測定器の使い方
更新記録、2009年1月13日、アクセス解析のためカウンターを付けました。
実験装置を作る時に必ず行うのが部品などの寸法を測ることです。ものさしだけでは良い実験装置はつくれません。
ここでは、大学の実験室でよく使う長さを測る測定器について、その種類と特徴、使い方を説明します。
私たちは大学の工作室で実験装置の試作・製作・組立をおこなっていますので、町工場と同じようなは機械工作時の寸法を精度よく行う必要があります。最初にそうした加工現場でよく使うノギスやマイクロメータの使い方を説明します。そして、寸法以外の計測についても順次紹介していく予定です。
機械工作で正確な寸法を得るためにはノギスやマイクロメータを上手に使って正確な測定を行う必要があります。
ここでは、工作現場でよく使う測定工具とその正しい使い方を解説すると同時に、コンパスやスケールなどの便利な使い方も紹介しますします。
単に長さの測定と言っても、それぞれのスキルや測定工具によって測定精度や信頼性は大きく異なってきます。アマチュア的あるいは古典的な方法からミクロンオーダーの専門的な測定まで、様々な方法を紹介し、測定の目的と結果の利用という観点で整理し、加工精度や組み立てを考慮に入れた実践的計測を考えていただければと思います。
このような目的で「目で見てわかる測定工具の使い方」を日刊工業新聞社より出版しました。本書はこのホームページを元に全体を整理して多数の写真や図を加え、古典的で手近にある測定工具の使い方を初心者でもすぐわかるよう編集したものです。百戦錬磨の中堅・ベテランの方々はみなご存知の内容ですが、手元の測定工具を網羅したので、若手教育の参考書としてもご活用いただければと思います。
工作の現場で必要となる寸法測定
- スケール
単純な「ものさし」ですが、加工現場では重宝です。
- ノギス
加工現場では代表的な測定器です。ノギスを上手な使い方や知っておくと便利な情報を掲載します。
- マイクロメータ
ノギスの精度では足らないとき、マイクロメータが必要です。慣れればベアリングのはめあい程度の精度を管理できます。
- パスとコンパス
古典的となってしまいましたが、パスでなければ計れない部分もあります。
- ダイヤルゲージとピークメータ
連続的な変位を見ることが出来るので、芯出しや倣い精度の確認には必需品です。
- 各種ゲージ
ねじのピッチ、角のR、角度、隙間など、様々なゲージがあります。
精密な測定の基準となったり、機会の整備などに必要な測定器
一次元の寸法精度では困るとき、二次元〜三次元の測定が必要です。
- 工具顕微鏡
CCDカメラと組み合わせて顕微鏡で拡大しながら二次元測定ができます。
- 三次元測定器
接触式のセンサーと組み合わせて、幾何公差の定義に基づく三次元計測ができます。
実験装置を作るとき、寸法や長さ以外の測定も必要となります。ここでは金工室で実現可能な方法を解説します。
- 硬さ試験機
金属の熱処理を行った後、その処理が適切であったかどうかを確認するには硬さを調べます。
- Heリークディテクター
真空容器を製作する場合、必ず必要になるのが漏れ試験機です。
- ひずみ測定
ひずみ測定は材料力学の応力によるひずみを測定するもので、高圧や高加速度のかかる部分の評価には必要不可欠です。
- トルク測定
トルク測定やトルク管理は精密組み立てになくてはならない技術です。
このPAGEについてのご意見は kawai*tech7.sci.nagoya-u.ac.jpまでお願いします。(スパム防止のために@を*で表現しいますので、この部分を書き換えてください)
スケール
単純な金属製の「ものさし」ですが、裏側にはインチの変換表が付いています。
150、300、600、1000、1500(mm)という長さのものが市販されています。
最も基本的な使い方としては、加工物の大きさを見たり、けがき作業(穴の中心位置などに印を付ける作業)に用います。このとき用いる金属製の尖った棒は「けがき針」です。コンパスの開きなどもスケールを目安にします。
色々な長さのスケール | スケールの目盛り | スケールの裏側 |
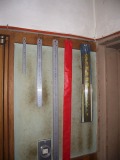 |
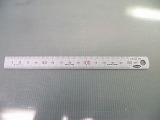 |
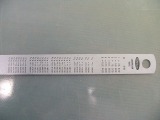 |
けがき針とスケール | けがき作業 | コンパスとスケール |
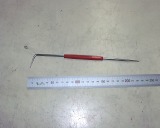 |
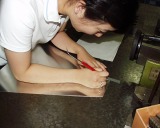 |
 |
スケールの最も単純な長さを計る機能にしても、旋盤やフライス盤加工で途中経過を確認するときなど、短時間にさっと寸法を確認できるため、色々便利に使えます。
スケール立てとトースカンを用いて、定盤の上で効率よくけがき作業を行なうことが出来ますが、ハイトゲージが普及してからはほとんど使われなくなりました。
return to top !
パスとコンパス
パスは古典的な道具ですが、使い方を知っておくと大変便利です。ベテランの旋盤工はパスを上手に使い、0.01mmの精度の加工もパスで対応可能だと言われています。
パスには外パスと内パス、片パスの3種類があります。
measure
パスの開きはスケールだけでなく、ノギスやマイクロメータ、ブロックゲージから寸法を写し取ることができます。
熟練すると、パスのたわみを利用してどれぐらいの誤差に入っているかなどを知ることが出来ます。
コンパスはけがき作業でよく使います。
中学・高校のころ、数学の図学で使ったように、二等分線、三角形の重心、円周の6等分、直交する線分などを思い出してください。これらはけがき作業の基本的なものばかりです。
return to top !
ノギス
旋盤やフライス盤の加工現場でノギスは最も基本的な測定工具です。
ノギスの大きな特徴はバーニアスケールの存在です。バーニアスケールとは、荒い目盛りと細かい目盛りを組み合わせてより小さな値を読み取るようにしたもので、19mm(あるいは39mm)を20等分(あるいは50等分)したものをバーニアスケールとします。この場合、20等分であれば最小読み取りは0.05mm、50等分であれば0.02mmとなります。
下の写真はM型ノギスです。このノギスは外径を測定するジョウの部分のほかに、内径用のクチバシ、段差や穴の深さを測定するデプスバーの3箇所で測定することが出来ます。
右端の写真のバーニアの読みは、25.60mm〜25.65mmとなります。
ノギスは錆にくく硬いSUS420J2が使われています。
M型ノギス | ジョー | クチバシ | デプスバー | バーニアスケールの読み |
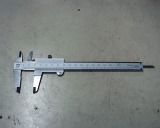 |
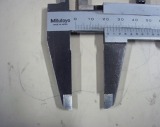 |
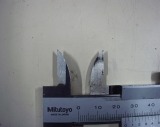 |
 |
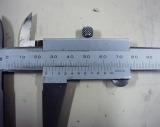 |
バーニアスケールは便利ですが、スケールの正面に目をもってこないと視差による誤差が出ます。この視差による誤差をなくすために開発されたのがダイヤル付きノギスやデジタルノギスです。
また、測定のレンジも様々なものがあります。市販品のカタログには100mm〜1000mmが掲載されています。下の写真は150mm〜500mmののぎすです。
ダイヤルやデジタルノギス | 様々な大きさのノギス |
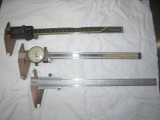 |
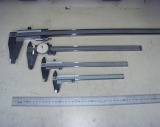 |
工作現場でノギスを使って測定している様子を示します。
重要なことは、2つあります。
一つは、ノギスの当て方です。
直方体の場合は測定したい平行する面に垂直にノギスのジョウなりクチバシをあてます。円筒の直径を計る場合は円筒の軸に対してノギスが直角になるようにジョウを当てます。このときに直角からずれていれば長いほうに誤差が出ます。
もう一つはノギスの目盛りのある面に垂直の位置に自分の目がくるようにします。これは主尺と副尺の面の高さが尖っているので斜めから見ると視差ができるからです。
そのほかに、測定時に隙間のないようにと考えて力を入れすぎてもいけません。
ノギスの分解能は0.05mmですが、ノギスを使った測定では上記のような誤差が付きまとうので、プラスマイナス0.2mm以内の精度しか保証できません。
自分専用のノギスを持っていて、ノギスの使い方に慣れ、時々校正などを行って良好なコンディションを保つことができれば、0.1mm以内の精度で図ることができます。
ダイヤル付きやデジタルノギスなど、分解能が高くなっていますが、視差による誤差がなくなっただけで、依然として当て方による誤差が生じることから、読み取った数値を鵜呑みにして0.01mmの精度で測ったと思ってはいけません。
立方体の寸法を測る | 穴の直径を測る | バイスに付けたまま測る | デプスバーで測る |
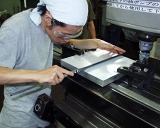 |
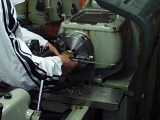 |
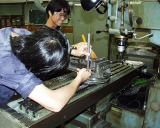 |
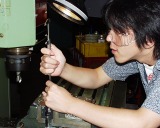 |
return to top !
マイクロメータ
マイクロメータはノギスとならんでよく使う測定工具です。
最も一般的なマイクロメータは外径を計るもので、フレームの両端にアンビルとマイクロメータヘッドが配置された構造になっています。このネジとシンブルの部分をマイクロメータヘッドといって、共通の部品になっており、25mmのストロークがあります。
シンブルシンブル(回転する部分)は一回転0.5mmの精密なネジになっており、シンブルの円筒面に50等分の目盛りを入れておくことで、0.01mmの分解能をもった測定を可能にしています。
シンブルの先には測定圧力を一定にするためのラチェットストップが付いてます。
右端の写真にあるマイクロメータの読みは、3.13mmとなります。
マイクロメータ | マイクロメータヘッドとシンブル | ラチェットストップ | マイクロメータの読み |
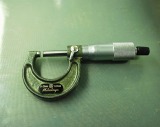 |
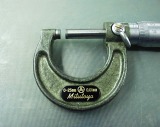 |
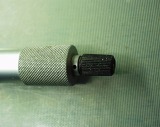 |
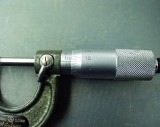 |
マイクロメータの原理を用いた測定工具はたくさんあります。
内径専用のマイクロメータによる測定は外形の測定に比較して非常に難しくなります。
大きい内径の測定には棒型内側マイクロメータを使います。
小さい内径の測定には3点式ホールメータが便利です。
内側マイクロメータ | 棒型マイクロメータ | 3点式ホールメータ |
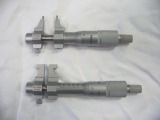 |
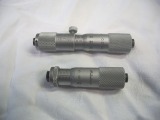 |
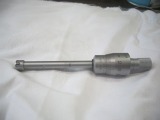 |
マイクロメータの校正にはブロックゲージを用います。このとき、フレームを素手で持っていると体温で膨張するため、正しい値がでません。こんなときにはマイクロメータスタンドを用います。
マイクロメータのアンビルとスピンドル先端の平行度はオプティカルフラットをはさんでニュートンリングを確認します。
最近、デジタルマイクロメータが普及してきました。デジタルマイクロメータはアンビルの部分にロータリーエンコーダーを組み込んで1μmの分解能を実現したものです。
基本的な性能はアンビルの中のネジの精度によるので従来のマイクロメータと同じですが、表示誤差や分解能がたかいために便利に使うことが出来ます。
マイクロメータスタンド | オプティカルフラットによる検査 | デジタルマイクロメータ |
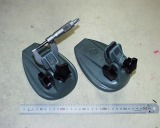 |
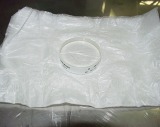 |
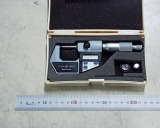 |
マイクロメータを使った測定を紹介します。
ボールベアリングなどの軸や取り付け穴はミクロン単位の精度が要求されます。しかし、マイクロメータの分解能は10μmですから、ブロックゲージなどでマイクロメータ自体をよく校正しておく必要があります。このとき、ラチェットの具合や繰り返し誤差(再現性)なども入念に確認しておきます。
ノギスの場合と同じで、当て方が難しい。特に内径を計る場合は、穴の軸に直交する位置にマイクロメータをあわせることと、内径の一番広い部分に測定子がきているかなどを注意します。
デジタルマイクロメータは1μmの分解能があり、しっかり校正していればそのまま読み取り値を信頼できます。
フレームを持ってラチェットを回す | 内径の場合、よくなじむ場所を探す |
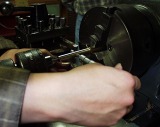 |
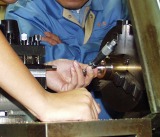 |
ブロックゲージ
ブロックゲージは工場の長さの基準となるもので、マイクロメータやノギスの校正に使ったり、アクセサリーキットと組み合わせて定盤の上で高さ標準や段差測定を行うことに用います。
基本的な組み合わせは、幾つかのブロックを組み合わせて1.000mmから5〜10μmおきに任意の長さを構成できるような組み合わせになっています。
写真のセットは、1.000mmから10μmおきに1.490mmまで49枚、0.5mmから24.50mmまで0.5mmおきに49個、25.0mmから100.0mmまで25.0mmおきに4個、それに2.000mmが2個という組み合わせになっています。
下の写真は、ブロックゲージとアクセサリーキットを組み合わせて高さ標準にしたもので、ダイヤルゲージによって高さの差を測定しているところです。アクセサリーキットはベースブロックとR付きの先端ブロック、留め金などと共に、ナイフエッジなどがセットになっています。
ブロックゲージをサインバーのスペーサーとして用いれば極めて精度のよい角度基準を作ることが出来ます。
アクセサリーキットで高さ標準を作る | サインバーで精密な傾斜を作る |
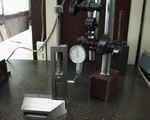 |
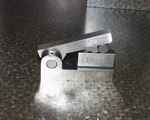 |
ブロックゲージそのものの精度は等級にもよりますが極めて高いものです。しかし、素材そのものの熱膨張係数があるので、環境温度の変化によって変化するので、長い距離の基準にする場合は環境温度を一定にしたり、直接手で触れないよう、手袋を着用します。
ダイヤルゲージとピークメータ
ダイヤルゲージやピークメータなどの回転機構で分解能を上げた測定器は変位量を見るのに便利です。
ダイヤルゲージはマグネットスタンドに取り付けて使うことが多く、マグネットスタンドアームの使い勝手や剛性で誤差ができますが、変位を見るだけなら気軽に高い分解能で調べることが出来るので、非常に便利です。
ダイヤルゲージの分解能は概ね10μm、ストロークは4〜5mmあるので、比較的大きく変位していてもレンジを外れることはありません。それに比べて、てこ式ピークメータの分解能は2μmと高分解能なのですが、ストロークが1mm以下と少ないのが特徴です。
ダイヤルゲージは比較的安価に高分解能の測定器が作れるので、これを利用して、様々な測定器が考案されています。ここではダイヤルキャリパーとシリンダーゲージを紹介します。
ダイヤルゲージ | てこ式ピークメータ | ダイヤルキャリパー | シリンダーゲージ |
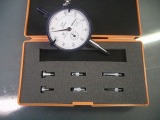 |
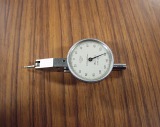 |
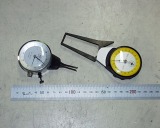 |
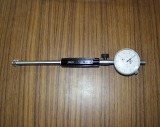 |
ダイヤルゲージやてこ式ピークメータはマグネットスタンドに取り付けて使います。
マグネットスタンドのダイヤルゲージを取り付ける部分に微動装置が付いていると、セッティングが楽に出来ます。
レバー式ピークメータはレバー部分が摩擦継ぎ手になっていて、ぶつかっても先端が壊れることはありません。変位方向を切り替えるレバーが付いていて、これで測定したい方向を決めます。分解能が高いので、微動装置を備えたマグネットスタンドに装着すると良いでしょう。
スタンドの微動装置 | ピークメータ指示方向切り替え |
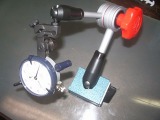 |
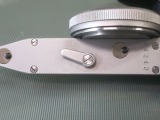 |
ダイヤルゲージを使った測定の例を紹介します。
最初の写真は、ダイヤルゲージによって旋盤加工での円筒部分の振れを見ています。その次は、同じくダイヤルゲージで端面の振れを見ています。最後はフライス盤のテーブル取り付けた工作物の垂直・水平を確認しています。
円筒部の振れ | 端面の振れ | 工作物とテーブルの平行 |
バイスの平行精度 | バイスに固定した工作物の水平 |
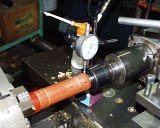 |
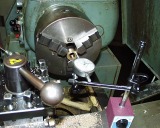 |
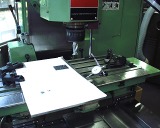 |
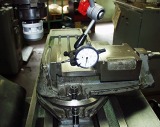 |
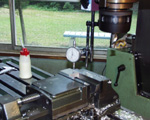 |
てこ式ピークメータを使った測定の例を紹介します。
最初の写真は、旋盤作業で薄肉の加工物をスクロールチャックに固定したときの円筒面の振れや締め付け応力による変形を見ています。次は同様に内側のフランジ端面の振れを見ています。
次の写真はフライス作業での工作物の取り付け精度を確認しています。ダイヤルゲージより厳しい精度を要求されるときに便利ですが、先にダイヤルゲージで概ねあわせておかないと、測定レンジを外れてしまったり、微動装置がないと丁度良いところに取り付けられなかったりします。
ダイヤルゲージを用いた測定器
シリンダーゲージは深い穴やパイプの内径を測るもので、ダイヤルゲージの動きをテコで連動している突起と交換式の突起(固定側)の間隔の変化をダイヤルゲージで読むようになっています。
シリンダーゲージのテコのストロークは0.5mm〜2.0mm程度しかないので、固定側の突起を交換して、目的の直径を測れるようにします。このときの校正はマイクロメータで行います。
交換式突起がセットになって収納されているシリンダーゲージ | 先端の測定部分、交換式突起 | テコと連動している突起 |
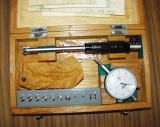 |
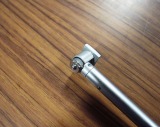 |
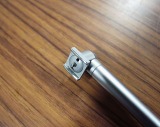 |
デジタルリニアゲージ
ここで紹介するデジタルリニアゲージはダイヤルゲージと同じように、マグネットスタンドなどによって任意も場所に取り付け、芯出しや変位量の確認に用います。分解能は1μm以下のものもあり、ストロークも20mm〜100mmと大きく取れるので非常に便利ですが、あまり分秋能が高いと最後の桁の表示が常に動いていて読みにくいようなこともあります。その場合は読み取り装置の分解能を下げて表示すると良いでしょう。
原理はデジタルリニアスケールと同じで、光学式あるいは磁気式の精密且つ高分解能の測定器です。
デジタルリニアゲージは、ゲージ部分と読み取り表示部分が分かれているものが普通です。読み取り表示装置はパソコンと接続して高度な情報処理を可能にしているものもあります。
ストレートエッジとスコヤ
ここで紹介するストレートエッジは文字通り、直線の基準、スコヤは直角の基準です。
例えば、工作機械のテーブルや刃物台が真っ直ぐに動くかどうかを確かめたり、直交精度を確かめるにはこれらの基準が必要となります。こうした測定はダイヤルゲージやデジタルリニアゲージなどを用いて、ストレートエッジやスコヤの基準面をトレースします。
ストレートエッジは大きな装置を組み立てるときの基準面を確認したり、仮基準面を形成するときなどに使えるので非常に便利です。
加工物の歪みを見る | 加工面の平面性を見る | 直線案内機構の直線性を見る |
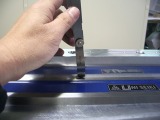 |
 |
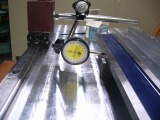 |
各種ゲージ類
ここで紹介するものは、当ててフィットするかどうかを見て確認するような使い方のゲージです。
この他にも色々なゲージが市販されています。
ピッチゲージはねじのピッチが不明なときに、ゲージを当てて、山と谷がきれいにかみ合うかどうかを見て確認します。
シクネスゲージはフランジや板の歪みなどがある場合、厚さの判っている金属片が隙間に入るかどうかを目と手触りで確認します。
ピッチゲージでネジ山のピッチを見る | シクネスゲージで隙間を見る | センターゲージでねじ切りバイトの角度を見る |
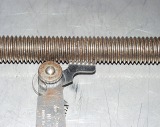 |
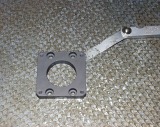 |
 |
加工面荒さは触針式の表面粗さ計で詳しく調べますが、初心者や一般の人に説明するために、表面粗さ見本があります。これは、そのまま目で見たり、手触りで確認してもらえるようになっています。
表面粗さ見本 |
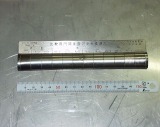 |
水準器
ここで紹介する水準器は長さを測定するものではありませんが、定盤や工作機械を水平に設置するときや望遠鏡など大きな装置を作るときに必ず必要になる水平基準面を確保するための測定器です。
水準器が測定器として用いられた歴史は古く、構造が単純なのでローコストにも関わらず比較的高い精度を実現することが出来ます。
水準器の原理は、わずかに曲がったガラス管の中に気泡と液体を閉じ込めると、凸部分に気泡がくることを利用しています。これに目盛りをつけ、1mあたり0.05mm〜0.02mm程度の分解能をもたせたものが一般的です。しかし、高分解能にすると、曲率を大きくしなければならないので液体の粘性で気泡の動く速度が遅くなり、測定に時間がかかります。
水準器はガラス管を支持するところが狂ってしまうことが多く、正しい水平が読み取れなくなるので、時々反転させて両者の読みが一致することを確認します。もし反転させて気泡の位置が食い違う場合は一致するように調整ネジを回して校正します。このように、他の装置を必要とせずに自分だけで校正できることは水準器による測定の信頼性を高いものにしています。
写真では標準のものと、傾斜を測定するためにマイクロメータの付いた傾斜水準器を紹介します。
標準型水準器 | 傾斜水準器 |
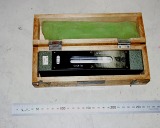 |
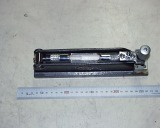 |
水準器を使った作業は、気泡がゆっくり動くので十分時間をかけて目盛りを読み取ることが大切です。同時に、180度反転させて、どちらも同じ目盛りになることを確かめます。もし同じところに来ないならば気泡管の角度を微調整するネジがあるのでそれを調整して同じ値になるようにするか、誤差を見越して読み取るようにします。
180度反転を数回繰り返し、目盛りを平均化したものがその場所の傾斜です。水準器の下面は非常に重要で、この面に損傷がある場合は油砥石などで補修します。
下の写真は、水準器を使った定盤や工作機械の水平出し作業です。水準器の読みを頼りに、前後左右が水平になるようレベリングブロックや据え付け調整ネジなどを調整します。
一般的に、平面は3点で決まります。しかし、定盤や工作機械の据え付けでは4点〜6点の調整箇所があります。調整の仕方は作業すあの好みもありますが、3点支持を基本にして、長手方向の2点で水平を出して、その後短い方の1点で水平を出します。残ったところは荷重が一定になるよう、少しず荷重をかけて、全体の荷重バランスをとります。そして最後に確認のため水準器で水平を確認します。
定盤の水平出し | 旋盤の水平出し |
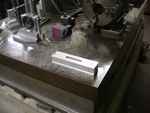 |
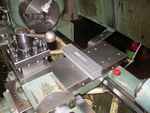 |
同じ水準器が2台以上あると大変便利です。
一箇所に水準器を置いて高さ調整すると、他の位置や方向の平面も変化するので、たくさん置けばそれだけ同時にその位置や方向の水平を見ることが出来ます。
一個では縦横同時に見られない | 二個あると縦横同時に見られる |
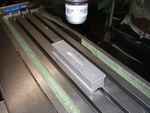 |
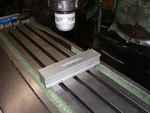 |
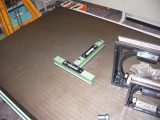 |
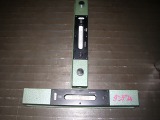 |
最近は電子式水準器があって、2軸同時に測定できたり、気泡式に比べて応答速度が速いなど、高性能のものがあります。
定盤とVブロック・イケール・マス
ここで紹介する定盤とVブロック、イケール、マスは、測定器というよりは精密組立作業の基準面やけがき作業の基準面として用いることが圧倒的に多くなりました。
最近は便利な三次元測定器などが開発されて、これらの道具はあまり測定に使われなくなりましたが、使い方を知っておくと色々なところで応用がききます。
精密定盤 | 摺り合わせ定盤 | マス |
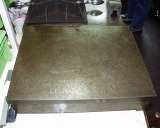 |
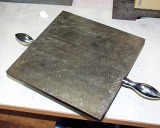 |
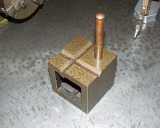 |
イケール | Vブロック(ヤゲン台) | インデックス |
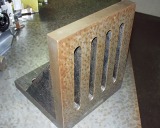 |
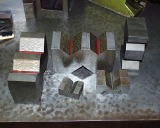 |
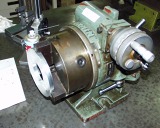 |
工具顕微鏡
工具顕微鏡は載物台に精密な二次元メカニカルステージを用い、透過照明と落照照明の両方を使える顕微鏡で、接眼レンズを用いた測定のほかに、CCDカメラを取り付けて画像取り込みもできる便利な装置です。
工具顕微鏡の用途としては、文字通り、刃物の刃先形状を拡大して測定したり、微小・微細加工の状態を検証することができます。
三次元測定器
三次元測定器にはスタイラスチップを被測定物に触れさせる接触式と、オートフォーカスなどの画像処理技術を駆使した非接触式の二種類があります。
金工室には接触式の比較的小型の三次元測定器があります。
三次元測定器を使うにあたって、幾何公差に関する基本的な知識を身に付けておく必要があります。
Heリークディテクター
真空装置を作るとき、要求されている真空度にもよりますが、真空の漏れ試験を行う必要があります。この漏れ試験においてHeガスを漏れの有無を確認するプローブとして用いるのがHeリークディテクターです。
真空容器の内側を真空引きし、外側からHeガスを吹きかけて内部に侵入したHeガスの有無を質量分析器で調べます。4極子型質量分析計はHeに対する感度を高めることができることや、Heガス分子が自然界の分子の中でも特に小さいので微小隙間も透過することから、非常に感度の高い漏れ試験機となります。
Heリークディテクタの検出部分は4極子型質量分析計なので、被測定容器内部の真空度がある程度高くならないと測定にかけられないことから、大きな漏れには対応しにくいのですが、高真空〜超高真空領域で用いる真空容器の信頼性確認にはぜひとも必要な測定器です。
移動式Heリークディテクター | 据え置き型Heリークディテクタ |
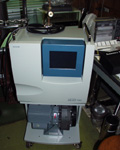 |
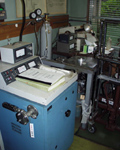 |
移動式は実験場所に持っていってリークテストを実施できるので便利です。据え置き型は高感度などで、真空装置を組み立てていくときに一つひとつの部品を厳しく検査するのに適しています。
硬さ試験機
物理学実験では様々な金属を使います。そして、それらの硬さを調べたいことはよくあります。
例えば、SUS630やBeCuなどのように析出硬化熱処理を行って構造物の耐力を増し、高圧容器として用いる場合、実際に目標の耐力を得たかどうかは硬さ試験機にかけて確認しなければなりません。
析出硬化熱処理は比較的低い温度(5〜600℃の電気炉でよい)で、特別な設備が無くても実施できることがメリットですが、硬さ試験機がないと信頼性が得られない・・・ということになります。
SUS304などのオーステナイト合金や、インコネルなどの鉄=ニッケル合金は加工硬化現象が大きく、加工後の加工表面の性質が変わってしまうこともよくあります。このような場合も、表面の硬さを確認できれば、加工硬化の有無を判断できます。
銅や銀などのアニール(焼きなまし)を確認するなど、硬さを調べてわかる情報はたくさんあります。
硬さ試験機 |
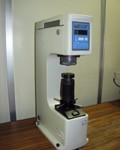 |
ひずみ計
ひずみ計はストレンゲージともいい、応力変化や圧力測定などに広く用いられています。
フィルム表面にプリントされた微細回路の抵抗値が引っ張りや圧縮などの応力によって変化するところをブリッジ回路で測定し、その部分のひずみを測定する装置で、一度に多くの場所を同時に測定することにより、機械の剛性を確認できるので、装置開発には欠かせない測定技術となっています。
ひずみ読み取り装置 | ゲージを貼り付けた板に荷重をかける |
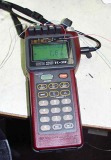 |
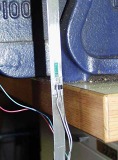 |
トルク測定器
私たちの所でトルク測定が必要になるのは、装置組み立ての品質管理です。
ボルトの締め付けトルクには適正値があり、これを管理することは精密組み立て技術のいろはです。人工衛星に搭載される装置など極限の性能を要求されるところでは特に厳しい管理が必要です。
こうした目的に用いられるのがトルクレンチです。
低温装置でよく使うインジウムシールや真空配管で用いるスウェ−ジロックではねじの締め付けトルクを細かく管理することでシールの信頼性を上げ、無用なトラブルを避けることができます。
ダイヤル式トルク測定器 | デジタル式トルク測定器 |
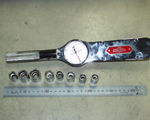 |
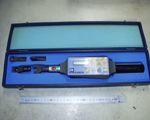 |