光学マスクの加工
ここで紹介する光学マスクは「ASTRO−F」の光学系を評価するためのもので、厚さ0.1mmのリン青銅板に、小さな穴を正確な位置にあけたものです。
光学系の実験装置では、光路を正確に辿ることによってその光学系の工学系の誤差を正確に測定することは重要である。そのためには、マトリックス状にピンホールを配した光学マスクを用います。
光路解析用光学マスクは、穴の直径精度、真円度、位置精度が要求されます。場合によっては、機械工作限界の小さな穴径を要求されることもあります。
穴加工の限界2>
金工室の小径穴加工の限界は、直径0.05mm、深さ0.2mm、加工材料「りん青銅板」です。
このような穴加工の場合、加工可能な深さの制限も厳しい。穴径に対する穴深さの比をアスペクト比と呼び、これが〜5程度なら普通に加工可能であるが、10を超えるような場合は加工が困難となります。
光学マスクの場合、穴のエッジにバリなどを残さないために、上下をダミーの板で挟んで加工するので、実際に加工する穴が深くなり、アスペクト比が大きくなることから、穴径が小さいほど非常に難しい作業となります。
一般的に、小径ドリルによる穴加工は高速回転が必要とされています。それは被削材と刃物による最適切削速度の範囲があり、小径では回転数を上げないと理論的に良好な切削速度に達しないからです。
写真は高速ボール盤にドリルを取り付けたときの偏芯を測定し、最小となるようにしているところです。高速ボール盤はレバー式のスピンドル上下機構を備えており、ドリル刃先の状態がレバーを介して指先に伝わるため、扱いやすい構造となっています。しかし、主軸スピンドルを約1万rpmで回転させると、ダイナミックバランスが取れていない分だけ振動し、穴径を大きくするように働きます。実際に高速ボール盤で0.05mmのドリルを使った穴加工では、直径0.060〜0.065mmとなり、オーバーサイズとなってしまいました。
下の写真のように、位置決め精度の良いマキノフライ盤を用い、振動の少ない回転数1500rpm程度で加工した方が良い加工面を得ることができます。反面、高速ボール盤のような操作性は得られず、もっぱらZ軸(テーブルの上下移動)のカウンターを頼りの加工となります。
この様に、微細加工では、理論値から大幅に外れた切削速度でも、振動による悪影響を取り除いた方が良い結果を得られることは良く経験することです。
高速ボール盤による加工 | ドリルの芯出し |
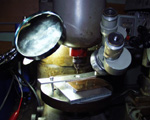 |
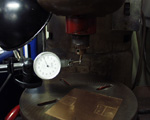 |
穴の位置精度
光学マスクの場合、穴の位置が正確に分かればよいので、とにかく穴を加工してから、穴の位置を正確に測定することができれば、穴の位置はおおよそでよく、レバー式のスピンドル上下機構扱いやすい高速ボール盤を使うことができます。
金工室の工具顕微鏡の測定範囲を超えたものや位置精度を要求される場合はフライス盤の位置決めを用いなければなりません。
この場合、マキノフライスの座標再現性(X−Y座標)は±10μm以内であり、光学マスクのような狭い範囲の位置決め精度は2〜3μm程度を実現できます。写真では、切り屑の排出を顕微鏡で確認できるようにしています。マキノフライスは完全マニュアル操作で高い位置決め精度を実現できることから、限界に迫る小径ドリル加工が可能であったと考えられます。
リニアスケールを装備した汎用フライス盤(NC制御装置を備えたフライス盤も含め)の座標再現精度(X−Y座標)は±20μm程度を実現していますが、0.05mmのドリル加工は不可能です。サーボロック状態でも常時±20μmの揺らぎがあり、ドリルの刃が折れてしまいます。これらのフライス盤では0.2mmが限界と思われます。
マキノフライス盤による加工 | 完成した光学マスク |
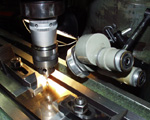 |
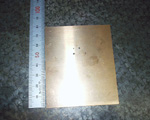 |