金工室にはマニュアル操作のフライス盤(写真−1 マキノフライス盤)が2台あり、小物の加工に適しています.
このフライス盤の基本的な機構は,コラム(本体)の前方に左右方向のX軸,前後方向のY軸,上下方向のZ軸という3軸のメカニカルテーブル,上部には旋回主軸ヘッドを備えています.
マキノフライスの特徴は,主軸スピンドルを150mm上下できるクイル機構が付いていることです.このクイル機構を用いて,高い位置精度での穴あけや中ぐり加工ができます.
金工室のマキノフライスは、X軸のフルストローク(650mm)で直線案内の誤差が1.5μmと極小です。これは各軸の直線案内機構をよく整備して得られた値ですが、同寸法のストレーとエッジと等しい驚くべき精度であるといえます。
マニュアル操作のメカニカルテーブル(XYZの3軸)にはデジタル・リニアスケールが取り付けてあり、テーブルの動きを直接数値で読み取ることができます。
クイル機構があるぶん、このフライス盤は全体の剛性が下がっているので、大きな刃物をつけてバリバリ加工する・・・というような使い方は不向きです。
|
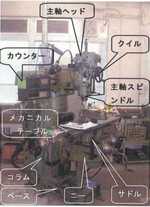 |