ボール盤による穴加工
更新記録、2009年1月13日、アクセス解析のため、カウンターを設置しました。
工作の中で、穴加工は最も頻度の高いもので、日曜大工で使うような電気ドリルでもけっこう簡単に穴加工を行うことが出来ます。
しかし、穴あけは簡単なように見えて、けっこう奥の深い工作です。
電気ドリルでは綺麗にあるいは正確に穴をあけられない場合でも、小型のボール盤があれば、位置精度も形状精度も良好な穴加工を行うことができます。
ここでは卓上ボール盤を用いた穴加工を紹介しましょう。
ボール盤による穴加工では、ストレートドリルを用いるのですが、この他にも用意しておくと便利な工具がたくさんあるのでここで紹介します。
最後に、薄板やアルミシャーシに穴を加工する場合の具体的なノウハウを紹介します。
関連するホームページへのリンク
このPAGEについてのご意見は kawai*tech7.sci.nagoya-u.ac.jpまでお願いします。(スパム防止のために@を*で表現しいますので、この部分を書き換えてください)
ボール盤の機構と機能
ボール盤とはドリルを使って穴加工を行う工作機械で、人類にとって最もなじみの深い工作機械の一つです。
ボール盤には、工作台の上に載せて使う卓上ボール盤、床に接地する直立ボール盤、ヘッド部分が水平に動くラジアルボール盤があります。特殊なものとしては、小径ドリル専用の高速ボール盤やタップ(雌ねじ)加工専用のタッピングマシン、大量の穴を一度に加工する多軸ヘッドボール盤などもあります。
卓上ボール盤は工作機械として、工場や工作室には必ず置いてあると思います。
ここでは、最も一般的な卓上ボール盤を例に挙げて、各部の名称と機能、ボール盤作業でよく使う工具を紹介します。
金工室で使っている卓上ボール盤と直立ボール盤の写真です。
ボール盤作業 | 卓上ボール盤 | 仕上げ室の卓上ボール盤 | 直立ボール盤 |
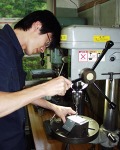 |
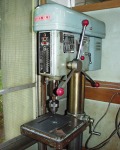 |
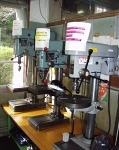 |
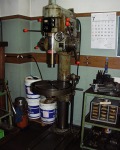 |
- ドリルチャックとスピンドル
ボール盤では、回転する軸の先端にドリルを取り付け、こてを回転させながら押し下げることによって穴加工します。このとき、上下する部分を「スピンドル」、「スピンドル」先端のドリルを掴む部分を「ドリルチャック」といいます。
「ドリルチャック」は「ジャコブステーパ」で「スピンドル」に打ち込まれており、スピンドル底部にあるナットを緩めることで「ドリルチャック」を取り外すことが出来ます。
一般的に、卓上ボール盤のドリルチャックは、直径13mmまでのストレートシャンクドリルを掴むことができます。
スピンドル | チャック&ハンドル | ドリルチャックの交換その1 | ドリルチャックの交換その2 |
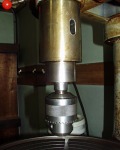 |
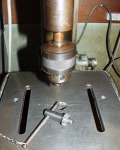 |
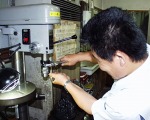 |
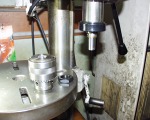 |
- テーブルの上下
ドリルの長さや工作物の大きさなどによって、テーブルの高さを調整する必要があります。
まず、固定ハンドルを緩め、上下動ハンドルによって丁度良い高さに合わせた後、固定ハンドルでテーブルを固定します。
このとき、固定ハンドルを閉め忘れると事故の原因となりますので、必ず締め付けて置いてください。
テーブル | テーブル固定ハンドル | テーブル上下動ハンドル | アシアボール盤は丸テーブル |
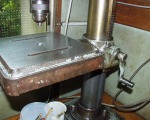 |
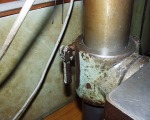 |
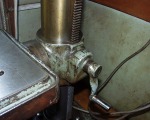 |
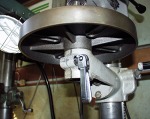 |
- 回転数を変える
ドリルの径によって回転数を変える必要があります。小さい径の場合は高速、径が大きくなるに従って回転数を遅くします。面取り加工や沈めフライスを使う作業では一番遅い回転数を選ぶと良いでしょう。
ヘッドカバーを開き、右(奥)の小さいレバーを左回しで緩め、赤いノブのあるレバーを押し込むとVベルトが緩みます。
Vベルトを目的の回転数となる段にあわせ、赤いノブのレバーを手前に引くとVベルトを張ることが出来ます。
この状態のまま、奥のレバーを右に締めこむと、Vベルトを張った状態で設定完了です。
回転速度の表はヘッドカバーの下のわかりやすい位置にあります。
ヘッドカバーを開ける | Vベルトを緩めるレバー | 回転数の表 | アシアボール盤はこちらで |
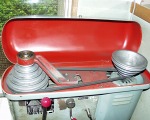 |
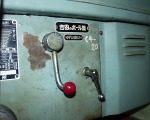 |
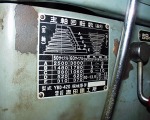 |
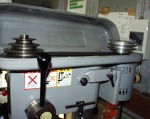 |
- 加工深さを見る
主軸ヘッドの前面に、スピンドルの上下動を見る目盛りが付いています。この目盛りは製造メーカーや機械の型番によって位置や方式が異なるので事前に確認しておきます。
下のねじを回すと目盛りを上下できるようになっていますので、丁度ドリルの先端が工作物に触れるで、加工深さと一致させておくと、穴の深さを合わせることが出来ます。
上下動ハンドルと目盛り | 目盛り板 | 目盛りの矢印を合わせる | アシアボール盤はこちらで |
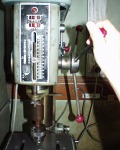 |
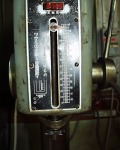 |
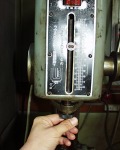 |
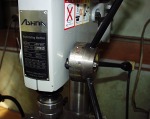 |
ドリルチャックにストレートドリルをしっかりつかみ、目印(センタポンチで刻印)の場所にドリルが真っ直ぐ降りる位置で工作物をバイスなどで固定し、上下動ハンドルでスピンドルを下げ、穴をあけます。
ストレートドリルと蝋燭ドリル
ここでは、ボール盤作業で用いる「ドリル」について説明します。
なお、ドリルの研磨については、こちらをご覧下さい。
金工室には、標準のストレートドリルを、直径1.0mm〜13.0mmまで、0.1mmピッチで用意しています。
一般的な穴加工では標準ドリルを用いますが、薄板やプラスチックの加工では蝋燭ドリルを使います。
薄板に標準ドリルをつかって穴をあけると真円度の悪い「おにぎり型」「五角形」に変形したあなになることが多いので、こうした場合に蝋燭ドリルが有効です。
標準ドリルの他に、ロングドリル(長さ150mm)、テーパシャンクドリル(直径14.0mm〜50mm)、ルーマ型ドリル(シャンク径1.0mm、直径0.05mm〜0.7mm)を用意しています。
このほかに、穴の仕上げ用として、ブローチリーマを用意しています。ボール盤のドリルで仕上げ寸法より0.2〜0.3mm小さい穴(下穴)をあけておき、そのままブローチリーマに交換して、高速回転で突き通すと、H7(汎用はめあい・すべりばめ)程度の精度のよい穴径とすることができます。
ストレートドリルとテーパシャンクドリル | ロングドリル | ルーマ型ドリル | ブローチリーマ |
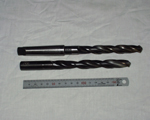 |
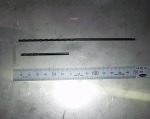 |
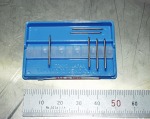 |
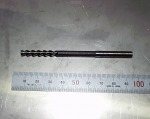 |
面取りカッターと座ぐりフライス
穴加工の後処理で重要なのは裏面のバリ取りです。面取りカッターで丁寧に取り除きましょう。
面取りカッターには、アルミ合金などの柔らかい材料用とステンレス鋼や構造用鋼などの硬い材料とで使い分けています。硬い材料の面取りを柔らかい材料用で行うと刃先がすぐに痛んでしまうので注意してください。
面取りの量を厳しくそろえる必要のない場合は、面取りカッターを専用のハンドルに取り付けて、穴にカッターを押し付けながらハンドルを手で回すと、バリが取れます。
大量にある場合は、電気ドリルに面取りカッターを取り付けて、これを穴に押し付けるようにして回せばバリを取り除くことができます。
面取りカッター | アルミ合金用面取りカッター | SUS用面取りカッター | 面取りカッターハンドル |
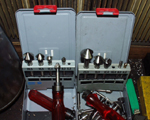 |
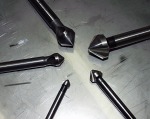 |
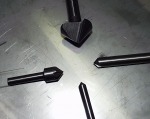 |
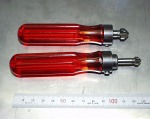 |
沈めフライスは、ねじ頭を掘り下げて隠す必要のある場合、例えば底面にねじを配置する場合に有効です。先にドリルで穴をあけておき、そのまま沈めフライスに交換して掘り下げます。このとき、回転数は一番遅くなるように変更して置いてください。
沈めフライスは中央のボスが案内となって周囲を削るようになっているので、ボール盤でも安全に加工できます。
M3より小さい径のねじに合致した沈めフライスは市販されていないので、古くなったドリルの刃を削って、沈めフライスとします。径が小さいので研磨しにくいのですが、一組作っておくと便利です。
沈めフライス | 自作沈めフライス | 皿小ねじ用沈めフライス |
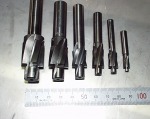 |
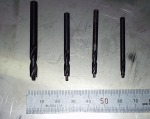 |
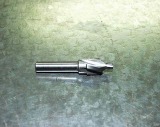 |
皿小ねじのザグリ加工は安易に面取りカッターを使うとザグリの中心がずれてしまいます。これを防ぐには、上右のような皿子ねじ専用の沈めフライスを用いると良いでしょう。
直立ボール盤
ここでは直立ボール盤の便利な機能と使い方を紹介します。
直立ボール盤の一番大きな特徴は、加工できる最大穴径が大きいことです。卓上ボール盤では直径13mmまででしたが、金工室にある直立ボール盤は直径50mmまでの穴加工、ボーリング加工を行っています。
13mmより大きい径では、旋盤の芯押し台のテーパと同じ、モールステーパとなっています。金工室の直立ボール盤は主軸端がMT4(モールステーパ4番)となっていますので、小さい径はソケットやスリーブを用います。
直立ボール盤 | 主軸部分 | スピンドルとチャック | 工具交換 | モールステーパ |
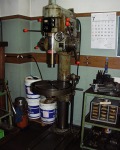 |
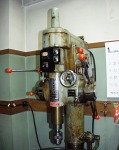 |
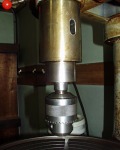 |
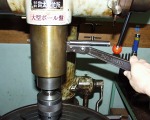 |
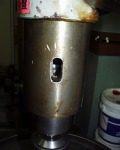 |
卓上ボール盤と異なり、本格的な穴加工が出来るように、直立ボール盤には次のような機能が備わっています。以下に、その代表的なものを紹介します。
- 回転数が細かく設定できる
速度変更用レバーによって、40〜1586rpmを12段で変えられるようになっています。これによって広い範囲の加工条件に合わせることができ、ボーリングヘッドによる精密穴あけ作業をも可能にしています。
回転速度変更レバー | 高速低速切り替えレバー | 回転速度表 |
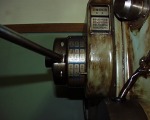 |
 |
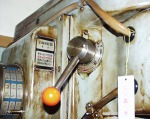 |
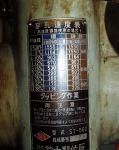 |
- 微動ハンドルによる大口径穴加工の送り
微動ハンドルは上下動レバーを外側に倒すことによって機能させることができます。
大口径の穴加工では切削抵抗が大きくなるとともに、レバーの操作では一様な送り速度を得にくいので、ウォームギアによる微動機構はたいへん有効です。
主軸端にボーリングツールを付ければ、穴径をミクロンの精度で加工することが出来ます。
微動ハンドル |
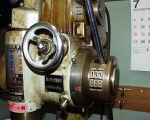 |
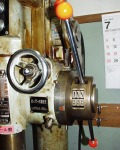 |
- スピンドルの自動上下機構と正転・逆転の切り替えによるタッピング(ねじ切り)
自動送りレバーでは、送り速度の選択と、タッピング動作の切り替えを行うことが出来ます。タッピング動作とは、送りレバーの操作で正転・逆転を瞬時に切り替えることが出来ます。タッピングツールなどを用いて、この機能を使えば、効率の良いタップ加工が可能です。
自動送りレバー | モード変更レバー |
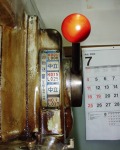 |
 |
直立ボール盤のテーブルにはT溝が付いているので、フライス盤と同じようにステップクランプを用いて工作物を強固に固定できます。金工室では直立ボール盤のすぐ隣にある牧野フライス盤用のステップクランプを使うようにしています。
テーブルの操作は卓上ボール盤と同様、上下動の固定クランプが左、右に上下動ハンドルとなっています。
さらに、このテーブルは、センターの穴を中心に旋回します。テーブルの裏に固定クランプハンドルが付いています。
テーブル | 上下送りハンドル | テーブル固定レバー | テーブル回転固定レバー | ステップクランプ |
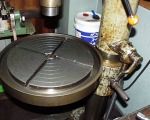 |
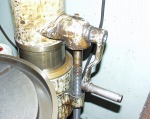 |
 |
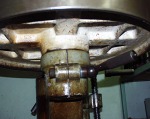 |
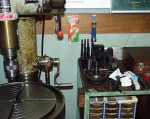 |
高速ボール盤
高速ボール盤は小さい径の穴加工に特化したボール盤です。主軸回転数約10000rpm、スピンドルを上下させるレバーが高感度となっていて、小径ドリルの切削抵抗がレバーの指先に伝わる仕組みになっています。
金工室の高速ボール盤による穴加工で、これまでに最も小さい径の成功例としては、直径0.07mm(ルーマ型ドリル使用)があります。
小型ドリルチャックの掴みは、ストレートドリルを用いた場合、直径0.5mmが最小となります。
テーブルの上下は、テーブル左下のノブを緩めて上下・旋回を行い、再びノブを締めて固定します。
タッピングマシン
タップ加工の数が多いときはタッピングマシンを用いると早く楽にできます。
このタッピングマシンを使うには、使用するタップに合わせて、ピッチの選択(換え歯車を使用)、ストロークの調整(リミットスイッチのドグ位置)、スリップクラッチの調整(摩擦式スリップクラッチ)を行う必要があり、この画業に手間取るのですが、一度調整すればその後はなにも考えずにタップ加工が出来ます。
このタッピングマシンは目的のピッチに合わせて主軸が下がるので、ロールタップを使えることも大きなメリットです。
タッピングマシン | 歯車を架け替えてピッチ選択 | スリップクラッチによるトルク調整 | ドグによるストローク調整 |
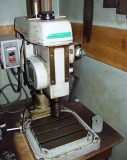 |
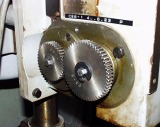 |
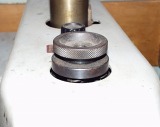 |
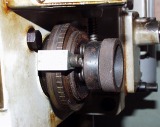 |
下の写真は150〜200箇所のタップ加工ですが、これを一つひとつ手で行っていたのでは相当の時間がかかります。タッピングマシンを調整するのに15〜20分ほどかかりますが、このように数がまとまればタッピングマシンの有り難さを実感できます。
多量のタップはタッピングマシンで |
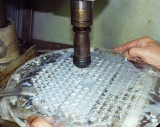 |
バイスとクランプ
ボール盤作業では、小さな工作物に穴あけ加工を行うことが多いので、こうした場合は小型のバイスやクランプを用います。
ここで紹介する小型バイスは、こうした目的のために普段使っているものです。変り種としては、古くなった旋盤のスクロールチャックを用いると、丸いものを掴むのに便利です。
ベタバイス | ヤンキーバイス | スクロールチャック | フリークランプ | フリークランプで固定する |
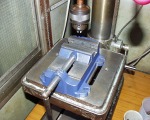 |
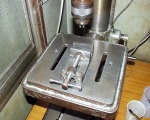 |
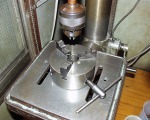 |
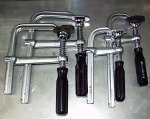 |
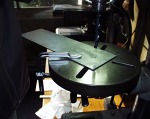 |
クランプはボール盤のテーブルに直接自由な位置で工作物やバイスを固定できるのでたいへん便利です。
実例−1−ボール盤による穴加工の手順(比較的厚い板の穴あけを例にして)
ボール盤作業で最も一般的な、比較的厚い金属板にボルト穴(段付き)を開ける手順を解説します。
ここで示した手順は、工作物が異なる場合、穴の位置のケガキの方法と、工作物を固定する方法に違いがありますが、全体の流れは一緒ですので、参考にして下さい。
厚さ15mmのアルミニウム板(A5052S)にM8用の通り穴とボルト頭部を沈めるために深さ9mmのザグリ加工を行います。
- 穴の位置を割り出す(ケガキ作業)
定盤の上で、ハイトゲージ、イケールなどを用いて、板(フライス盤で精密に外形を仕上げたもの)の表面に穴位置をケガキます。
ハイトゲージで刃先を合わせる | 平行にケガキ線を入れる |
|
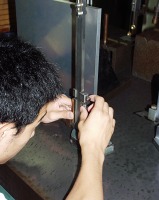 |
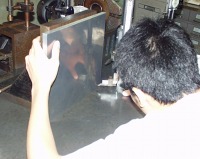 |
- センタポンチを打つ
ケガキ線の交点にセンターポンチを打ちます。
センターポンチの先端が尖っていないと、正確にケガキ線の交点に打つことができません。ポンチの先端を人差し指で軽く撫でてみて、痛点の神経を刺激しない場合(痛いと感じない)はセンターポンチの先端が鈍っているので、研ぎ直す必要があります。
センターポンチの練習 | センターポンチの本番 |
|
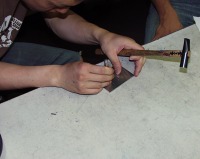 |
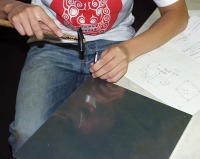 |
もしセンターポンチの位置がケガキ線から外れた場合は、ヘガキ線からずれた反対側のポンチ痕の縁にセンタポンチの先端を合わせ、軽く打って、中心位置を正しい側に引き寄せます。うまくいかない場合はポンチを傾けるなどして、ケガキ線の中央に引き寄せます。概ね修正できたら改めて強く打ち直します。この作業は拡大鏡などを使うとわかりやすいと思います。
- ドリル先端をポンチ痕に合わせる(芯出し作業)
目的の直径(φ8.5を使用)のドリルをボール盤のチャックでしっかり銜え、テーブルの高さを調整して加工物をテーブルに載せます。このとき、テーブルをしっかり固定します。
ドリルの先端とポンチ痕がおおよそ一致する場所で上下送りハンドルを回し、ドリル先端とポンチ痕が軽く当たる状態にします。
送りハンドルを軽く押しながら手で軽くスピンドルを反転させると、ドリルの先端が自動的にポンチの中心を捕らえます。この時、加工物が僅かに動きます。これにて芯出しができました。
センターポンチの位置にドリルを合わせる | スピンドルを手で逆転させる | クランプで板をテーブルに固定する |
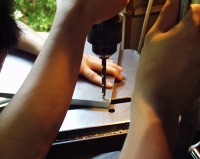 |
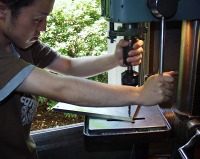 |
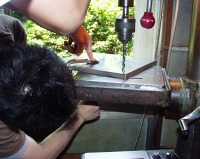 |
- ボール盤のテーブルに固定する
芯がずれないように、クランプでテーブルと加工物を固定します。一度ドリルを回転させ、軽く加工物に当てて、センターが狂っていないかを確認します。もしずれてしまった場合は、もう一度芯出しを行います。
- 穴を開ける
ドリルの先端に加工油を少し付け、回転を与えて、穴加工を行います。穴の抜け際にさしかかったら、上下ハンドルをしっかり握り、引き込まれないようにします。
- 面取り加工を行う
ドリルによる穴加工では、必ず裏側にかえり(バリ)が出るので、固定していたクランプを緩め、表側裏側ともバリ取りを行います。写真では手で面取りカッターを回していますが、アルミニウムのように柔らかい材料ならこれで十分です。
ステンレス鋼などの硬い材料の場合はボール盤や電気ドリル(低速回転のできるもの)に面取りカッターを取り付けてバリ取りを行います。
手で面取りカッターを回す |
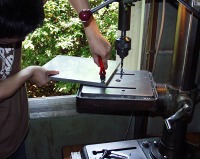 |
- ザグリフライスの高さを合わせる
ボルトの頭部を沈める加工は専用の工具である沈めフライスを使います。M3〜各種サイズが揃っています。
沈めフライスがネジの通り穴を開けた後にボール盤で安全に加工できるよう、中心にガイドが付いていますので、ガイド部分を先に空けた穴に合わせ、板(加工物)を固定します。
沈めフライスを取り付ける | 沈めフライスの中心を確認する |
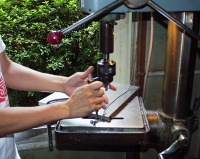 |
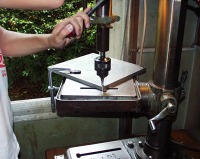 |
- 段穴加工を行う
沈めフライスの加工深さはスピンドルの全面にある目盛板で見ます。ストッパー機能を使って一番下までスピンドルを降ろしたら穴の深さが合うように設定することもできます。
沈めフライスは加工径が大きいので周速度(切削速度)が高くなりがちです。こまめに給油して、無理のない加工を心がけて下さい。
目盛板を見ながら深さを合わせる | 時々刃物をあげて給油する |
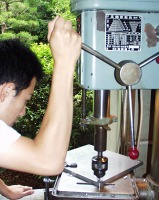 |
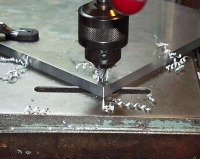 |
- ザグリ部分の面取り加工を行う
ザグリ部分の面取りも行います。この場合、大きい径の面取りカッターを使うことになりますので、ボール盤を使う場合は回転数を落とせるものでないとうまく加工できません。充電式の電気ドリルか手回しが安全です。
- 穴加工時の切削油
深穴加工では加工油が必需です。穴の直径(分母)と深さ(分子)の比をアスペクト比といい、5を越える加工は難しく、10を越える加工は極めて難しいと考えて下さい。
- 穴加工で失敗しないために
アルミニウムは柔らかいので、一見、穴加工がしやすいのではないかと考えがちですが、小径のアスペクト比が大きい加工では切り屑が詰まってドリルを折る事故が多発します。
ステンレス鋼に穴を開ける場合、ギリギリと音が発生したらドリル刃先がダメになっています。この状態で無理に加工すると、ドリルが折れたり、加工硬化によって次の加工(例えばタップ加工など)が困難になってしまします。このような時は、ドリルを再研磨するか、新しいドリルに取り替えましょう。
薄板やプラスチック板の場合はろうそくドリルを使い、下にダミーの板きれ(ベニア板など)を敷くとうまく行きます。
実例−2−アングルなどの長物の穴加工
アングルなどの長い物に穴加工する場合、ベタバイスなど大きめのバイスで工作物を固定します。
それでも工作物がながくて安定に固定できない場合は、隣のボール盤のテーブルを支えに使うと良いでしょう。
複数のボール盤を隣り合わせに配置しているのは、このような場合を想定してのことです。窓側にはみ出す場合も、窓を開ければ相当長い物でも加工できます。
隣のボール盤テーブルを支えに使う | 窓をあければ長い物も大きい物も固定できる |
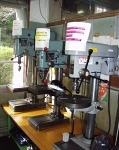 |
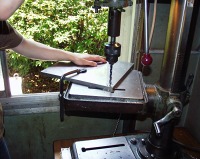 |
実例−3−長物端面の穴加工
長物の端面に穴加工するばあい、工作物の固定方法に一工夫します。
ボール盤のテーブルを下まで下げてベタバイスで工作物を固定することで加工できれば比較的簡単ですが、もった長い場合はテーブルにイケール(アングルプレート)を取付、イケールに工作物を固定するほうほうで行います。
卓上ボール盤のベースから主軸までの距離は短いので、これより長い場合は直立ボール盤を使うことになります。
さらに長い場合は、縦型ボール盤では加工できません。そのような場合は、手持ちの電気ドリルを使うことになりますが、穴の位置精度は格段に悪くなります。
実例−4−皿ねじ用ザグリ加工
サラネジの頭を綺麗に工作物に沈める(出っ張らないようにする)加工は、穴の中心と円錐のザグリ穴の中心が合わないことが多いので注意が必要です。
下穴加工(ボルト穴)をおこなったところに面取りカッターなどでそのまま加工すると、中心がずれる可能性が非常に高いので、写真に示すようなサラ穴専用の工具を使います。この工具ならば最初に空けた穴中心がずれることはありません。
センターガイドの付いたサラ穴用カッター | 加工の様子 | サラネジを入れたところ |
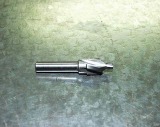 |
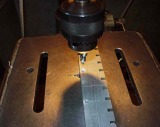 |
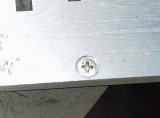 |
return to top !
実例−5−薄板、プラスチック板の穴加工
薄板(1mm以下)に普通のドリルで穴を開けると、おにぎりのように少し潰れた穴形状になったり、急にドリルが食い込んで危険なめにあうことがあります。
プラスチック板(アクリルなど)の穴加工では、ドリルが抜けかかる頃に急に負荷が軽くなって食い込み、エッジが割れてしまうことがあります。
おにぎり型に崩れた穴 | エッジが割れたアクリルの穴 |
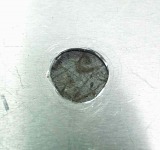 |
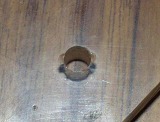 |
このような場合、蝋燭ドリルを使います。蝋燭ドリルとは、先端が蝋燭のような形状になっているもので、中心と円周部分がにサラネジの頭を綺麗に工作物に沈める(出っ張らないようにする)加工は、穴の中心と円錐のザグリ穴の中心が合わないことが多いので注意が必要です。
下穴加工(ボルト穴)をおこなったところに面取りカッターなどでそのまま加工すると、中心がずれる可能性が非常に高いので、写真に示すようなサラ穴専用の工具を使います。この工具ならば最初に空けた穴中心がずれることはありません。
蝋燭ドリルの形状 | 蝋燭ドリルで空けた穴 |
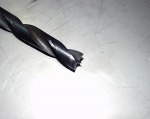 |
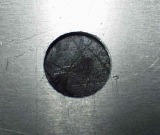 |
縦型ボール盤によるタップ加工
縦型ボール盤には卓上ボール盤にはない便利な機能があります。
ここで紹介するタップ機能はスピンドルを上下させるレバーの操作(少し外側に開く)によって主軸が反転するもので、小ねじならばタッパーと組み合わせて、大きいねじならばそのままチャックにタップを固定して、タップ加工を実現できます。
写真で紹介するのはM20P1.0とのねじ加工で、太いのでドリルチャックにタップをそのまま固定しています。
縦型ボール盤のタップ機能を使ったタップ加工 |
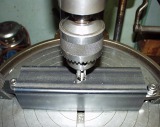 |
ボーリングツールによる加工
ボーリングツールは10μm単位で直径を微調整できるスライド機構を持った工具で、ボール盤やフライス盤にボーリングバイトを取り付けて任意の直径の穴の内径を精密に加工できます。
縦型ボール盤はフライス盤よりも主軸の上下が大きいので、写真にあるような懐の高さを必要とする加工も可能です。
ボーリングバイトとボーリングツールを使った穴加工 |
ボーリングツールを使った精密穴加工 |
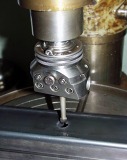 |
 |
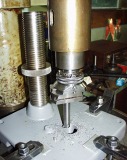 |