ASTRO-F用フーリエ分光器可動鏡駆動機構の開発を支えた技術
2003年2月 第二装置開発班、金工室 河合利秀
本編は2002年度理学部技術報告に掲載したものをWeb閲覧できるように体裁を手直ししたものです。
はじめに
ASTRO-F及び駆動機構の詳細については川田光伸さんが「ASTRO-F衛星搭載遠赤外線観測装置FISにおける技術開発」で詳しく述べておられますで、そちらをご参照ください。
写真1は、駆動機構用フーリエ分光器可動鏡駆動機構(以後単に駆動機構という)の全景である。全長約15cmほどの、小さな装置だが、駆動機構の構造は複雑である。それは、人工衛星に搭載する装置の宿命として、限られた空間に最大限の機能を実現しつつ、1gでも軽くすることと、打ち上げる際に生じる激しい振動によって壊れない強度を同時に実現しなければならないからである。
駆動機構のような装置の開発研究は、複雑な機構や部品を正確に作る技術の裏付けがあってはじめて成立する。
今回の報告は、ASTRO-F駆動機構の開発において、主に加工技術の問題をどの様に解決したかを述べるなかで、金工室と外注業者の果たした役割を整理し、大学の技術職員と町工場の技術者が協力することで、より効果的に、大学の教育研究を支えるための技術開発に貢献できることを示す。そして、協力していただいたいつかの外注業者(町工場)について、具体的にその技術を紹介する。
写真1、ASTRO-F用フーリエ分光器可動鏡駆動機構 |
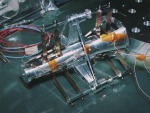 |
このページの先頭にもどる
1、複雑・精密加工の現状と課題
< 設計者と加工者の連携 >
駆動機構の開発ではこれまで何回も試作を重ねてきたが、これらの作業を進めるためには、設計と加工の緊密な連携が必要であった。
今回の開発は人工衛星に搭載するため、強度と軽さ、小ささを同時に実現することが技術的な課題であり、それに関するいくつかの部分について加工困難と思われたので、まず最初に金工室で試作し、加工の可能性や精度の問題点を確認した。駆動機構のような複雑な部品では、図面をそのまま外注業者に出しても製作困難として戻されるか、法外な見積もり金額によって暗に断わられることもある。金工室で一度試作することによって加工上の問題点を整理し、場合によっては設計変更を検討する。技術職員に求められる技術判断は、設計者と加工者の双方の立場を理解し、最良の解決策を見いだすことにあり、開発研究の成否をにぎることもあるなど、責任は大きく重い。
< 外注業者の利用 >
金工室に依頼されている仕事はたくさんあるので、それを全て自前で加工することは、時間的に不可能である。実際には加工作業のかなりの部分を外注化し、浮いた時間を設計・開発に振り向けている。従って、信頼できる外注先をいくつも持っていないと、思うように仕事を進めることはできない。
駆動機構では、半分以上の部品加工を外注加工した。表1は外注業者の一覧である。駆動機構では、これまで経験しなかったコイル巻き作業があったので、この技術分野の業者も知ることができた。
駆動機構のような複雑な装置の製作で最も重要なことは、部品どうしの整合性(ハメアイ)である。しかし、駆動機構開発の全課程を通して、ハメアイの詰めが甘く、組み合わせてみたら部品がかみ合わないことが何回もあった。こうしたことから、今回はむしろ積極的に金工室で追加加工や修正加工を施すこととし、修正加工用のジグ(補助的な固定金具や工具)を新たに作ることで、最終的な要求を満たした。
例えば、駆動機構本体を固定する部品(写真1、中央の部品)などは、基準面の無い放射状の面で中心軸と3方の支持軸を固定する構造で、中心軸の直径を50μmほど大きくする切削するために、基準面を3方の軸を受ける平面としたジグを作り、ダイアルゲージによって軸芯を合わせ、旋盤加工した。
業者名\適用 | 加工技術 | 特徴 | 仲介業者 |
イシグロ工機 | 旋盤、NCフライス盤、放電加工 | 加工一般 | 直接 |
杉山鉄工所 | 旋盤、フライス盤 | 特殊材料の加工 | マシナックス |
久野鉄鋼 | 旋盤、NCフライス盤 | 加工一般 | マシナックス |
マルマン商事 | 旋盤、NCフライス盤、放電加工 | 加工一般 | マルマン商事 |
国電機 | トランス製作 | コイル巻き | マシナックス |
表1、駆動機構に関係した外注加工業者(金工室取り次ぎ分、NCとはコンピュータ制御のこと) |
複雑形状の部品に加工精度を厳しくして外注加工を依頼すると、加工費用がかさむ。設計に加工のしやすさという観点も反映させ、同じ機能を実現しつつ加工単価を縮小することは大切である。外注先で精度を確保しようとすると高コストになってしまう場合も、金工室の追加加工によって目的の精度を確保することが可能であり、今回の駆動機構開発ではそうしたことがたくさんあったので良い勉強となった。
< 外注業者開拓の歴史 >
駆動機構の開発は、これまでになく多くの外注業者の協力が必要であった。ここでは、外注業者との関係を金工室がどのように築いてきたかを、簡単に紹介する。
金工室(旧物理金工室)ができて30年以上経過するが、これまでに出入りの工具問屋さんの紹介でいくつかの町工場に加工を依頼してきた。最初は思うような加工をしてもらえないことが多かったが、我々も町工場に足を運び、職人さんと直接話をしたり、工具問屋の担当者に加工上の問題点を指摘して、双方の満足のいくよう努めてきた。これらが現在の外注業者として育ってきた訳である。これには、工具問屋の担当者や町工場の皆さんが「大学の教育・研究のためなら」と熱心に協力してくださったことも大きい。
外注業者にとって、今作っている物が、どのような研究のどのような場所に使われるかを知ることは重要である。もしこうしたことを彼らが知っていれば、科学技術や教育・研究に貢献しているという自負や誇りをもって仕事を行ってくれるであろうし、加工や機械の専門家の立場から貴重なアドバイスをいただけることもある。科学技術や教育・研究に貢献しているという自負や誇りを外注加工業者の皆さんに持ってもらうことは、大学の教育研究を支える環境が学外にも構築されることであり、大学にとって大きなメリットとなる。このような関係を学外に構築することは我々技術職員の本分だと思う。
しかし、外注業者との関係で注意しなければならないのはトラブルである。依頼主の教員と加工業者の板挟みとなって、苦しい思いをしたことは何度もあった。一番多い事例は、注文した物が結果的には教官の要求にあわず、代金の支払いを拒否される事態であるが、粘り強く交渉して、双方の納得を得るしか方法がない。
外注業者を使う場合の問題点をまとめると、おおよそ次のようになる。
我々の側で、外注業者の能力や技術の特徴を掴んでおく必要がある。そして、@設計の意図をしっかり伝える、A加工単価を安くするための共通化や単純化を可能な限り行う、Bジグ・刃物に関するノウアウを公開する、C実験装置には特殊材料を使うことが多いので特殊材料の情報やノウハウを公開する、などは重要である。このような情報交換は日頃から外注業者と行っていると良い。
このページの先頭に戻る
2、FIS用フーリエ分光器可動鏡駆動機構の中心部品であるコイルボビンの加工
FIS用フーリエ分光器の最も重要な部品は反射鏡(可動鏡)の支持機構とその駆動機構である。駆動機構としてコイルボビンと永久磁石からなるアクチュエータを構成し、折り返しバネによる直線案内機構によって可動鏡の支持機構を構成する。コイルボビンは、中央に薄肉の円筒形状(ここにコイルを巻く)と、両側に3本づつ細く突き出た支持構造があり、コイルのリード線は支持構造の細い溝に沿って引き出される。このコイルボビンは外注業者では製作困難であろうと考え、早速金工室にてコイルボビンの試作に取りかかった。
最初の設計では、コイルボビンの内径が都合良く在庫の引き抜きパイプ(A6063)に符号していので、約半日で2個作ることができた。
物理金工室の精密旋盤(江黒鉄工所製、主軸にコレットチャック機構を採用)によって加工しているところを写真2に示す。
コレットチャックによってジグとなる真鍮丸棒を掴み、外径をミクロン単位で切削し、コイルボビンの内径とのハメアイを厳密にとった結果、双方の摩擦抵抗のみでコイルボビンを旋盤主軸に固定することができた。これにより、コイルボビンの加工が可能となり、中央部分の肉圧0.15mm以下を実現した。
写真2、コイルボビンの加工 | 写真3、ジグ直径の測定 |
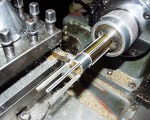 |
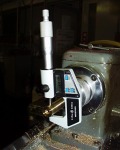 |
写真3のように、ジグとなった軸の直径はデジタルマイクロメータによって1μmの精度で測定できる。
江黒旋盤の軸受けは強制給油メタルなので、回転精度(真円度)が高いことや、コレットチャックによる材料固定の際の芯ぶれ精度が高いことから、今回のようなミクロン精度の加工にはうってつけの旋盤である。
写真4、横送り台の動きをダイヤルゲージで見る | 写真5、腕の修正加工 |
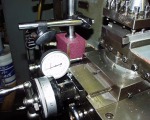 |
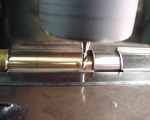 |
写真4は、江黒旋盤の横送り台の動きを1μm読みのダイヤルゲージで見ているところである。これで刃物の切り込み量を正確に読むことができ、 横送り1μmの精度で加工することが可能となる。
写真5は、外注加工で作ったコイルボビンの支持構造の細い腕の加工精度が悪かったので、フライス盤で修正をしているところである。この他にも、コイルボビン支持構造の細い腕の部分に微細な溝を入れたり、リード線の通る穴を開けるなどの追加加工を行った。修正・追加加工に要する時間は、旋盤とフライス盤を含めても1日ていどである。結果的には、外注加工を前加工工程として出すというようなセンスとなった。
コイル巻きは小牧市の国電機で行った。国電機は小型トランスの専門メーカーで、直径0.1mmの絶縁被服を施した超電導線を切れずに巻く技術をもっている。実際の作業を行ったのはアルバイトの女性従業員だが、この道20年以上のベテラン職人とのことだった。当時担当だったU研の宇津野氏と一緒に工場を見に行ったときには、キャラメル大ほどの小型トランスのボビンに、魔法仕掛けのように細い線を次々と短時間で巻く見事さに驚かさた。ここでは様々な仕様のトランスを作ってもらえるとのこと。日本の各地にこうした隠れた名人がいて、「もの作り日本」を支えているのだと実感した。
このページの先頭に戻る
3、駆動機構支持金具の加工
写真6に示す駆動機構支持金具(写真1の中央に位置する部品)は強度と軽さという矛盾した要求を同時に実現しなければならない部品で、しかも加工精度も要求される難しい。
支持金具中央の穴の精度をH7(常用はめあい、すべりばめ)と指定して外注加工したが、組みあがらない。よく調べてみると、駆動機構本体と金具の双方とも要求した精度を満たしていないことがわかった。
一回目は、加工応力が加わらないために高い精度が期待できるワイヤー放電加工としたが、中央の円筒部分の真円度が悪かった。
二回目はNC加工としが、一回目と同様、中央の穴の真円度が悪く、卵形に20μmほど変形していたので、結局、二回とも専用ジグを作って修正加工を行った。
写真6、駆動機構支持金具 |
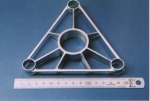 |
専用ジグは円盤状で、外周部分を加工基準面とし、ここに3点支持(写真6の三角形頂点の穴)位置に合わせた取り付け用のねじ穴をあけておく。さらに、3点支持部分の内径にぴったりと挿入できるブッシュを作り、その中央には、ばか穴をあけておく。
ブッシュを3点支持部へ挿入して、ジグにねじで仮止めし、旋盤のチャックにジグごと固定して、てこ式ダイヤルゲージで中央部分の穴の芯振れを読み、一番振れの小さくなるところで3点のねじを締め直す。以下、中繰りバイトで内径加を切削加工すればよい。横送り台の送り量はコイルボビンのジグを作ったときと同じ方法で、1μmの精度を実現できる。
この方法の良いところは、支持金具をフランジの基準面とブッシュで固定しることから、中央の部分に、曲げなどの余分な応力がかからず、加工精度がそのまま部品の精度として生きることである。
二回の外注加工における変形の原因は定かではないが、材料の残留応力か、固定時の応力による変形ではないかと考えられる。材料は何れも残留応力の少ないA7075であるが、支持金具のような輪郭と骨しか残らないような加工例では、僅かな残留応力も精度に影響するということであろう。結果論ではあるが、H7を指定したにもかかわらず誤差がマイナス側にあった(本来ならば10μm程度プラス側のはず)ので、修正加工の余地ができた。次回はこの問題を整理して、仕上げ加工の余地を明確に残した寸法で外注するようにしたい。
このページの先頭に戻る
4、位置センサーの加工
駆動機構はフーリエ分光器反射鏡の位置制御が最も重要な機能であるが、それを実現するためにはミラーの動きを検出する精密な位置センサーが必要である。人工衛星に搭載する装置はできる限り小型軽量であることが望ましいので、駆動機構専用の光干渉を使った位置センサーを試作することになった。
この位置センサーは小型で、微細加工と通常の加工の中間的な位置にあり、コストとの関係で、通常加工で押し通すことにしたが、その分、難しい加工になった。
現在、一般的に町工場で小型の部品を旋盤で加工する場合、中ぐりバイト(旋盤用の刃物をバイトと言う)の製作技術を持っていなければ、市販のバイトを使うしかない。今回の形状は、こうした市販のバイトでは製作困難なものである。金工室では「必要なバイトは自分で作る」という先代(佐野さん)からの指導で、小径の中ぐりバイトも自作してきたことから、この加工だけにしか使わないかもしれないが、専用の刃物(バイト)を自作することにした。
<バイトの製作><
このような小型中ぐりバイトは、完成バイト(粉末の高速度鋼を焼き固め、高周波焼き入れしたもの)を研削成形して作る。工具研磨盤など無いので、手で完成バイトを持ってグラインダーにあて、刃先形状を整えた後、最後に油砥石で刃付けする。
ドリルの刃先などもグラインダーに砥石にドリルを手で持ってあてて、研磨するので、要領は同じである。グラインダーは時々ドレッシング(目詰まりを取り除いたり、形が悪きなったときに成形すること)をかけて、加工面をきれいにしたりエッジ部分を成型する。
今回製作したバイトの刃先は全て工具顕微鏡によって計測した。2001年度購入した工具顕微鏡は正にこうした測定を得意とするものである。
写真7、センサー本体と小径バイト | 写真8、コリメータレンズホルダとバイト |
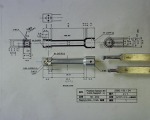 |
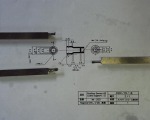 |
写真7は、位置センサー本体の図面と現物と刃物の対比したものである。この写真では、右側の内径加工を物理金工室が担当し、外形左側の四角形の加工はイシグロ工機の型放電加工機によって製作した。
イシグロ工機は熱間鍛造金型の製造を得意とする町工場で、型放電、ワイヤー放電、NCフライス盤など、高精度加工を可能とする設備を持ち、大学の実験装置の試作・製作に協力していただいている。
写真8は、コリメータレンズホルダである。この写真に示すように、コリメータレンズホルダは位置センサーの右側に中心軸がずれないように固定する。従って、この部分の加工は本体とのハメアイが厳しく(数μm以内)、且つ、内径加工の精度も厳しい。
今回の作業で4本の刃物を作った。特に右から3番目のバイトは、レンズの中心を出すためのテーパ角度(45°)と深さ(1.1mm)を決める重要なもので、工具顕微鏡によって刃先形状を正確に測定した。
このページの先頭に戻る
5、駆動機構の磁気回路部品(リターンヨーク)の加工と分解
2章で紹介したコイルボビンは、強力な磁石と対で駆動機構を構成し、折り返し平行バネによる直線案内機構によってフーリエ分光器の反射鏡を精密に動かす。この部分の動きは、コイルボビンを支えている並行バネとの連携で、直線性と位置の再現性がどれだけ実現できるかが重要である。
コイルに一様な磁場を作るため、強力な永久磁石(TDK)と電磁軟鉄製のリターンヨークによって磁気回路が形成されている。
リターンヨークの加工は、ヨークの合わせ部分に隙間があると磁気抵抗が増え、設計値通りの磁場が得られず駆動力の低下を招くことから、高い精密で加工しなければならない。
電磁軟鉄は非常に切削しにくい材料の一つで、経験豊富な職人の手が必要であるが、この加工は杉山製作所が行った。杉山鉄工所の杉山勇氏は手作りバイトを操る数少ない旋盤職人の一人で、チタン合金やモリブデン加工のスペシャリストである。今回杉山勇氏と巡り会えたことは大きな収穫であった。
最終的な組立はTDKで行ったが、内部でコイルの断線が発生するなどのアクシデントのため、メインアクチュエータを分解しなければならない事態となった。
TDKに分解作業を依頼する時間的な余裕もないことから、金工室で分解することとなった。
この作業は内部にある強力な磁石のため、簡単には分解できないばかりか、分解途中で破損する可能性もある、リスクの大きな作業である。
そこで、この分解作業を安全に行うための、コレット式のジグを作った。写真9はそのジグを用いて永久磁石とリターンヨークを分解しているところである。作業の手順は、
- 旋盤の主軸チャックによってリターンヨークの外径を固定
- 芯押し台にドリルチャックを装着しドリルチャックによって専用ジグを掴む
- リターンヨークのふたの部分を専用ジグのコレット部分に挿入してジグのネジを締め付ける
- 芯押し台のハンドルを引く方向に回す
この方法ならば、リターンヨークの中心軸を狂わすことなく、安全にリターンヨークを分解できる。
このジグは、組み立て作業の安全性も格段に高めた。手作業では強力磁石によって不用意にかみつかれる危険性が高かったが、このジグを作ったことで、最もリスクの大きい分解・組立作業が大学内でスムーズに行えるようになったことは、後の作業スケジュールを楽にした。
写真9、ジグを用いたリターンヨークの分解 |
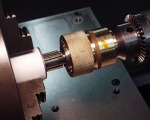 |
このページの先頭に戻る
まとめ
外注業者が作った部品は、必ず加工精度などを確認しなければならない。可能ならば、受け取りの時に業者の目の前で確認する方がよい。もし、設計図と異なっている場合は、その原因を探る必要がある。
最終的な加工精度の確認や、修正加工は、金工室で適時行なうことは重要である。今年度、ミクロンオーダーで気軽に使える三次元測定器を購入することにしたので、この点に関して、大きく前進できるのではないかと期待している。
要求される精度が高いほど、あるいは複雑な形状になればなるほど、加工技術は困難性を増すので、実際の加工上の限界を理解することは重要である。我々技術職員の側から、設計者に加工上の問題点を十分伝えることがよい装置を作る重要な条件である。今回の仕事は、こうした意味で、大学の研究現場と協力工場の職人さんとの意思疎通の重要性を再認識し、お互い得るものが多かった。
以上、紹介してきたように、駆動機構の開発にあたっては、名古屋近郊の外注業者とその協力工場のみなさんを多数動員してきた。彼らも、自分たちの作ったものが人工衛星になって飛んでいくのを今か今かと楽しみにしている。まだまだ色々なトラブルに見舞われる可能性もあるので、ASTRO-F/駆動機構が無事成果を上げられるようになるまで頑張りたいと思う。
協力してもらった外注業者の皆さんには、最低の時間単価しか支払っていない。彼らの、利益を度外視した協力には頭が下がる。今後とも彼らの協力なしには技術開発は不可能である。さらなる緊密な連携が可能になれば、大学の教育・研究にもっと貢献できるのではないかと思う。
謝辞
常々、外注業者とその協力工場の皆さんの多大な協力によって、名古屋大学の教育・研究が支えられていることを紹介したいと思っていたので、今回発表の機会を与えて下さった理学部技術研修会実行委員会の皆様に感謝いたします。
普段からお世話になっている株式会社マシナックスの佐野隆治様、マルマン商事株式会社の加藤修郎様、有限会社イシグロ工機の石黒淳治様、杉山鉄工所の杉山勇様他、作業を分担していただいた皆さんに、改めて感謝いたします。
このページの先頭に戻る
追補
- 過去の失敗から学んだこと(外注業者とのトラブル)
外注先とのトラブルをたくさん経験したので、新たな外注業者に作業を依頼する場合に注意しなければならないことについてまとめる。
- 例1、金メッキ
もう25年も前だが、事件はキャビティ(空洞共振器)に金メッキを依頼したときに起きた。
キャビティの機械加工は金工室で行い、それを仲介業者を通じてメッキ業者にお願いした。全部で2個の部品であったが、このうちの一個に非常に細いリング状のキリコとバリが残っていて、金メッキによって溶着してしまった。
2個の部品はねじ部分がはめあいになっていて、ボトムエンドはチョーク構造となっているのだが、このチョーク部分に例のキリコが付いていて、これが原因でQがあがらず、想定していた周波数ともずれてしまうことがわかり、このままでは装置に使えないと、依頼した研究者はカンカンになって怒ってしまった。そこに、相手側から加工料金の請求があったので、「払う」「払わない」のトラブルとなり、この問題を解決するのに長い時間がかかった。
メッキ業者は預かったものをそのままメッキをかけたのだから「払え」というし、研究者は使えないものにはお金を「払わない」と折り合わない。実際には、使えないことはなくて、金工室でエッジのバリを取り除くと設計通りの性能を発揮したのだが、キリコが溶着していた部分は金メッキが剥がれてしまったので研究者は納得しなかった。
このトラブルの原因は、本来なら金工室が機械加工のときのキリコを見落としたことや、メッキの受け取り検査を怠ったからである。
研究者の依頼も「この通りのものを作れ」というもので、それが何に使われるかなどの説明はなかった。形状から見てたぶんキャビティだろうというのはわかっていたのだが・・・
結局のところ、加工を依頼された仕事の大切なところをきちんと確認しなかったことや、研究者に渡す前に修正加工をすればよかったことを考えると、金工室に責任があると感じた。
- 例2、ポールピースの傷
強磁場を発生させる電磁石のポールピースを再研磨してほしいとの依頼があり、加工物が金工室の旋盤にかからない大きさだったので外注業者に加工を依頼した。
指示は単に表面を削れということで、平面度や面荒さについての指示は特にない。仕上げ面と平坦度の指示を追加して、加工業者に渡したのだが、仕上がってきたものを見ると、ポールピースの表面に傷がある。どうやら輸送途中で何かが当たって付いてしまったようだ。傷自体はそんなに深いものではなかったので、依頼主に見てもらったところ、やっぱりきれいな方がよいといって、もう一度加工してもらうことになった。
その後、この加工に対する請求書には2回分の加工費用となっていた。これも一回分なら払うとおう研究者と業者の間で折り合いが付かず、トラブルとなってしまった。
それ以来、その研究者からの工作依頼は受けづらくなり、受けたとしても簡単なことしか取り扱えなくなってしまった。
いまから考えれば、金工室がきちんと指示を出しておけば、このようなトラブルを生じなかったと思う。金工室が依頼された加工物の使われ方と加工精度との関係をつかみ、業者に説明できていれば、加工表面を保護して輸送してきたはずで、仕事を仲介した金工室の落ち度だと思う。
- 外注業者を使う場合の留意点
外注業者に加工を依頼する場合は、その装置がどのような目的でどの様なところに使われるかをよく把握し、そのときに性能を発揮するために必要な部品の寸法精度や表面荒さについて、加工業者に説明しなければならない。これは、研究者の立場よりも加工技術の現場を知る我々技術職員の方が的確に指示を出せると思う。
もう一つは、加工業者の力量をよく知ることである。新規に取引する場合は、直接工場に出向き、使用している刃物や加工途上の製品を見れば、その工場にどれほどの技量があるかを判断できる。得意な技術・不得意な技術なども分かる。こうしたことを確認した上で、的確にアドバイスすることが大切である。
以下に少なくとも合意しておかなくてはならない事項を挙げる。
- 寸法精度を明示する(クリアランスなど、はめあい記号で表示しておくのがよい)
- 加工基準面を明示する
- 表面荒さを明示する
- 面取りの指示をはっきりする
- 納期と価格を確認する
- 現物合わせの場合は相手側を渡しておく
- 些細なことでもわからないことがあれば必ず連絡してもらう
機械加工の経験に乏しい研究者が直接業者に加工依頼する場合もあるので、ここに挙げた事項は特に指示が無い場合の基準について合意してある。機械加工では常識的なものだが、その内容を以下に示す。
- 寸法精度 ±0.2mm以内(ノギスの精度)
- 穴中心の相対精度 ±0.2mm以内とし、累積誤差は不可
- 面取り 糸面
- 面荒さ Ra4〜10
- 加工上の矛盾 直ちに金工室に連絡すること
このほか、加工品の材料をきちんと確認することは重要である。同じアルミニウム合金やステンレス合金でも、用途によっては全く不向きな場合もあるので、装置や部品がどの様な目的でどの様な環境で使われるかをよく理解する必要がある。