旋盤用バイトの研磨
★ 更新記録:2012年09月19日、「目で見てわかる 切削バイトの選び方・使い方」を紹介します。
最近、私たちの周りからロウ付けタイプのバイトが急速に姿を消しつつあります。同時に完成バイト(高周波バイトともいう)を器用に成型して細い中ぐりバイトを作る職人もみかけなくなりました。
一品ものの試作を中心とした加工屋にとっては、大量生産の現場と違ってとにかく切れるバイトが一本作れればよく、バイト研磨は大変重要な技能の一つです。ところが、最近では刃先交換型(スローアウェイタイプ)バイト(旋盤で使う刃物を「バイト」と言います)に頼ることが多くなり、汎用旋盤でもスローアウェイバイトしか使えない人が増えています。
しかし、スローアウェイバイトだけでは、特殊な形状や特殊な材料が相手だったりあと5μm削って・・・などという要求には思うように加工できませんね。
その理由は、汎用旋盤は本来ハイス(高速度鋼のこと)製のバイトを使うように設計されており、より強い機械剛性を要求しているスローアウェイタイプのバイトは切削抵抗が大きく、刃物本来の性能を発揮することができないからです。
NC工作機械がどのように発達しても、市販のスローアウェイバイトで全て賄えるとは限らず、加工条件が変わるたびに誰かに適合するチップやフホルダーを聞く・・・というスタイルでは切削技術の向上は見込めないでしょう。こうした時、ロー付けタイプのバイト(ハイスと超硬合金両方あります)を、特別な設備なしに自由自在に整形して試験切削を行い、素早く刃先のデータを確定して、適合するチップを選べるようになりたいものです。
このような理由から、市販されてない形状や小さい径の加工に対応したり、未知の被削物における刃先形状と切削条件を探るようになるためには、ロ−付けタイプのバイトや完成バイトを自由自在に整形し、刃先を形成する技術・技能は、旋盤加工の専門家としては是非とも身に着けておきたいものなのです。
このHPでは、いささか古い技術ではありますが、ロー付けバイトを巧みに使う技術を若い世代に少しでも伝わればと思い、ロー付けバイトを両頭グラインダーで整形し、油砥石にて刃先を研磨する基礎的な工程とノウハウを公開します。
このページで紹介した「バイトの整形・研磨方法」は、「目で見てわかる 切削バイトの選び方・使い方」(2011年12月28日:日刊工業新聞社刊)に整理して詳しく紹介しています。
- 両頭グラインダー
- ハイス片刃バイト
- 超硬の片刃バイト
- 油砥石によるハイスバイトの刃付け
- バイト研磨−応用編(各種バイトの研磨)
このPAGEについてのご意見は koba*tech7.sci.nagoya-u.ac.jpまでお願いします。(スパム防止のために@を*で表現しいますので、この部分を書き換えてください)
両頭グラインダー
バイト研磨の前に、両頭グラインダーについて説明します。両頭グラインダーは文字通り、モーターの両側に砥石車を取り付けたものです。
第二装置開発室で使っているものは、直径305mm、幅30mmの砥石で、右側にWA-46-P、左側にGC-120-Hをつけています。砥石の名称の意味は、最初の記号は砥粒の種類で、WAはホワイトアランダム、GCはグリーン・カーボランダム(緑色炭化珪素、2008年12月11日に訂正、以前はコランダムと書いていましたが、完全な間違いでした。みなさまにお詫びします。)を意味します。次の数字は砥粒の粒度を示し、最後の記号はビトリファイド砥石の結合度を示しています。
ハイスの研削は主にWA砥石を使い、超硬の研削ではGCを使います。
一般的に、GC砥石は砥粒が細かいことや結合度がやわらかいので、ハイスの研削にも使います。その場合は強く当てないことがこつです。
砥石車は使えば表面が脱落して形が悪くなるので、時々ドレッシング(整形)をする必要があります。
GC砥石のドレッシングは左下の写真のように砥石整形用金剛砂砥石を押し当てます。
WA砥石は専用のドレッシングツールを使います。WA砥石は砥石表面の整形というよりは目詰まりを取り除く目的でドレッシングを行ないます。
GC砥石の整形 | WA砥石の整形 | 防塵マスクと安全めがね |
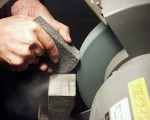 |
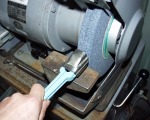 |
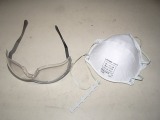 |
両頭グラインダーを使う場合は、労働安全衛生法に基づく特別教育「自由研削砥石」を受講する必要があります。粉塵被害を防止するため、防塵マスクの着用が義務付けられています。
両頭グラインダーの砥石と受け台の間隔が開いていると危険なため、適正な間隔に調整する必要があります。ドレッシングを行った後は必ず隙間を確認して、3mm以下に調整して置いてください。
受け台との間隔を測定 | 隙間を3mm以下に調整 |
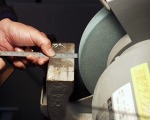 |
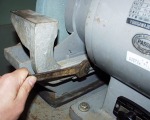 |
2、ハイス片刃バイト(真鍮用)
切削理論で整理したように、バイトの刃先角度は、逃げ角はどれも同じだがすくい角が被削材や刃物材によって異なります。
真鍮用の片刃バイトは最も単純な形状なので、砥石にバイトを当てる基本動作を練習するのに適しています。ここでは、バイト研磨の技能を磨くために、最も簡単な刃物の構造を持っている、片刃バイトの角度について整理します。
片刃バイトの刃先角の名称 |
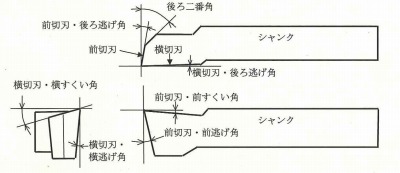 |
真鍮用片刃バイトの写真です。この角度をよく見ておいてください。
- 横切刃側面の研削
研削の順番は、大きい面から行います。刃バイトは横切刃を構成する側面の研削面が一番大きく、この面を綺麗に仕上げることができれば、基本的な技能を修得できたと考えてください。
側面は二つの角度を満足していなければなりません。横切刃横逃げ角は5〜10°、横切刃後ろ逃げ角は2〜5°を狙います。写真のように、一枚の連続的な研磨面を形成できるようにしてください。
ハイスバイトを研削するときは主にWAを使いますが、写真の例はGC砥石を使っています。
以下の写真のようにバイトを持ちます。両頭グラインダーは危険を伴うので、この写真のようにバイトを持つ指がグラインダーに触れないような姿勢と指の位置をよく考えることが大切です。グラインダーが止まっている時に、実際にバイトを持って研磨する部分を砥石車に軽くあてて見て、安全を確認してください。
砥石車にバイトの研削面を当てるときは、受け台に手(指)を置いて、手(指)が研磨の振動を吸収するようにします。
写真のように、止まっているグラインダーの砥石にバイトを当てて適正な角度になるときの置き台と手の関係を、砥石車を止めた状態でよく確認してください。
写真は実際に研削を行っているところです。グラインダーを止めている時と動いている時の砥石とバイトの位置関係が変化していないところを良く見てください。
連続的にあてていると過熱によって焼き戻しが入ってしまいますので、頻繁に水に入れて冷却します。研磨面に対しバイトを左右に動かすと砥石焼けを防ぐことが出来ます。
砥石を止めて角度を見る | 研削開始 |
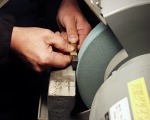 |
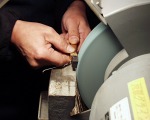 |
前の写真のような綺麗な研磨面を得るためには、砥石車のドレッシングも欠かせません。
- 横切刃上面の研削
横切刃の側面が研磨できたら、次に大きな上面を研磨します。
上面は、前切刃前すくい角(0〜5°)と、横切刃横すくい角(0〜10°)になるよう、砥石車を止めて当て方を確認します。
あとは横切刃側面の研磨と同様に、研磨面を仕上げていきます。
上面はハイスの焼きいれチップがロウ付けされているので、バイトを強く砥石車に押し当てるとすぐに過熱して焼き戻しが入ってしまいます。従って、あまり力を加えないように、頻繁に冷却することが大切です。
- 前切刃前面の研削
この面は、前切刃後ろ逃げ角(5〜10°)と前切刃前逃げ角(5〜10°)を狙います。
前切刃前面の研削ができたら、後ろ二番角を大きく取ります。これはセンター押し加工の場合にバイトがセンターと干渉しないようにするもので、必ず視の必要ではありません。
この面の研削は逃げ角が大きくなる傾向にありますので、角度をよくみて、大きくしすぎないように注意しましょう。特に、真鍮加工用のバイトは逃げ角が大きいとバイトが食い込んで大きく破損する事故につながるので注意します。
- ノーズ半径
ノーズ半径が大きい場合は、刃先先端を砥石車にわずかにあてて、0.3〜0.5程度の面取りをします。
最後なのでグラインダーのスイッチを切って、惰性で砥石が回転している間に、刃先をほんのちょっと当てる・・・というような操作をします。
ノーズ半径を小さくしたい場合は砥石車に当ててはいけません。
ハイス・剣バイトのノーズ半径 | スローアウェイ・チップのノーズ半径 |
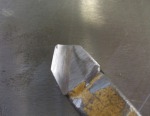 |
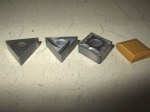 |
3、超硬の片刃バイト(アルミニウム加工用)
超硬バイトはGC砥石を使います。
GC砥石はWA砥石に比べて結合度を低くしてありますので、研磨面が急速に消耗するため、頻繁なドレッシング作業が必要です。ドレッシングには金剛砂の羊羹型砥石(#36〜46)を用います。
GC砥石を使う場合、研磨粉が大量に飛び散るので、防塵マスクと防護メガネは必需です。
以下に、アルミニウム加工用超硬片刃バイトの研削について解説します。
- 超硬合金ロー付けタイプアルミニウム加工用バイトの刃先形状
アルミニウム合金は柔らかいにも関わらず、切削で綺麗な表面を得ることが意外に難しい材料です。
アルミニウム合金の加工は刃物の先端に構成刃先を生成しやすく、それが加工面を悪くしたり寸法精度を損なう原因となります。構成刃先を防ぐには切削速度を高くすることと、切り屑の排出性をよくして切削抵抗を小さくすることが有効です。
そのために、刃物のすくい角を大きく取って、切り屑が走る面を大きめのR溝とし、綺麗に研磨しておくと良いでしょう。
以下に、アルミニウム加工用刃物(片刃バイト)の刃先形状を示します。
超硬合金ロー付けタイプ片刃バイト(アルミニウム合金加工用) |
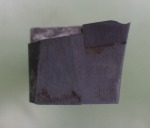 |
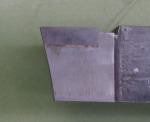 |
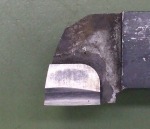 |
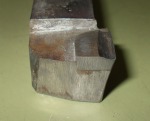 |
上の写真でお分かりのように、横切れ刃のすくい面にR溝が入っています。このRは任意ですが、写真のバイトはR2.5mmです。
市販のスローアウェイチップにもR溝が付いていますが、チップのR溝は鋼加工のときに切り屑が連続にならないよう折る応力を与えるもので、小さいRとなっています。従って、R溝があるからと言ってチップタイプでアルミ合金を荒削りしようとすると、大きな切削抵抗が発生し、うまく切れません。
- すくい面R溝の研削
砥石はGCを使います。WAでは砥粒の硬度が足らず、研削できません。
基本的には、ハイスの片刃バイトと一緒です。ノーズ半径の前に、横すくい面のR溝を付けます。
この溝が安定して付けられるようになれば、両頭グラインダーでの刃物の研磨(外径加工用編)は卒業となります。
写真19のように、砥石のエッジを使ってすくい面のR溝を研削します。
すくい面のR溝は砥石のエッジを使って研削する |
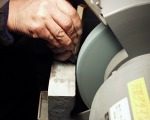 |
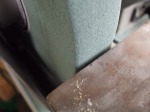 |
4、油砥石によるハイスバイトの刃付け
- 油砥石の種類
油砥石は3種類あります。
写真の白い(あるいは青い)羊羹形の砥石は仕上げ砥石、茶色の櫛型や棒状のものは中砥石、柄のついているものは超硬合金用のハンドラッパーです。
ハイスの場合は、両頭グラインダーで整形したあと、中砥石でグラインダーの研磨痕をとり、最後に仕上げ砥石で刃先を研磨します。
ハンドラッパーは超硬合金用です。柄の部分の色で砥粒の大きさが決まっています。赤は#250、黄色は#400です。
- 油砥石のメンテナンス
油砥石もハンドラッパーも、使えば研磨表面が消耗し、へこんでいきます。へこんだ状態では正しい刃付け研磨はできません。
使用前に、砥石の使用面が平面であることを確認してください。
もし平面になっていなければ修正する必要があります。#46〜#100程度のカーボランダムを挟んで共摺りすると凹みを修正できます。
油砥石もハンドラッパーも十分加工油が浸みていないと研磨熱によって刃先を鈍らせます。普段から加工油に浸しておくことをお勧めします。
切削油に浸した砥石 |
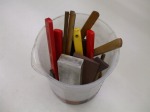 |
- 油砥石による刃付け研磨(平面)
両頭グラインダーの砥石車で整形した面は砥石車の直径と同じ円筒面になっているはずです。従って、その面に砥石を当てると、上と下に砥石が当たり、砥石の角度が決まるはずです。
砥石を上下に平行に動かすことによって実現します。この時、砥石の角度が上下するたびにふらつく(ローリング)と正しい角度になりません。
片刃バイトの横逃げ面は研削による平面が最も大きいので、砥石の角度がふらつきにくく、研磨技能の練習には丁度よい課題といえます。
もしこの方法が難しいようであれば、砥石を上下ではなく左右に動かして研磨してみてください。左右ならば角度がふらつく心配はありません。
中砥石による研磨 | 仕上げ砥石による研磨 |
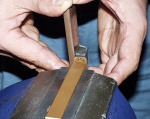 |
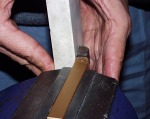 |
中砥石〜仕上げ砥石によって横切刃側面の研磨仕上げを行っている写真を見てください。砥石が変わっても砥石を当てる角度は一緒です。砥石を矢印のように上下に動かしたときも、この角度がずっと維持できるように訓練してください。
前面、上面と研磨を進めていきます。研磨砥石の角度を変えないことは全て同じです。
- ノーズ半径の付け方
ノーズ半径は、ノーズ半径を付けたいコーナーに「面取り」をする要領で砥石を当てます。小さく面取りが出来たら、ヤスリでRを付ける要領で砥石を回していきます。この時、逃げ角が損なわれないように注意してください。
- すくい面R溝の研磨
すくい面のR溝は刃付けという意味より、ここを滑る被削材(特にアルミニウム合金)との摩擦抵抗を少なくするために、滑らかになるようにします。
ハイスの場合は写真31のように丸あるいは小判型の砥石を使い、超硬バイトはハンドラッパーを使います。
すくい面のR溝 | 超硬の場合 |
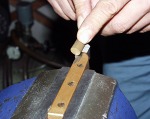 |
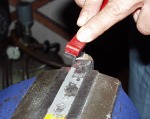 |
- 超硬バイトにはネガティブランドを付ける
超硬バイトは刃先が脆いために、ラッピングしても刃の先端に細かいクラックが入っています。これを取り除くため、#400〜#600のハンドラッパーで軽く面を取るように刃先をかるく磨きます。
ネガティブランドを設けることによって切れ味は一歩引きますが刃物寿命は大幅に伸びます。
ネガティブランド |
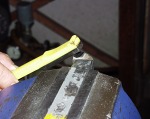 |
5、バイト研磨応用編(各種バイトの研磨)
基本的なバイトの研磨方法を説明してきましたが、ここからは応用編となります。
各種バイトの基本的な形状を示していくので、逃げ角とすくい角の関係を見て置いてください。
- 突っ切りバイト
意外に難しい突っ切り作業は、結局のところ、突っ切りバイトの性格を知っているかどうかに係っています。是非との自分で突っ切りバイトを製作し、使ってみて、何が大事なのかを体験してください。
突っ切りバイトの角度を下の図に示します。
突っ切りバイトで一番難しいのは、横逃げ角と共に僅かなバックテーパを付けるところです。横逃げ角やバックテーパを大きくしすぎると、バイトの根本が痩せてしまい、剛性不足になってしまいます。
バックテーパを上手につけるこつは、横逃げ角を取るときに、砥石車のエッジを使って研磨することです。この時、砥石車の軸に対して、突っ切りバイトのシャンク部分をマイナス側に3〜5°傾けることで、この角度がそのままバックテーパになります。
図5は突っ切りバイトの横逃げ角を研磨するときの、砥石車との位置関係を示したものです。
このように、最初から、逃げ角研磨の時にバックテーパを意識した位置取りをすることで、図4のようなバックテーパを形成することが出来ます。
左側の横逃げ角は左右反対になるだけで、同じことです。
研磨作業では、右手も左手も同じように使えないと、思ったような形にバイトを研磨することが出来ません。
このとき、砥石のエッジが多少丸くなっていたほうがバックペーパの研削面は綺麗に仕上がります。
- 中ぐりバイト
中ぐりバイトはシャンクから突き出した先に刃先があり、穴の内面を加工できるようになっています。従って、刃先は小さくなり、その形状は剛性との関係でとても微妙なものとなります。
中ぐりバイトは刃先の形状によって加工できる最小直径が決まります。写真のバイトでは前に突き出た刃先が通る穴径が加工できる最小直径となります。
この写真で分かるように、より小さい穴を加工する場合は、刃先をシャンクの中央まで下げればよいことがわかります。上の写真のバイトはろう付けタイプなので、十分に刃先を下げることが出来ません。
それに比べ、総ハイス製のバイトは刃先を下げることができるので、小さい径のバイトに向いています。
刃先を下げた総ハイス製の中ぐりバイト |
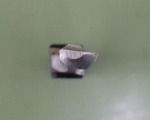 |
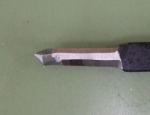 |
- 完成バイトから内径の細いバイトを作る
完成バイトは高周波バイトとも呼ばれているもので、高級ハイスの粉末を焼結し、熱処理後、表面を整形研磨したものです。
小径用の中ぐりバイト用には1/4〜3/8インチ角のもので、長さも60mm〜75mm程度のものが良いでしょう。
新品の完成バイト | 完成バイトから作った小径バイト |
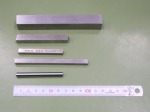 |
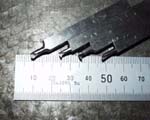 |
完成バイトは最も適した条件で焼入れされているので、グラインダーによる研磨作業のときに必要以上に加熱させないことが重要です。WA砥石よりも発熱の少ないGC砥石で荒取を行うと良いでしょう。
完成バイトはロー付けバイトのような大まかな形状すらない、単純な角棒になっているので、それを両頭グラインダーで削り落とし、バイトの形状を削り出さなければなりません。従って、これまでの研磨より多くの手間を要します。しかし、自由自在に整形できるので、上の写真にあるような非常に小さい径のバイトも製作可能です。
一般的に、両頭グラインダーの砥石巾は広いので、突き出しを短くしようとすると、突き出しの逃げを研削することができません。狭い小径の砥石が使える小型グラインダーがあるとこうした細かい作業が楽です。
- 突っ切り用のステッキバイト
突っ切りバイトは刃先の突き出し寸法が決まっているので、大きな径を突っ切ることが出来ません。こうしたときに重宝なのはステッキバイトです。
ステッキバイトは突き出し長さを自由にできるので、大きい径のバイトも、小さい径のバイトも自由自在です。
新品のステッキバイト | 刃先を整形したステッキバイト | ステッキバイトホルダー |
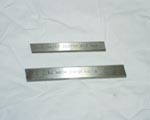 |
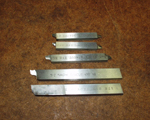 |
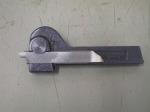 |
ステッキバイトは完成バイトと同じく、焼き入れ研磨されているので、必要以上に加熱しないことが大切です。バイトホルダーに少し長めに取り付けて両頭グラインダーで研削します。研削の要領は突っ切りバイトと同じで、僅かにバックテーパを取る所が重要です。
バックテーパはハイスの突っ切りバイトの項で解説したバックテーパのつけ方と同じなので、そちらを参考にしてください。
- Oリング溝加工用のバイト
Oリング溝加工用のバイトはステッキバイトで作ります。
下の写真のように、短い突っ切りバイトになっていますが、外周の逃げ角の取り方を写真のように工夫します。
フランジのOリング溝を加工するとき、逃げ面をまっすぐ落としたものは小さい径のOリング溝の場合、逃げ面の下の方が干渉してうまく削ることができません。逃げ角を大きく取れば一応加工はできますが、刃先角度が少なくなって、外形側の刃先が早く消耗し、加工精度が出にくくなります。
これを避けるには、外周の逃げ面をR形状にして、逃げ角を確保しながら干渉部分を逃げるようにします。エンドミルの横切れ刃のエキセントリック研磨に似ていますね。
このテクニックは小径の中くりバイトの逃げ角も同じです。
Oリング溝加工用のバイト |
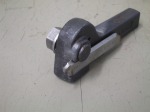 |
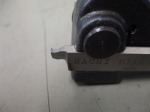 |