OPERA実験用メカニカルステージの開発
最新の更新 2009年1月14日、今後、この技術業務をまとめるため、順次技術内容を公開していきます。 by Kawai
近況報告
OPERA実験の原子核乾板解析用顕微鏡高速ステージは4号機まで製作し、研究室(解析室)が耐震補強工事によって移転しなければならない事態(2008年)にも遭遇しながらも、OPERA実験は順調に進み、何とか解析できる水準の顕微鏡高速ステージを何台か完成させることができました。
機械としては、極めて微弱な振動を止めることや、顕微鏡ステージは原子核乾板の解析作業に入ればほぼ連続運転となり、様々な部品の寿命限界に近い厳しい物です。
すでに1号機でトラブルが発生し、X軸の送りネジ(ボールネジ)が完全に破損しました。X軸の交換は機械の保守としては最も容易なため、機械を止める時間も半日程度で収まりました。
4台の高速ステージで、X軸が最も負荷が大きいため、今後同じようなトラブルが発生する可能性もあります。
主にOPREA実験で出る大量の原子核乾板を高速解析するための顕微鏡テージの概要と開発状況を報告します。
現状報告(2007年2月14日)
現在、基本的な開発要素は概ね終了し、コスト低減を考慮して設計見直しを行った「量産型ステージ」1号機の総合組立を行いつつあります。この顕微鏡ステージはS-UTSを搭載(100倍の対物レンズを使用して高速CCDによる画像取り込みと解析を同時に実行)した状態で視野の座標精度0.2μm以内を目指しています。
第一号機に新たに追加された要求は、移動範囲の拡大と、XY直交座標系の精度です。これはこれまでの仮組立における精度確認で、全移動範囲において、エラー2μm以内を達成できる見込みとなりました。
そこで、新しい情報として、「量産型NewStageの組立」として順次掲載していきます。
これまでの掲載事項
関連サイト
このページについてのご意見はkawai@ufp.phys.nagoya-u.ac.jpまで
量産型NewStageの組立
2009年1月15日 加筆 by Kawai
以下に、量産型顕微鏡高速ステージの組立作業を紹介します。1号機で試行錯誤したことを量産型に反映し、2号機でさらなるかいりょうを加えました。その後3〜4号機は順調に組みあがり、精度や運動性能は概ね要求を満たすことができました。
- ベース部分の加工と組み立て
定盤のほぼ中央付近に照明光学系を取り付ける直径40mmの穴を開けます。これは大型のアトラという電磁石式ボール盤とジェットブローチ(筒状の穴あけ専用工具)を使いました。周囲の小さい穴は同じくアトラエースを使いました。
このような方法は、穴の位置精度が不十分になりやすいので、設計である程度調整できる余裕をもたせることが必要です。大きな工作機械の持っていない我々にとってアトラのような工作機械は大変便利です。ただし、工作物が鉄であることが条件ですが・・・・
アトラとジェットブローチによる穴加工 |
アトラエースによる穴加工 |
穴加工の終了した定盤 |
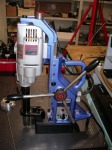 |
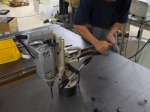 |
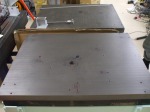 |
- 照明光学系の取り付けとベースの水平だし
定盤にあけた穴の面を丁寧に取って、掃除機で切り屑を吸い取った後、照明光学系を組み付けます。照明光学系はXYZそれぞれに自由度を持たせる設計になっています。X〜Yは±1mm、Zは±10mmの調整範囲としました。
これらの調整は、後でX−Yステージと主光軸台、Zステージ、S−UTSを取り付けた状態で、微調整する必要があるので、小型のユニバーサルジョイントで微調整用のネジを回せるようにしました。
ベースの水平だし |
照明光学系のマウント |
照明光学系を取り付けて動作確認 |
完成したベース |
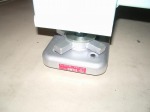 |
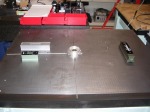 |
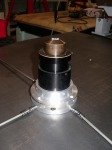 |
 |
- X−Yステージの組み立て調整
この顕微鏡ステージで最も難しいのがX−Yステージの組み立て調整です。
最初にY軸のベース板を乗せて、その上にリニアガイドとボールネジを仮固定します。長手側のリニアガイドがY軸ベースの基準エッジに並行になるように両端を仮固定、ガイドブロックにダイヤルゲージを取り付けてストレートエッジで直線走り精度を確認しながら固定ネジを締め付けていきます。
長尺側リニアガイドとボールネジの間隔の誤差を0.1mmになるように固定、短尺側リニアガイドのレールは仮止めのネジを緩めておきます。
この状態でX−Y中間板を載せ、Y軸リニアガイドのブロックとX−Y板の取り付け穴全部にネジを挿入します。このとき、ボールネジの固定部分の隙間がないこともあわせて確認します。この部分は見にくいので、歯医者が使うような小型の鏡と懐中電灯があると便利です。
長尺側のリニアガイドブロックとX−Y板を仮固定し、前後に軽く動くことを確認後、短尺側のレールを固定し、Y軸の直線案内機構を確定します。この状態で直線走り精度を確認し、±2μm以内であればOKです。
ここで一旦X−Y板を取り外し、エンコーダを取り付けます。エンコーダの取り付け精度はメーカーのカタログに従ってください。
Y軸のボールネジ駆動固定のネジを締めて、モータでY軸を動かし、問題が無ければY軸の基本部分は完成です。
X軸の組立を行います。基本はY軸と同じですが、XとYの直角精度を確保するため、X軸の超尺リニアガイドは直角基準を使ってY軸とX軸は稼動範囲内でそれぞれ誤差±5μm以内になるように取り付けます。X−Yステージの組立でこの部分が最も難しいところです。
直角精度が確認できれば、Y軸と同じようにX軸も組み立てていきます。X軸の一番上の板は、本来ならガラス板が貼り付けてる物なのですが、組立作業はガラス板のないダミープレートを使います。
Y軸リニアガイドを仮固定 |
Y軸エンコーダ取り付け |
X-Y板は重いのでホイストを使用 |
X軸の直線性を見る |
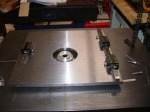 |
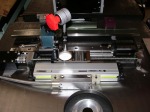 |
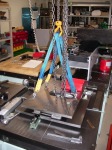 |
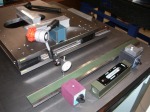 |
X軸リニアガイドなどを仮固定 |
直角基準でX−Yの誤差を見る |
ダミーのトッププレートを乗せる |
設計変更で追加加工もアトラが活躍 |
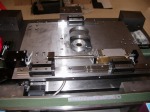 |
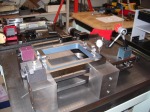 |
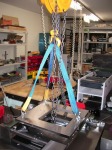 |
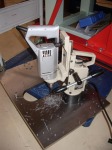 |
- Z軸ラフステージの組み立て
Z軸ステージはS−UTSの高速振動に耐えて顕微鏡の光軸を確保し、振動等による画像の劣化も許されない高い合成を要求されています。従って、このZステージは稼動範囲が僅か30mmにも関わらず、工作機械並みの剛性を持たせた構造となっています。
X−Yステージが中抜き構造に対し、Zステージは駆動軸から外れた位置に主光軸があり、その点で振動や誤差のない機構であることが求められています。
Zステージは2枚の精度のよい板の間に直線案内のリニアガイド2本を平行に置き、中央に駆動用のボールネジを配した標準的なものですが、X−Yステージとは異なり、4点支持の構造なので、過拘束にならないような精度(平面精度)が上下の板に必要です。
リニアガイドを固定する |
ボールネジを取り付ける |
手動で直線案内の負荷の変化がないかを確認する |
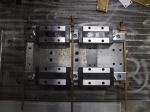 |
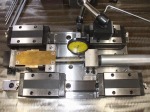 |
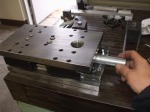 |
- Zステージを取り付ける構造体の組み立て
剛性の大きいZステージを取り付ける構造体も充分な強度と制震作用が必要です。
基本的な考えは振動エネルギーを重さの比で小さくし、適度に制震構造を入れることによって光学顕微鏡としては最も拡大率の大きい顕微鏡視野でも揺れを感じさせない程度にすることを目標にしました。
大まかな構造は、300mm角のH型鋼(重量100Kg)に剛性の大きなラフステージを介してS-UTSをがっちり固定すると言うものです。H鋼の両端はブリッジ構造で定盤の四隅に固定します。四隅の足には高さを調整するネジ式ジャッキを作りこみ、ダブルナットで固定します。
H鋼のブリッジもL金具を介してしっかりねじで固定します。
H鋼はそのままでは共鳴するので、上部に四箇所振動吸収用のツッパリパイプを固定し、さらにその中に振動吸収材を入れられる構造にしてあります。
ブリッジの水平だし |
作りこんだネジ式ジャッキ |
両側の高さをそろえる |
H鋼部分を載せる |
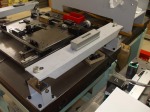 |
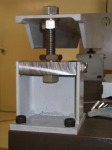 |
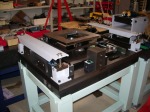 |
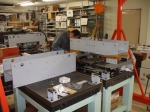 |
- Z軸ラフステージ搭載と光軸あわせ
H鋼のZ軸を支える構造物が載ると、Z軸ラフステージを取り付け、S−UTSを取り付けて、光軸合わせを行います。ブリッジとH鋼の取り付け位置はアジャスタブルなので、S−UTSのカメラを取り付ける穴から覗き込んで、照明光学系の中心に穴の中心をインチングであわせます。
水準器で水平を確認後、ブリッジのジャッキ、H鋼とのつなぎなどのネジをしっかり締めこみます。
Z軸ステージを取り付ける |
インチングで位置合わせ |
H鋼とZ軸ステージの仮合わせ |
S-UTSを取り付ける |
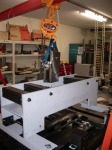 |
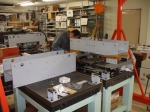 |
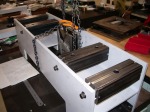 |
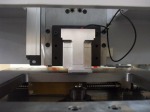 |
- リミットスイッチなどの調整
機械屋の仕事はもう一息。
リミットスイッチやエンコーダを取り付けて、可動範囲が最も有効に使えるよう微調整をします。
リミットスイッチの微調整 |
概ね完成した顕微鏡ステージ |
電気配線を終えた顕微鏡ステージ |
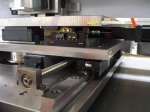 |
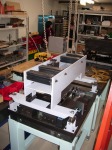 |
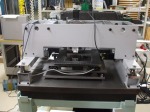 |
このページの先頭に戻ります。
耐震改修工事のための顕微鏡ステージの移動と修理作業
高速顕微鏡ステージは全部で4台作りました。振動を抑えることや、照明光学系の解決ができず、時間が大きく過ぎてしまいましたが、なんとかOPERA事件の解析に間に合わせることができました。
機械ができたあとはメンテナンスです。
この章は高速ステージのメンテナンス作業を書き足していきます。
- 耐震改修工事のための顕微鏡ステージの移動
顕微鏡ステージは非常にデリケートな精密機械です。一度業者に頼んで失敗したことがあったので、今回は全部自前で行いました。
移動式クレーン、床上操作クレーン、玉がけの資格をもっているので、クレーン付きトラックを建設機材レンタル会社から借り、顕微鏡ステージの分解、養生、トラックへの積み込み、運搬、新しい実験室への荷降ろし、再組立、調整という一連の作業を行いました。
顕微鏡ステージは金工室製4台と日本光学のものを含め、全部で4回にわたる作業となりました。
第一回目は手探り状態、二回目は締め具が緩み、ステージが移動したハプニングがありましたが、それ以降はスムーズに運びました。
- 故障の修理
引越し作業後、順調に稼動していた顕微鏡ステージですが、1台(1号機)のX軸から異音が出るとの報告を受け、修理することになりました。
症状からすると、駆動用のボールネジが破損していることが予想されたので、交換できる準備をし、交換作業そのものは2時間程度で終了。解析装置がフル稼働している情況で少しでも止める時間を短くしたかったので短時間で修理できてよかったです。
修理前は、ボールネジの損傷により精度が大きく損なわれていたものが、修理後は目標の精度を充分満足するものとなり、一安心です。
下の写真は、修理前後の原子核乾板を解析したときの角度の誤差を表しています。巾が狭いほど角度再現性が高い、つまり、X−Y座標の再現性がよいということになります。
修理前の角度分解能 |
修理後の角度分解能 |
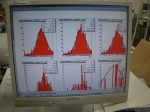 |
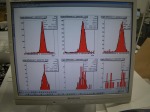 |
このページの先頭に戻ります。
試作機から量産型ステージへの変更のまとめ
コストダウンを図った量産型NewStageの仮組立作業を進めると、最初気づかなかった様々な問題点のあることが判明した。それは照明光学系を調整する機構の組み込みが難しいこと、S-UTSを取り付けたZ軸粗動ステージに求められる位置決め精度が予想外に必要なこと、X−Yステージに要求される速度安定性を得るには可動範囲を広げる必要があること、解析負担軽減のために座標分解能に匹敵する座標精度(X−Y直交精度など)が必要など、全てこの量産型ステージで解決しなければならない。
今回、これらの問題のうちの幾つかを解決できたので、当初の目的であったOPERA実験の原子核乾板解析用としては満足のいく顕微鏡ステージを実現できる見通しが付いたといえる。
改良したところ
- Z軸粗動ステージの取り付け方法を工夫し、S−UTS稼動時の位置安定性を改善した
この問題は300x300mmのH型鋼を使ってS-UTSを取り付けることにより、Z軸の支持部分の重量が約100Kgとなって、S-UTSの振動エネルギーと可動部分の重量との比による精度が理論上要求値を満たすという設計思想で、どのような支持方法がよいかを試行錯誤した。
その結果、H型鋼を二次断面モーメントの大きい方を垂直軸にとり、向かい合わせた板の共鳴を何本かの支柱(内部に鉛の小球を入れて共鳴を防ぐ)によって取り除く構造を採用した。
- 顕微鏡ステージのベースとなる定盤(鋳鉄製)を試作機より大きくしたことで振動などの問題解決を容易にした
試作Stageでは600x1000mmの定盤を使用したが、定盤上部が手狭なため、量産型は750x1000mmを採用した。これにより、重量も約100Kgから200Kgへと大きく変化、その結果、振動などの問題解決を「重量」が増すことによって容易になるという副産物も得られた。
定盤を支える架台は肉厚の鉄角パイプを溶接し、足の部分に防振ゴムパッド付きのスイベルを固定した。これにより設置場所によらず水準器によって装置の水平を出すことができるので、組立精度を確認していくうえで重要な足がかりとなった。
- 照明光学系を定盤の中心に穴加工し、微動機構も含めた無理ない配置を実現した
照明光学系はファイバーによって光を導くものにするが、定盤にφ50の穴をあけて、そこに照明光学系の微動機構を配置することにした。ファイバーは下から通す形式の最も単純な形となった。
微動機構はプランジャーのバネを利用してX−Y平面で±1mm動く簡単なものとし、上下は固定ネジを緩めて直接下から高さを合わせる構造とした。上下はネジによって微動できたほうがよいので、その点を改造することにする。
- X−Yステージの可動範囲を広くしたことで原子核乾板を設置するローダーの設計を容易にした
原子核乾板の大きさは125x100mmであることから、当初ステージの可動範囲を130x110mmで設計したが、両端のリミットスイッチなど安全装置との間隔や安定走行速度を得るまでの助走距離の問題など、主に制御の制限から可動範囲を拡大する必要が生じた。
直線案内レールの可動範囲を限界まで利用すると、150x150mmは実現可能である。これによって、原子核乾板のローダー(次動的に乾板をセットする装置)の開発も容易となる。
可動範囲を拡大したために、ボールネジやリニアゲージの長さが足りなくなるので、量産型ではこれらの適当な長さを設定しなおす必要がある。
今回の仮組みは、それらの問題を解決するために設計変更を行いつつ進め、組立現場にて穴加工などを行った。
- 駆動用ボールネジの固定端となるベアリングブロックを見直した結果、座標精度を改善した
試作NewStageでは極力市販のベアリングブロックを使うこととしたが、量産型Stageで可動範囲を拡大したり座標精度を向上させる必要から、ボールネジ固定端のベアリングブロックに大きな与圧をかける必要があった。この与圧に耐えられる大きさのベアリングホルダーで適当な寸法のものはないので、結局自分で作ることとなった。
今後、量産する場合は、これを外注加工とするが、加工費用を抑える設計とする。
- 組立時に直線案内精度と直交精度を確認することにより、理想的な直交座標系を実現できた
ストレートエッジを使ってリニアガイドの直線走行精度を確認する組立方法を確立、それぞれの軸が2μm以内の誤差に収まるよう君立てることが可能となった。
X軸とY軸の直交精度は直角マスター(200x300mm、ミツトヨ製)を使って検証するが、これもステージのフルスケール(全可動範囲)で2μm以内の誤差に収まることを確認した。
これにより、X−Yステージの絶対精度が確保できるので、原子核乾板の解析効率向上に寄与することができる。
上記改良によって生じた新たな問題点
- 全体の重量が400Kgを超えるなど、当初予定していた重量を大幅に超過した
建物の床の強度が問題となる。1台の解析装置(顕微鏡ステージ)が400Kg超となったことから、装置を集中配置すると床の耐荷重を超える恐れがある。
- 可動範囲を大きくしたことで、スケールやボールネジなどを買いなおす必要が生じた
ボールネジとリニアスケールを買いなおす必要が生じた。
ボールネジは開発段階で入手が困難だったので必要最小限しか購入しなかったことから、新たに買い足せばよいが、リニアスケールは少々もったいないことになった。
リニアスケールはミツトヨのAT−25(基本ピッチ8μm)長さ150mmを沢山購入しているが、応答速度が遅いこともあわせて、NewStageのX軸には使いづらくなった。これはZステージで活用していくことを考えたい。
このページの先頭に戻ります。
OPERA実験用メカニカルステージの必要性
原子核乾板には膨大な量の素粒子飛跡が記録されています。我々が必要な素粒子の飛跡はそれらの中のたった一つです。このたった一つの飛跡を効率よく選び出す技術の開発によって、原子核乾板は今日高エネルギー実験の有力なディテクタとして機能しています。
OPERA実験では、毎日数個の有用な反応があり、その反応がおきたと思われるECCモジュールが取り出されて、現像されます。これをリアルタイムで直ちに素粒子解析できる装置を目指すのが、この素粒子飛跡検出装置の技術開発の目的です。
F研では、最新のエレクトロニクス技術を駆使して、CCDカメラからの高速画像取込を可能とし、同時に素粒子飛跡の効率的な検出をおこなう事のできる自動素粒子検出装置を開発しました。このことにより、OPERA実験での大量の原子核乾板の解析がほぼリアルタイムで可能とする可能性ができました。この自動素粒子検出装置の性能に見合うようにメカニカルステージを動かそうとすると、これまでの10倍〜100倍の速度が必要となります。
我々の技術開発は、メカニカルテーブルと顕微鏡を組み合わせた従来の素粒子検出装置(半自動)から脱皮して、素粒子反応自動検出ロボットのような装置を考えています。従来の直線案内を用いたメカニカルテーブルの考え方に縛られない自由で柔軟な発想が要求されています。
OPERAの実験の成否は、ニュートリノ反応を如何に効率よく検出し解析するかにかかっています。OPERA実験は、ニュートリノ反応があったと思われる個所のECCブロックを一日に十数個取り出し、現像します。1個のECCブロックは4x5インチの原子核乾板56枚からなっているので、一日に500〜800枚処理しなければなりません。解析用顕微鏡ステージを10台用意するとしても、50〜80枚/日の処理速度が要求されます。こうしたことから、1枚の原子核乾板の処理時間は10分程度で処理しなければならないことになります。
このようなことから、OPERA実験のリアルタイムな解析を実現できるそして、CCD&画像処理システムの速度に見合う、新たな高速ステージの開発が必要となりました。
このページの先頭に戻ります。
S-UTS-Stageの仕様
我々はF研によって新たに開発された素粒子飛跡検出装置の特徴を生かすため、Z軸をピエゾ素子によって100Hzで振動させ、原子核乾板の厚み方向の情報を取込みながら横方向に捜引して連続的に三次元の素粒子飛跡を捉えてしまうシステム(S-UTS)を考えました。
S-UTSに必要なメカニカルステージは、一定速度で動くX軸と、画像の回転などを生じないY軸及びZ軸の比較的荒い駆動(位置決め精度はさほど必要ないが、他の軸が動いているときにきちんと止まっている事が重要)があればよいことになります。
従来の画像取り込み装置UTSのCCD部分 | 新しい画像取り込み装置S-UTS |
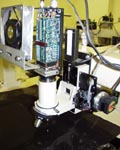 |
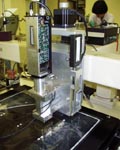 |
従来のメカニカルステージでこの作業を行なおうとすると、0.1μmの座標読取り精度と、100mm/秒の高速走行を同時に実現できるメカニカルステージが必要となってしまいます。このようなステージは半導体産業などで広く使われていますが、1台1億円もすると聞いています。これを10〜20台も保持する事はあまりにも現実離れしているので、原子核乾板の画像取り込み方法を工夫し、グレードを落とさずに如何にメカニカルステージの負担を軽くするかを考えた結果がS-UTSとそれを支える新しいメカニカルステージ=OPERA-Stageなのです。
OPERA-Stageの開発は、0.1μmの座標分解能をメカニカルステージで実現するのではなく、原子核乾板の特長を生かして、S-UTSに取り付けたピエゾ素子によるサブユニットで分解能を稼ぐ方法で実現しようというものです。
このような方法による新しいステージ(S-UTS-Stage)の仕様は以下の通りです。
- X−Yのうち1軸のみ速度変動率1%以内で駆動できること
- ステージは中抜きタイプで、中央の窓は180mm角以上あること
- 各軸のストロークは150mm以上、あるいは、120mmx170mmあること
- すべての軸は0.1μmの座標分解能が必要
- S-UPS稼動時、主光軸と原子核乾板の相対的な震度が0.1μmを超えないこと
- リニアスケールの読み出し速度は10msec以内
- モーター駆動装置はパルス入力でも電圧入力でもよい
- 高さ制限、重さ制限、面積制限は特にないが、室温は±2℃以内で調整されている(原子核乾板からの条件)
このページの先頭に戻ります。
従来のメカニカルステージの問題点
- 三鷹光機の精密二次元座標測定器
この顕微鏡ステージは三鷹光機が25年前に作ったものです。直線案内は正方形の断面をもつレールによっています。レールをボールベアリングの車輪が走行するようになっていて、極めて軽い摩擦係数の直線案内を得ています。
この顕微鏡ステージは、当時最も高い精度(1μmの座標分解能)を実現しています。
三鷹光機の精密二次元座標測定器 |
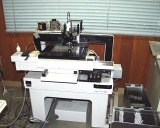 |
- 量産型のニコンステージ
現在はストローク450mmのニコン製メカニカルステージを用いています。このステージは、THKのリニアベアリング、ボールねじ、オリエンタルモータの5相マイクロステップモータ、ハイデンハインのガラススケールという基本パーツをオーソドックスに配置したものです。
このステージの座標分解能は数μm程度ですが、我々のこれまでの要求に十分耐える性能でした。
ニコンステージ | エンコーダ取り付け部 | 駆動部 | CCDカメラ |
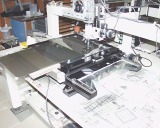 |
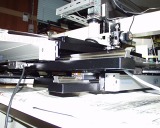 |
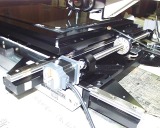 |
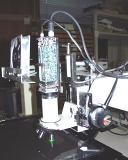 |
- 各社のステージの等速駆動時の性能評価
以下の表は、各種X−Yステージの性能(駆動速度10mm/sec、10msecのサンプリング)を比較したものです。
機種 | 直線案内の種類 | 駆動方法 | 速度変動率(%) |
ニコンステージ−1 | THKリニアガイド | ボールS+StepM | ±2(P-P) |
ニコンステージ−2 | THKリニアガイド | ボールS+StepM | ±3(P-P) |
ニコンステージ−3 | THKリニアガイド | ボールS+StepM | ±7(P-P) |
THKステージ | THKリニアガイド | ボールS+ACサーボ | 5(RMS) |
NSKステージ | NSKリニアガイド | リニアモータ | ±3(P-P) |
NTNステージ | NTNリニアガイド | ボールS+ACサーボ | 5(RMS) |
NTNステージ | エアスライド | ボールS+ACサーボ | 2 |
NSKエアスライド | エアスライド | リニアモータ | ±0.1(P-P) |
調査に関するコメント
1、エアスライド+リニアモータはオーバースペック
2、速度変動率がP−PとRMSがあって、単純には比較できない
3、3台のニコンステージの結果は、組付けによる性能の変化が大きいことを示している
4、全体としては、ボールねじが速度変動率を悪くしているように見える
- リニアガイドとボールねじ駆動のメカニカルステージの問題点
リニアガイドとボールねじ駆動を組み合わせたメカニカルステージは、容易に高精度のものを実現できます。しかし、我々が必要とする中抜きのメカニカルステージの限界精度は数μmといわれています。
我々は、この組み合わせによって新しいメカニカルステージに要求されている等速運動性能を測定しました。以下に示すグラフはNikonステージを様々な方法で駆動したときの速度変動を表したものです。右下はボールねじ駆動の速度変動をFFT解析したものです。
CFひもで引張る |
ボールねじ駆動の良好なもの |
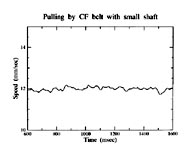 |
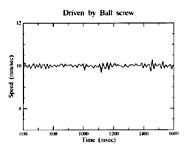 |
ボールねじ駆動(多数) |
FFT解析 |
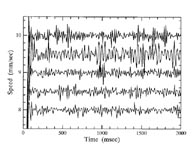 |
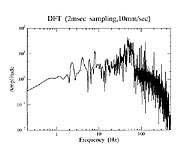 |
- 既存のメカニカルステージのまとめ
以上の結果から、エアスライド+リニアモータの組合わせならば簡単に我々の求めるスペックを満たす事ができると思います。この場合コスト高が問題です。
しかし、Nikonステージの駆動試験から、速度変動の主な原因となる機構部品や駆動方法・組立精度などの因果関係を見ると、リニアガイド+ボールねじの組み合わせでも、駆動速度10mm/sec、10msecのサンプリングにおいて速度変動率1%以下は実現できる可能性があります。
このページの先頭に戻ります。
TEST-Stage
以上の結果から、リニアガイド+ボールねじによるメカニカルステージにおいても、理想的な構造と部品配置を考えたものによって等速駆動性能1%を達成できるのではないかと考え、同方式によって1軸の試作1号機(TEST-Stage)を製作し、データを取る事にしました。
TEST-Stageの設計コンセプトは以下の通りです。
- 高剛性
- 三点支持
- 重心駆動
- 一定摩擦
- 案内軌道と駆動軌道の誤差吸収機構
- 高分解能スケールによる速度管理
- トルクむらの少ないモーターによる駆動
- 熱膨張係数の異なる素材を構造材に持ち込まない
8、は特に、精度に直接関係するリニアガイドとボールねじが鋼なので、それを直接取り付けているプレート他の構造物を同じ熱膨張係数の鋼(今回はS55C)に統一する事により、熱膨張係数の違いから出てくる経年変化を少なくするとともに、高剛性によるメリットを狙いました。
Z軸のS-UTSを100Hzで振動させる事になるので、X−Yテーブルは重いほうが良いという判断もあります。
以下に上記コンセプトによるラフスケッチを示します。
三次元イメージ |
上面図 |
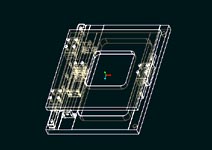 |
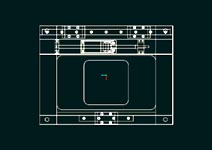 |
使用した機構部品
- ボールスクリュー
W1203FA-1P-C3Z5(NSK) リード5mm 精度C3
- リニアガイド
SHS25 (THK)
- リニアスケール
AT25−200(ミツトヨ) 基本ピッチ8μm、80分割にて0.1μmの分解能
TEST-Stageの組み立てと速度測定
TEST-Stageは1000x600の箱型定盤を天板とした台(鉄角パイプの溶接構造)のほぼ中央に組み付けました。
30mm厚のS55C板を直線案内(リニアガイド)の基準面としました。この板は定盤から豆ジャッキで浮かす構造をとりました。これは、下の定盤が必ずしも平面ではないためです。定盤はその重量によって振動の影響を緩和する効果を期待しています。
30mm厚のS55C板に、リニアガイド、ボールねじ、モーターブラケットなどを固定した後、メカニカルステージの天板を載せ、リニアガイドのライナーとボールねじのナット側金具を固定します。これでメカニカルステージの主要な部分は組立て完了です。
次に速度特性を測定します。手っ取り早く試験するためにステップモータ(オリエンタルモータ)を取り付け、位置測定にはリニアゲージ(ハイデンハイン)をマグネットベースによって取り付けました。
速度特性を測るときに重要なことは、リニアゲージのAD変換誤差によるスケール基準ピッチ内の揺らぎです。ハイデンハインのゲージを使ってきた印象では、20μmの基準ピッチ中2〜3μmのゆらぎが繰り返し誤差となって現れているようなので、これを無視できる測定方法を考えることです。我々は基準ピッチ(20μm)変化したときにかかった時間を測定することで、ゆらぎによる誤差が速度変動率に乗らないようにできました。
高分解能のエンコーダは必ずこうした基本ピッチでの繰り返し誤差を持っています。南アフリカ望遠鏡の追尾精度を測定したときも同じ問題に悩まされました。この時は単に測定だけでは済まされない(制御のリファレンスとして使っていた)ので、補正テーブルを作って正しい値を得ることに成功しました。
次の写真はTEST-Stageと、速度測定の様子、そして速度変動率です。
組みあがったTEST-Stage |
リニアゲージの取り付け |
速度変動率 |
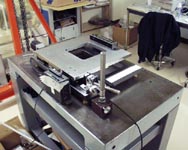 |
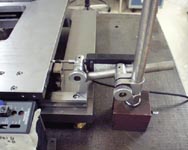 |
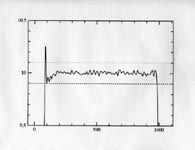 |
この時の速度変動率は、縦軸を速度、横軸を移動量としており、上下の点線は1%を示しています。Nikonステージの速度変動率と比べるとその違いが良く分ります。
Nikonステージでの測定より厳しい条件となっています。それは、リニアゲージを定盤面からマグネットベースで取り付けたことで、一つ余分な振動系を入れてしまっていることです。従って、起動時に大きなリンギングが現れました。しかし、それでもなお、中間の一定速度を保っている部分では、目標の1%より小さく、0.3〜0.5%程度になっていることがわかります。
この速度変動率はエアスライドとリニアモータを組み合わせたメカニカルステージに匹敵するものです。
この結果から、速度変動率1%以内のメカニカルステージは、従来のリニアガイドとボールねじの構成によっても十分実現できることがわかりました。
以上の結果から、TEST-StageはOPERAの原子核乾板スキャン用精密ステージ(等速駆動ユニット)としての仕様を十分満たしており、TEST-Stageで得た技術を他の軸に用いることによって、OPERA実験での原子核乾板解析用ステージ(OPERA-Stage)の開発にめどをつけることができました。
このページの先頭に戻ります。
高剛性Z軸ステージの設計
S-UTSは主光学系をピエゾ素子によって高速駆動するため、振動エネルギーに打ち勝って主光軸を0.1μmの精度で保持しなければなりません。現在はシグマ光機のメカニカルステージを用いていますが、これは強度不足です。
従って、TEST-Stageで得た成果を実際に試すために、極めて剛性の高いZ-Stageを新たに設計・製作することにしました。
このZ-Stageの設計プランは、先の新設計ステージでの経験を生かし、シンプルなデザインとして、部品の加工精度1μm以内も十分期待できるようにしました。
リニアガイドはTHKのSHS25、ボールスクリューはNSKのW1601MA-1PY-C3Z2を採用、全て与圧のかかったものを選び、軸受けにも与圧をかけ、モーターとの結合は捩じれ剛性の高いカップリングを用います。リニアガイド取付板や天板などの構造部品はダイス鋼(SKD)を使用しました。
リニアガイドとボールスクリューの配置 | 高剛性Z軸ステージの完成予想図 |
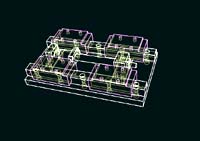 |
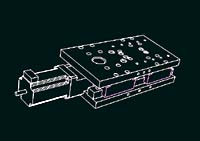 |
このZ-Stageは一応完成して、静的な負荷試験を行った結果、XY方向に対する剛性は十分でしたが、Z軸方向の剛性が不足していました。それは、Z軸方向の剛性を決める経路にいくつかの部品が関与していることと同時に、市販のボールネジ軸受け(固定端)の剛性が他の部分に比較して大きく取れないことに原因が有ります。
市販品の軸受けでは剛性不足なので、この部分のみ、特別に大きいボールサイズのアンギュラベアリングを使ったベアリングブロックを設計し直しました。
現在、このZ軸ステージは完成し、動特性の評価を待つ状況です。
完成したZ-Stage1 | 完成したZ-Stage12 |
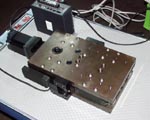 |
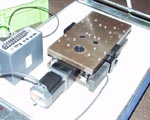 |
このページの先頭に戻ります。
最新設計のXYステージ
OPERA-Stageの前段階として、TEST-Stageを直交配置してXYステージとするような2軸構成のXY-Stageの設計を始めました。
X軸にTEST-Stageをそのまま配置し、その下に、Z-Stageを中抜き構造としたようなY-Stageを配置する構造で設計を進めました。
Y軸にZ-Stageと同様の高い剛性を持たせるのは、S-UTSの振動の影響を受けないようにするためです。従って、このXYステージは、従来のメカニカルステージと比較して非常に高い剛性をもっています。このXYステージは9月中旬には組立てに入り、10月には基礎的な性能評価を行えるよう準備を進めています。
XYステージの三次元イメージ1 | XYステージの三次元イメージ2 |
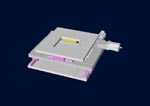 |
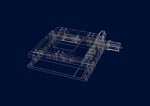 |
このページの先頭に戻ります。
OPERA実験用STAGE
試作したXYステージの上にZステージを強固なトラスで支える構造の3軸メカニカルステージとして、OPERA実験用STAGEをまとめました。
トラスの支柱によって、前後左右に空間ができ、原子核乾板の載せ替え装置との連携が楽な設計になっています。
OPERA-STAGEの三次元イメージ | 試作中のOPERA-STAGE |
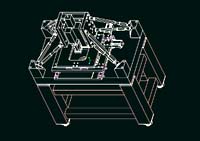 |
 |
右の写真は、仮組みを終えたOPERA-STAGE試作機です。この3軸メカニカルステージは、Z軸の保持にトラス構造を用いたところがこれまでの物と異なっています。
このZ軸保持構造の振動解析を進めています。写真中央に写っているものはS-UTSの5倍〜8倍の振動を発生させる装置です。振動をホール素子によってモニターしたところ、Z軸保持構造の共振周波数は25〜30Hz、X−Yステージの共振周波数は200Hz程度であることがわかりました。
ホール素子による振動測定はメカニカルステージ静止時しかできないので、PCによる総合的な制御環境を早急に整えることが、必要です。
このページの先頭に戻ります。
OPERA実験用NewStageの速度特性
これまでにNewStageの等速運転における速度安定性を測定してきましたが、十分な結果を得られていません。丁度使用したい速度付近に共鳴があって、原子核乾板の解析に必要な精度をまだ達成できていません。
ステージの駆動系メカ部品の共振が考えられるので、共振の可能性がある部品を交換し、共鳴周波数が移動するか同かを確認しましたが、メカには依存しないことがわかりました。
この結果、ステッピングモータを駆動しているドライバーの電気回路やコントローラーボード側に問題があり、丁度その速度で共振する組み合わせになってしまた野ではないかと考えています。
改善方法は、ドライバーを変える、モーターをACサーボモータに変えTノッチフィルター等で共振を取り除く、共振点付近を使わないようにボールネジのピッチを変える、などが考えられます。
当面、メカの変更はせず、ドライバーのPWM周波数などを変えるか、専用のドライバーを作るなどの対応を考えています。
S-UTSとZ-Stageを乗せたNewStage | NewStageのX-Axis駆動部分 |
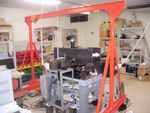 |
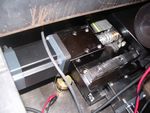 |
このページの先頭に戻ります。
NewStageにS-UTSを仮搭載、振動特性を測定
2005年末にS-UTSを搭載するため、NewStageにZ-Stage-Baseを搭載し、S-UTSを稼動させて振動試験を始めました。
300x300のH鋼を約1000mmで切断すると概ね100Kgの重量となります。S-UTSの振動マスは200g、これを200μm100Hzで振動させます。
H鋼のZ-Stage-Baseを何の対策もせずNewStageにネジ固定して、S-UTSを振動させると、97Hzに大きな共振のピークがあり、目標の周波数100Hz付近の振動の大きさは12μm(P-P)となりました。
ここから振動を取り除いて、目標の0.2μm以下になるようにしなければなりません。
S-UTSとZ-Stageを搭載したNewStage | H鋼につっかい棒を入れて振動ダンプ |
鉛板によるダンプ | ゲージを使った振動測定 |
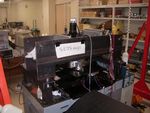 |
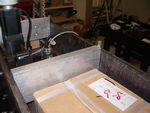 |
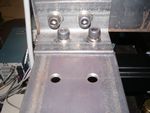 |
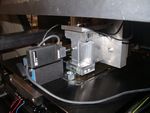 |
対策1
H鋼の共振を止めるため、上側の2箇所にアルミ製のつっかい棒を入れ、H鋼の下に鉛板(肉厚1mm)を入れ、振動を調べたところ、大きな共振は見えなくなりましたが、相変わらず97Hzに共振点があり、振動の大きさは2μm(P-P)でした。
この振動の大きさは、床から立ち上げたベースにゲージをつけて測定したので、実際のCCD画像の振動とは異なります。
NewStageの載物台