さにバイトの刃先高さが合うように敷き金をバイトの下に敷き、できる限り少数の敷き金で合わせるのがこつです。
- バイトの高さあわせは使うバイトの数だけ繰り返すことになりますので、この作業を手際よく上手にこなせるようになれば、機械工作実習仮免は卒業!ですね。
- 刃物台には最高4本のバイトしか取り付けられません。それ以上付けたいときは、使う頻度の少ないバイトを外します。その時、折角合わせた敷き金なので、バイトと敷き金をセットで保存しておきます。
敷き金 |
トースカン |
トースカンでセンタを拾う |
トースカンにバイトの刃先を合わせる |
頻繁に行う高さ合わせ |
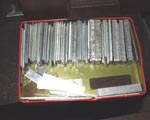 |
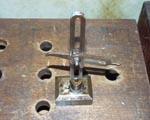 |
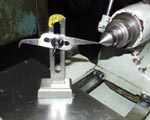 |
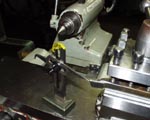 |
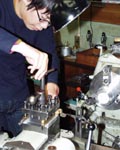 |
3、スクロールチャック(三爪)を用いた比較的簡単な加工
さて、いよいよ旋盤の加工偏に入ります。
旋盤で、最も基本的な作業はスクロールチャックを用いた加工です。以下に、各々の加工の様子を紹介します。
円筒面の加工は外径加工とも言い、剣バイトや片刃バイトを用いて円筒面を切削加工します。片刃バイトは端面加工や段加工にも使えるので便利です。
片刃バイトによる端面&円筒面の加工の例を写真に示します。
チャックの爪を反転(内爪から外爪へ)させると固定できる範囲が広がります。
内径加工は、基本的には外径加工と同じですが、外径加工に比較して難かしくなります。内径加工用のバイトは細長い構造で剛性が低いことや、加工部分が円筒内部で隠れてしまうことが多く状況が見にくいこと、切り屑のはけが悪いなど、悪条件が重なります。
長い材料を適当な長さで切断したい場合、幅の狭いバイトで切り落とす作業を行いますが、これを「突っ切り」と言い、この時使用する刃物を突っ切りバイトと言います。突っ切り加工は内径加工と同じく、比較的難易度の高い加工です。特に大きい径を切り落とすときには突っ切りバイトの突き出しを長くしないといけないので、そのようなバイトの刃先を成形するには熟練が必要です。
また、突っ切り加工では薄い刃先が深く材料に入るので潤滑性に優れた切削油の併用が必要となります。写真では油筆によって給油しながら加工を進めています。
片刃バイトによる加工 |
内爪&斜剣バイトによる端面加工 | 外爪&溝切りバイトによる溝加工 |
外爪&中ぐりバイトによる内径加工 | 内爪&突っ切りバイトによる切断加工 |
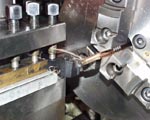 |
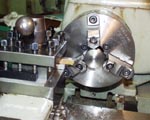 |
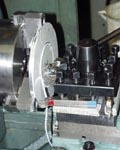 |
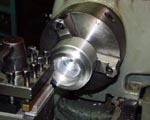 |
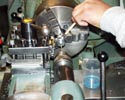 |
チャックの爪の交換は、スクロールチャックの爪の種類によって異なります。
一体硬爪タイプは内爪と外爪が用意されているので、爪の番号を間違えないように順に挿入していきます。分割爪タイプは、固定ねじを外し、爪を逆転させます。以下の写真は分割爪タイプの交換作業状況です。
固定ねじを緩める | 爪を外す |
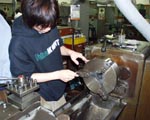 |
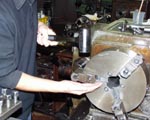 |
芯押し台の使い方とドリルによる穴加工
旋盤の芯押し台を使った穴加工は旋盤の基本操作の一つです。
旋盤の芯押し台は主軸の反対側の支えとして機能し、主軸の延長線上にモールステーパ(MT−4)のアタッチメントを取り付けることができます。芯押し台は左側のハンドルで主軸方向にアタッチメントを繰り出すことができ、この機構を使って穴開け加工や長い棒の端末支持を行います。
モールステーパは旋盤のアタッチメントとして規格化されたもので、ドリルチャック、センター、回転センタ、傘回転センタ、テーパシャンクドリル、スリーブ、ソケットなどをワンタッチで取り付け・取り外しすることができます。
これらのアタッチメントを紹介します。シャンク部分がおおよそ1/20程度のテーパ(円錐)となっており、この部分をモールステーパと言います。これらは芯押し台にワンタッチで脱着できます。
ドリルチャック | センター | 回転センター |
傘回転センタ | スリーブ |
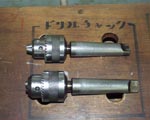 |
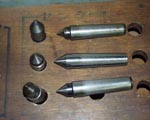 |
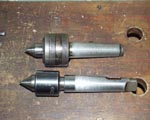 |
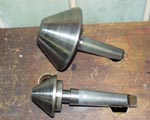 |
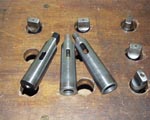 |
最初に、芯押し台の機能を用いた穴加工を紹介します。
ドリルチャックを芯押し台に装着し、センタードリルをドリルチャックで掴みます。
次に穴径が13mmまでならばストレートシャンクドリルをドリルチャックに装着して加工します。ドリルが入るときは送り機構のブレーキレバーを操作して適当な抵抗を付けると食い込み事故を防ぐことができます。
穴開け加工と同様の操作で、リーマ加工や面取りカッターによる面取り加工ができます。
大きな径のドリルの場合は、大きめのセンタードリル加工を行った後、ドリルチャックを外し、テーパシャンクドリルを取り付けます。この時、芯押し台のテーパとドリルが合うようスリーブを選びます。スリーブの装着はスリーブの後部をハンマーで軽く叩きます。スリーブを外すときは適当な大きさの「くさび」を穴に差し込み、軽くハンマーで叩きます。
センタードリル | 芯押し台と大径ドリル |
テーパシャンクドリルを用いた穴加工1 | テーパシャンクドリルを用いた穴加工2 |
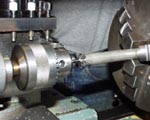 |
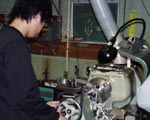 |
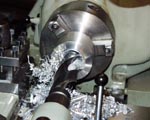 |
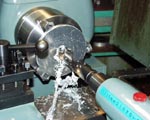 |
次に、回転センタと粘着板を用いた薄板円板やフランジの加工を紹介します。
この方法は、スクロールチャックなどでは掴めない薄い板状の加工物を丸く仕上げるのに便利です。粘着板の付いたアタッチメントを主軸側に装着し、芯押し台に回転センタもしくは傘回転センタを装着して、加工物(板)を挟みます。この時、芯押し台はしっかりロックします。もし挟み付ける力が弱いと、加工中に材料が飛び出したり刃物が破損するなどの事故を起こしますので注意して下さい。
薄板を同一寸法の円盤に仕上げるときは前後を別の板(少し厚め、5mm程度のアルミか真鍮)で挟むと良いでしょう。この場合、何枚か重ねても大丈夫です。当然厚さの異なるものを重ねても大丈夫です。
この方法で、厚さ0.1mm程度のリン青銅板の円盤を何十枚も一気に作ったことがあります。
粘着板と回転センタを用いた加工例1 | 粘着板と回転センタを用いた加工例2 |
粘着板と傘回転センタを用いた加工例3 |
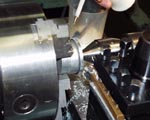 |
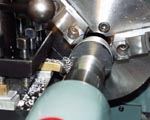 |
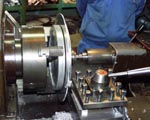 |
生爪を用いた加工例
生爪を用いた加工は、加工物の同心精度を必要とする場合や、フランジのような薄い加工物をしっかりつかみたい場合に効果的です。
生爪には二種類あります。スクロールチャックの爪が生爪と交換できるものと、三角生爪です。どちらも生爪を装着してから、爪の部分を工作物の掴み径と同じになるよう加工します。この時、スクロールチャックの爪の遊びが生じないよう、ダミーを銜えることが大切です。
「生爪による加工例3」ではカメラの接写用ヘリコイドユニットをつかめる形状に生爪を加工して、安全且つ精密にネジ加工を施したもので、このような複雑な形状も、生爪を工夫することにより、旋盤加工が可能となります。
三角生爪 | 三角生爪による加工 |
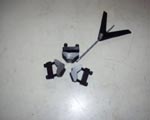 |
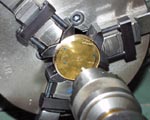 |
生爪 | 生爪に交換 |
生爪による加工例1 | 生爪による加工例2 | 生爪による加工例3 |
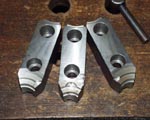 |
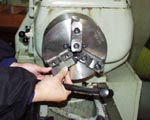 |
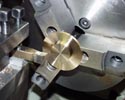 |
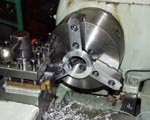 |
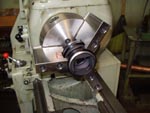 |
生爪の加工
生爪自体を加工するには、生爪を取り付けた後、下の写真のようにダミーを爪に噛み込んでチャックを締めた状態にしてから、中ぐりバイトによって爪を直接切削加工します。この時の加工径は生爪によってつかみたい工作物の直径に、深さは端面加工が可能なように、仕上げ寸法より僅かに小さくしておくのが良いでしょう。
このとき、中ぐりバイトのノーズ半径を極力小さくするか、「ぬすみ」を入れるなどして、生爪で工作物を掴んだときに端面や円筒面に隙間が生じないようにします。
以上の手順により、加工物の軸を狂わすことなく、反対側の加工も可能となります。
生爪でダミーを掴む | 生爪を加工(その1) | 生爪を加工(その2) |
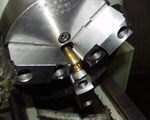 |
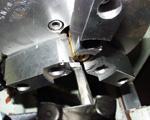 |
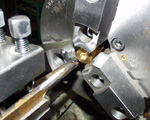 |
三角生爪も同様に、生爪部分にダミーを噛み込みます。このようにダミーを噛み込むのは、スクロールチャックのガタによる影響を少なくするためです。
コレットチャックを用いた加工例
コレットチャックは、主軸のレバーを一回操作するだけで加工物を固定したり外したりできるので、主に小径部品を沢山加工する場合に有効です。
また、スプリングコレットは加工物の外周全体に一様な締め付け応力が加わるので、工作物に爪の傷を付けないことや、つかみ精度(同心精度)が良いことも大きな特長です。
しかし、工作物の外径が変わるたびにコレットを交換しなければならないので単品物の加工では効率が良くありません。
コレットと加工物の外径が合わない場合はつかむことができませんので、他の方法(たとえば汎用旋盤と生爪を用いる)を考えなければなりません。
コレットチャックの主軸 | コレットチャック |
材料を直接つかむ | 治具を介した薄肉加工 |
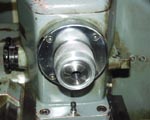 |
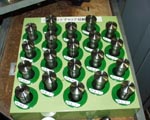 |
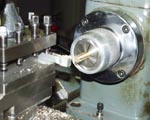 |
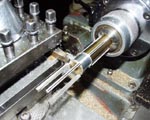 |
一番右の写真で紹介した「治具を介した薄肉加工」は、コレットチャックの高い精度(同心)を利用したもので、最終的に加工物の肉厚が70μm程度に仕上げることができました。この時の偏心は2μm以内を実現しています。この治具(真鍮製)と加工物は、摩擦抵抗のみで支持されるよう、クリアランスを極小にとっています。
四つ爪を用いた加工例
昔は四つ爪チャックしかなかったので、四つ爪チャックによる丸棒の芯出しは旋盤の基本的作業の一つでした。しかし、スクロールチャック(三爪)が普及してからは、大きな工作物を効率よく加工するために強力につかむ必要のある場合や偏心加工にしか用いなくなりました。
偏芯作業や四角い加工物の旋盤加工では、四つ爪チャックが必要です。偏心加工は重心が回転軸から外れるので、高速回転が必要なときは「重り」を用いて重心合わせを行ないます。
四つ爪チャックは材料に大きな力が加わるので爪が当たるところに薄いアルミ板などを挟むと、製品に傷が付きません。
四つ爪による偏心加工 | 四つ爪による直方体形状の製品の加工 |
四つ爪による板材の穴加工 |
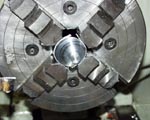 |
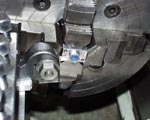 |
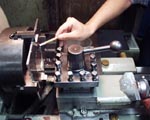 |
面盤を用いた加工例
面盤は比較的薄い板に旋盤加工する場合に必要です。面盤の長穴を利用してステップクランプ等で工作物を固定します。
面盤は初期の旋盤で普通に使われた工作物の固定方法です。
主軸に円盤状の板を取り付け、工作物を直接ネジで固定したり、固定金具で押さえつけます。
この固定方法は原始的ですが、自由度も高く、使いこなせると非情に便利です。
人工衛星などの複雑な部品を加工する場合は、面盤にあたる部分を旋盤加工して同芯性を確保したジグとすることで、普通旋盤でも1μm程度の加工精度を実現することができます。
このように、ジグを作ることは旋盤作業の適応範囲を拡大することになり、付加価値の高い工作を実現できます。
簡便なねじ加工
規格ねじは、タップやダイスを上手に使って加工した方が良いこともあります。
芯押し台にタッパーやダイスホルダーを付ければ良いだけなので、準備も簡単、ギアの掛け替えなどでピッチを合わす必要もなく、手早くできるところがミソです。
ダイスホルダーによる雄ねじ加工 | ダイスホルダー |
タップホルダー |
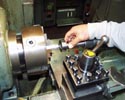 |
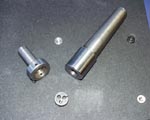 |
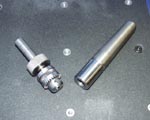 |
次に紹介するのは、オートタッパーを使ったタップ穴加工です。
オートタッパーはタップ穴(雌ねじ)加工になくてはならないジグです。オートタッパーはタップを折損することなくタップのリードをうまく利用して雌ねじ加工を行うジグで、シャンクをモールステーパにしておけば旋盤の芯押台(テールストック)に取り付けて端面の雌ねじ加工にも使える便利なものです。
オートタッパーにはタップの呼び寸に応じた専用のホルダー(金工室にはM3〜M12まで完備)があり、タップが折れないようにメカニカルクラッチが仕込まれています。タッパー本体は主軸の前後に10mm程度スライドする機構が組み込まれており、タップのリードとの同期が不十分であってもそれを吸収できるようになっています。
従って、正転〜逆転が切り替えられる工作機械とオートタッパーを使うと、安全且つスピーディーなタップ穴加工が実現できます。
オートタッパー | オートタッパーを使ったタップ穴加工 |
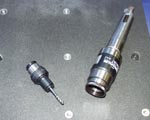 |
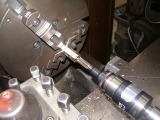 |
ここでは旋盤によるオートタッパーを用いたタップ穴加工について簡単に解説します。
- 旋盤の正転〜逆転機能を確認したら、オートタッパーを芯押台に取り付けます。
- 回転数をタップ加工できる回転(一般的に遅い回転)にします。
- 正転時タップのリードにあわせて芯押台のハンドルを回して押しコップを繰り出していきます。このとき、タップのリードとテーブルの同期が不十分でも取り付け位置から上下10mm程度は吸収しますが、手動の目測でよいのでできる限り同期をとるようにします。
- 止まり穴の場合、タップが穴の先端に到達するとタップを掴んでいるホルダーのクラッチが効きカチカチと音を立てます。このとき、あわてずに主軸の回転を一端停止します。
貫通穴の場合はタップの切刃が十分貫通したことを確認したところで主軸の回転を止めます。
- 次に、主軸を逆転し、芯押台のハンドルを回して押しコップをゆっくり戻します。
- そのままタップが加工物から抜ければ一工程終了です。貫通穴タップの場合はこれで完成です。
- 止まり穴タップの場合は3番タップに交換して、同じ手順で作業を進めます。
タップホルダーのメカニカルクラッチの精度がよく、タッパーの不良による折損はありません。
この方法は縦型ボール盤にも応用できるものです。
旋盤によるネジ切り加工
次に紹介するのはネジ加工です。
近代産業革命のマザーマシンとも言える旋盤の第一号はイギリスのモースレイが作ったものです。それまでの機械と異なる点の一つが、親ねじによる自動ねじ切り機構です。それまでにもレオナルド・ダ・ヴィンチらがねじ切り機を設計しており、王侯貴族の高貴な趣味として熟成していたローズエンジンにもねじ切り機構はありますが、産業用として大量にねじを作れるようになったのはモースレイの旋盤が初めてです。
モースレイの旋盤以後は必ずこのねじ切り機構が付いており、200年もの間基本的な形状や機能は変わらずにきました。
ここでは旋盤のネジ切り機構を用いた本格的な方法と、ダイスやタップを用いた簡便な方法を紹介します。
ここでは、この親ねじを使ったねじ切り加工を解説します。
- ピッチに合致した送りの選択
旋盤にはネジ切り機構が付属しています。メートルとインチの両方に対応していて、多くの場合、その切り替えは、主軸台カバーの中にある交換歯車を掛け替えることによって実現します。
ネジのピッチに合うように主軸台の各レバーやタンブラーギアを選択し、送り方向(右ネジ、左ネジに対応)や自動送りとねじ切りの切り替えレバーも正しく選択されていなければなりません。
ピッチは、メートルネジの場合、ネジ山(あるいは谷)の距離で表し、インチネジの場合は1インチにいくつ山(あるいは谷)があるかで表します。例えば、メートルの標準ネジならば、M6P1は外径6.0mmピッチ1.0mm、インチネジならばUNC1/4P20は外径1/4インチピッチ20山ということになります。
主軸台の各種切り替えレバー | ねじピッチ表 |
タンブラーギア | 主軸台内部のギアの掛け替え |
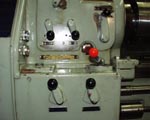 |
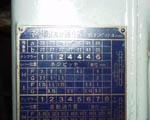 |
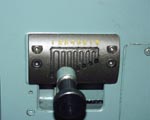 |
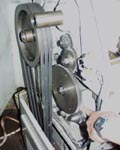 |
- ねじ切りバイトの取付
次に、ネジ切りバイトを刃物台に固定しますが、その時にセンターゲージを用います。センターゲージによってねじ切りバイトの刃先が正確にネジの形状に合っているかを確認するのです。この時、正確にバイト刃先の高さが合っていなければならないことは当然です。
センターゲージでバイトの傾きを調整する |
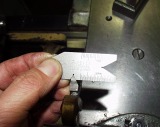 |
- ねじ切り作業の前に行わなければならないこと
ねじ切り加工に入る前に、ネジ部の面取り加工と切り上げ溝加工を行わなければなりません。面取りの大きさはピッチと同程度が目安です。
切り上げ溝はネジ加工部の終端を溝にすることによってねじ切りバイトの逃がし実現する方法で、初心者はこの溝幅を大きめに取っておくと良いでしょう。
逃げ溝加工を施したねじ加工部 |
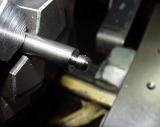 |
- ねじ切り作業には二つの方法がある
旋盤によるネジ加工に二通りの方法があります。
一つは、親ねじの落とし込みレバーを一度下ろしたらネジが仕上がるまで戻さない方法です。この方法はネジ部が比較的短い場合に便利です。最初に親ねじの落とし込みレバーを下ろし、ネジ加工を開始します。切り上げ溝までバイト刃先が達したら主軸を反転させると同時にバイトを引き、元の位置す。切り込みを与えて再び正転・・・以上を繰り返します。
もう一つは、往復台のダイヤルインジケータを利用した方法です。この方法はダイヤルインジケータの目盛を見て親ねじの落とし込みレバーを操作するもので、長い寸法のネジ加工に有効です。ネジ加工開始の位置に往復台を移動させ、切り込み量をセットし、ダイヤルインジケータが特定の目盛に来たときに親ねじの落とし込みレバーを下ろします。切り上げ溝に達したら親ねじの落とし込みレバーを戻し(これによってネジ切りの送りは止まる)てバイトを引き、手動で往復台を最初の位置に戻します。新しい切り込み量で、以上の動作を繰り返します。
往復台の落し込みレバー | インジケータと親ねじ |
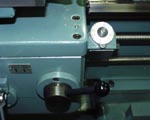 |
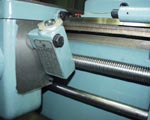 |
- ネジ切り加工時の切り込み量
ネジ加工は一気に行うことはできません。バイトの先端がデリケートなので、一気に行うと刃先の欠損や思わぬ事故を引き起こします。
従って、少しずつ、切り込みを重ね、目的の深さまで加工します。
P1.0のネジならば一回の切り込み量は0.1mm、これを4〜5回繰り返し、仕上げの切り込み量0.02mm程度として、現物やネジゲージによって噛み合いを確認します。
それでは、例題として、1/4インチ、P20のネジを旋盤で加工する手順を、順を追って説明しましょう。
- 旋盤のギアかけかえ
まず最初に、旋盤にねじ切り機構を確認し、ギア架け替え表を見て、必要なギアのかみ合わせになるように、主軸ボックス内のギアを架け替えます。
このとき、ギアの噛みあわせは僅かに隙間がある程度にします。
初心者はギアを遊びのないようにかみ合わせてしまいますが、それでは機械が壊れてしまいます。ギアは精度良く作ってあるとは言うものの、僅かな軸芯の誤差があるので、もし借りにピッチ円誤差の小さいほう同士で遊び無くかみ合わせれば、回転を与えたとき、ギアの歯や軸受けにとてつもない大きな力が加わり、双方を痛めてしまう可能性があるからです。
ギアのかみ合わせは、僅かに遊びを作っておく・・・というのが正しいということを覚えて置いてください。
ギアの架け替え表 | 変更前(メートル規格のセット) | ギアの架け替え後 |
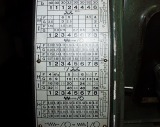 |
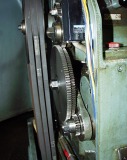 |
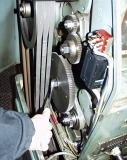 |
- ねじ切り加工の前加工
ねじ切り加工では、ねじの根本の部分で回転を止めるか反転させて、それ以上ねじ溝が進まないようにしなければなりません。いつも同じ場所でバイトの刃先を逃がすのを「切り上げ加工」といいますが、相当熟練しないと切り上げ溝が美しく仕上がりません。
ねじの根本は段を付けて軸に垂直な面を形成する場合が多く、この部分にバイト先端が逃げられる幅の溝を形成すると、相手側の部品に対し盗み溝として機能するので、強度的に問題なければ写真のような溝を付けておきます。これを逃げ溝と呼んでいます。
初心者は逃げ溝を大きめ(幅を広く)にしておくと、ねじ切り加工が楽になります。
逃げ溝加工を施したねじ加工部 |
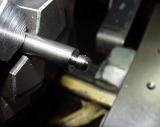 |
- レバー位置の選択
旋盤主軸台の送りレバーとタンブラーギアの位置を、ねじ切り表に従って選択します。ここで間違えるとピッチが大きく違ってしまいますので何度も確認します。
タンブラーギアの位置がずれていると、一見正しいネジが切れているように見えますが、僅かにピッチの違ったネジに待ってしまいます。これも良く確認しておきましょう。
タンブラーギアの位置 | 送りレバーの位置を確認 |
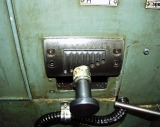 |
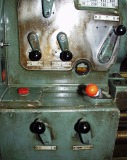 |
- バイトの取り付け
ねじ切り専用のバイトを取り付けるとき、センターゲージによって刃先角度や取り付け角度が適正かどうかを確認します。
センターゲージの背と旋盤のベッドのエッジを目で透かして見るのがコツです。
- バイト切り込み深さの設定・・・・切り込みゼロでカラー目盛りを”0”に
バイトが取り付いたら、バイトの先端を工作物のネジを切る円筒部にあわせ、ハンドルのカラー目盛りをわかりやすいところ(普通はゼロ)にします。
加工物の面にバイト先端を合わせる | ハンドルのカラー目盛りをゼロにする |
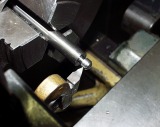 |
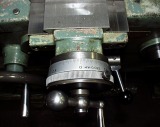 |
- ねじ切りの切り込み加工開始
カラーの目盛りをゼロに合わせたら、いよいよ、ねじ切りの送りになります。
サドルの右端にあるねじ切り送りのレバーを下げて「ねじ切り」の位置にします。このレバーは送りねじ(親ねじ)の割れナットを操作するもので、割れナットを開いたり閉じたりします。
ねじ切り送りのレバーを下げてねじ切り動作にする |
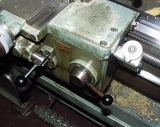 |
私たちが使っているねじ切りバイトはロー付けのヘールバイトなので、ピッチ2mm程度まで一回の切り込み深さは0.1mm程度にしています。これで目標に近づいたら切り込み量を減らして仕上げ面とし、あわせる相手方(雄ねじなら雌ねじを)が入るかどうか確認します。
最初に0.1mm切り込む(ハンドルの目盛り) | バイトの先端は0.1mmの切り込みで |
バイトの先端は0.1mmの切り込みで | 何回も繰り返し、目標の切り込み量に達する=完成 |
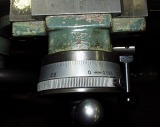 |
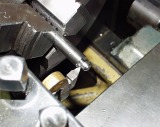 |
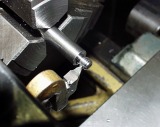 |
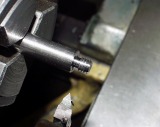 |
短いネジは落とし込みレバーを下げたまま、往復台を正転(ねじ切り加工)・逆転(元の位置に戻す)の繰り返しによって加工します。
内径のねじ切りも基本は同じですが、バイトの先端を直接見ることができないので、その分難しくなります。
- ギアを元に戻す
ナットか雌ねじがちゃんと入ることを確認したら、ねじ切り加工は終了です。
インチ送りのギアは必ずもとのメートル送りに直して置いてください。インチとメートルの切り替えは120/127のギア比で実現しています。
メートル規格のギア(120) | インチ規格のギア(127) |
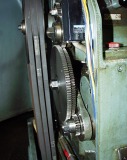 |
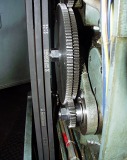 |
ローレット加工
ローレットとは、手で操作する部分の滑り止めのために、円柱部分にギザギザの切れ込みを入れたものです。文目と並目があり、それぞれ大きさも色々あります。
ローレット加工はこれまで紹介してきた「切削加工」とは異なり、ダイス(駒)を被削材に強く押し当てて塑性変形させるもので、非常に大きな力を加えることから、精密作業を得意とする「江黒旋盤」では行なわないで下さい。
ローレット工具はしっかり装着し、刃物台も強くロックします。回転数も200rpm以下で行って下さい。回転数が早いと極端に発熱し、作業がうまくいきません。
ローレット加工では直径が若干大きくなりますので、その分をあらかじめ小さく仕上げておきます。その値は中目(No.22程度)ならおおよそ0.5mmです。
ローレット前加工 | 仕上がったローレット |
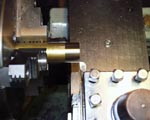 |
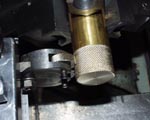 |
以下、ローレット作業を、順を追って説明します。
- ローレットの駒の幅約1/3程度の幅を被削材先端にあわせる。
- ローレットを強く被剤削材に押し当て、目が揃うまで横送りのハンドルを押す。
- 目が揃ったら、刃物送り台か往復台をゆっくり動かす。
- 必要な部分+ローレット駒幅までローレットがかかれば完成!
ローレット加工1 | ローレット加工2 |
ローレット加工3 | ローレット加工4 |
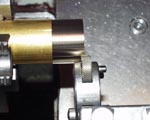 |
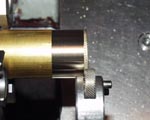 |
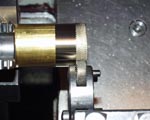 |
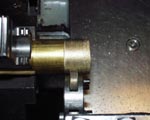 |
一端ローレットを被削材から離し、軽く押し当てて、左右に動かすことにより、切り屑を排除できます。この後、ワイヤーブラシなどで表面を軽くこすれば完成です。きれいなローレット目は手のなじみも良く、装飾的にもいいですね。
テーパ加工
テーパ加工も旋盤の重要な機能です。テーパとは円錐形状のことで、機械部品には多くのテーパ形状を利用します。例えば、旋盤の芯押し台にはモールステーパ、ドリルチャックの首にはジャコブステーパというように、位置決めと固定を同時に実現する便利な構造として多用しているのです。従って、旋盤によるテーパ加工は旋盤の基本的な機能の一つと言えましょう。
旋盤のテーパ加工には二つの方法があります。
一つは刃物送り台の下にある旋回機構(旋回刃物台)を用いるもの、そしてもう一つは両センタ加工で芯押し台のセンタをずらすことによって浅いテーパ加工を実現する方法です。
ここでは最初に述べた旋回刃物台を用いる方法について紹介します。
旋回刃物台による外径のテーパ加工 | 旋回刃物台による内径のテーパ加工 |
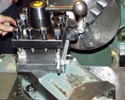 |
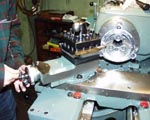 |
なお、テーパ加工で旋回刃物台を回転させた場合は旋盤加工の準備その1−刃物台の調整の要領で手送り刃物台が主軸と平行になるように、調整をしておいてください。こいの調整が不十分だと、あとで加工する人が合わせ直さなければなりません。
場合によっては、わずかなテーパに気づかず加工したために円筒部分の寸法精度が出ず、不良品となってしまうこともありますので、必ずきちんと直しておいてください。
Oリング溝の加工
真空容器や流体のシールにはOリングを良く使います。しかし、Oリング溝は傷のないきれいな仕上げ面が必要です。
旋盤によってOリング溝を加工する場合、ビビリなどの発生があってはいけません。溝の底面を横断するような傷は、シール性能を著しく損ないますので、回転数を落とし、ヘールバイトで加工するのがベストです。
Oリング溝の加工 |
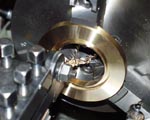 |
旋盤作業でノギスを上手に使うには
加工現場での測定、特に機械に工作物を取りつけたまま、工作物を測定することは、加工精度に直接反映します。機械加工の初心者が最も苦労するのは「測定」です。
ここでは、旋盤作業においてノギスによる測定作業を安全に行なうためのいくつかのポイントを整理しておきます。
安全の確保
測定中に主軸が回転するようなことは絶対にあってはなりません!
まず、安全確保のため、主電源を切るか、バックギアをニュートラルの位置にするなどして、誤操作等で電源が入ったとしても主軸が回転しないようにします。
旋盤作業では、主軸の法線位置は危険領域なのですが、回転を止めて工作物をノギス等で測定するとき、この危険領域に知らず知らずのうちに入り込んで、大きな事故を起こす可能性がありますので、常に機械の危険領域を意識していなければなりません。
以下に、代表的な測定方法を紹介します。機械と作業者との位置関係をよく見ておいてください。
- 外径の測り方
外径の測定 | 大きな外径の測定 |
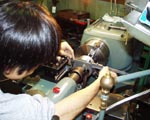 |
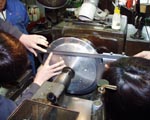 |
外形の測定では、芯押台のほうから主軸を覗き込むような位置に立ち、ノギスの主尺(メインスケール)副尺(バーニアスケール)に垂直な位置に測定者の目がくるようにすると視差による誤差を少なくすることができます。
次に、測定したい円筒面に対しノギスの主尺が主軸に直行するようにノギスの「くちばし」を当て、軽くスライダーを絞るように押します。このとき、不自然な姿勢となり、旋盤によりかかるような恰好となります。
初心者にとって、旋盤に工作物を取付けたままの測定は非常に難しいものなので、慣れるまで、何度も繰り返し、安定して測定できるように訓練してください。加工の途上で正確な測定ができなければ、工作物の精度は期待できません。如何に正確に測定できるかが工作の精度を決定するといっても過言ではないのです。
大きな径を測るときは、一人では困難なこともあるので、介助者をお願いしましょう。事故は複数名で作業する場合の方が圧倒的に多く発生します。互いの意思伝達がうまくいかなかったり、誤操作の可能性が増大するからです。必ず電源を切ってから行ないましょう。
- 内径の測り方
内径測定は外形測定よりさらに難しくなります。ノギスに付いている内径測定用の「くちばし」を穴に入れて、正確に最大径を取らなければなりません。外形の場合はノギスの傾きは目との関係で自由に取れたものが、内径測定ではノギスの傾きをゼロにしなければ最大径が求まらないからです。当然、視差がでないよう、目を副尺に垂直の位置にくるようにすると姿勢もさらに不安定なものとなりますので、旋盤の往復台のや刃物台を測定しやすい位置にあらかじめ移動しておくと良いでしょう。
- 段の長さの測り方
外径、内径の測定よりもずっと楽ですが、正確に測定しようとするとノギスでは不可能なこともあります。
ノギスのくちばしの裏にある段や反対側のデプスバーを使います。この部分の精度はメーカー保証がないので、あくまでも参照値ということですが、普段使うものはブロックゲージ等で校正するか、誤差を測定しておくと良いでしょう。
- 穴の深さ(溝の深さ)の測り方
段の測定と同じように、デプスバーを使いますが、デプスバーが入らないような小さな穴はノギスでは測定できません。
穴の中に切り屑が残っていたり、ドリルの先端角度などによって、測定誤差を生じますので、穴の内部をよく確認して、誤差の生じないようにします。
- 溝幅の測り方
内径測定用のくちばしを使います。内径測定よりも姿勢が自然なので測り易いと思います。
主軸チャックの保護
旋盤作業では思わぬことで事故を引き起こします。最近時々目にするのは、主軸チャックの爪と横送り刃物台をぶつける事故です。
幸い、作業者が怪我をするような事故になっていませんが、主軸チャックを破損したり、主軸そのものが狂うなど、工作機械に大きなダメージを与えるので、刃物台の位置が主軸チャックに近い場合には細心の注意が必要です。
一応、このような事故が起こらないよう、往復台の左側ストッパーを若干内側に配置して、外爪と横送り台が重ならないようにしておきますが、この部分を調整した人は、必ず元の位置にストッパーを戻しておいてください。
主軸と横送りが干渉する危険な位置 | ストッパーの位置を直す | 安全なストッパーの位置 | 主軸と横送りが干渉しない位置 |
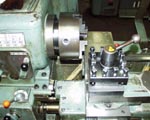 |
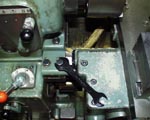 |
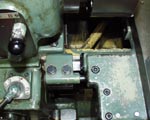 |
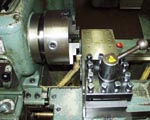 |
左から2番目の写真のように、ストッパーの固定ねじを緩め、ストッパーの位置を変更します。
この位置ならば、手送り刃物台を主軸側に出しすぎない限り、刃物台との干渉はありませんね。
刃物がチャックの爪に当たると、刃物が破損するだけでなく、チャックの爪も痛めてしまします。下の写真のようになっては、この爪は使えません。
必ずチャックや工作物と刃物の干渉がないことを確認したあとで、目的の作業に移る用にしてください。
破損したチャックの爪 |
|
|
- このページの先頭
- 汎用工作機械の使い方
チャック際の加工
チャック際の加工は、刃物・刃物台、横送り台と主軸チャックが互いに干渉しないよう、よく確認して下さい。
先に挙げたストッパーの位置が適正でも、比較的大きい径の材料をつかんだ場合はチャックの爪が飛び出しており、横送りハンドルや刃物台と衝突する恐れがあります。
従って、運転する前に主軸をフリーにして手でゆっくり主軸を回転させ、刃物を近づけたときに互いが干渉しないか、衝突の恐れがないかをよく確かめる必要があります。
僅かな時間を惜しんで、チェックを怠るととんでもない事故を起こすので、主軸チャックと刃物が接近している場合は特別の注意が必要です。
チャック際の加工には細心の注意を払う! |
|